5 reasons to choose the SLS 3D printer
After thousands of sold SLS 3D printers we learned that there are as many reasons to buy one as the number of clients and their applications. But some purposes are repeating all the time. We listed five of them.
#1 The most accessible products
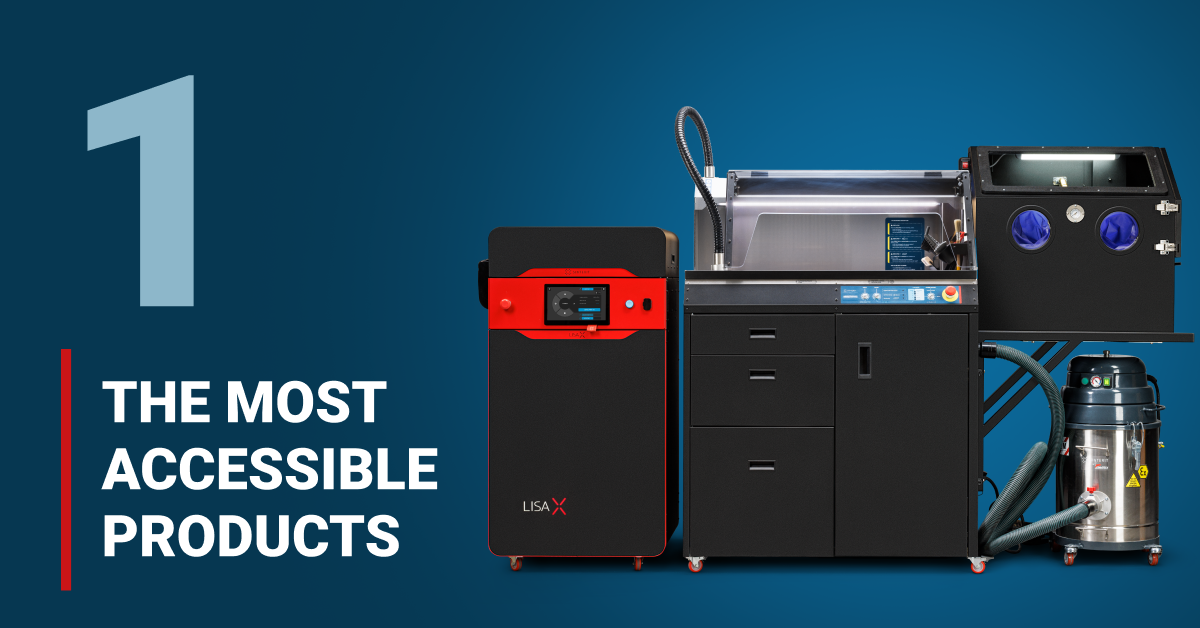
SLS 3D printing technology was associated with highly priced industrial machines that only top automotive, aviation or space companies could afford. Thankfully, after 2014s patent cliff, SLS technology become more accessible. Prices dropped from hundred thousands of dollars to less than 20k. One of the first accessible SLS 3D printers was Sinterit Lisa.
Almost ten years later, Sinterit still offers the most accessible products. With our Lisa X you have easy access to this groundbreaking technology.
If you’d like to buy a single printer, at a single price, there’s no better choice. Of course we also have different options in our full solution sets, but -to start- our offer of a “standalone printer” can be really simple. All you need to do is to consider your likely applications (or contact us and let our consultants help) and select the option that fits your needs.
What are the benefits of buying a standalone SLS 3D printer from Sinterit? Here are just few of them:
· No hidden costs.
· No mandatory service plan that you need to pay extra for.
· No additional but required modules or charged parts.
The only paid option that you may wish to consider -and only if you want to exploit full parametric control of print settings or if wishing to use any of our numerous, more specialist powders right from the beginning- is the Advancedversion of our Sinterit Studio Software.
Otherwise profiles for our standard parameters/powders are free in the basic version, which can anyway be easily upgraded at a later date.
In exchange of that you will receive:
· Industrial-grade printer from the leading compact SLS manufacturer worldwide
· Truly multi-material platform supporting up to 8 Sinterit powders, plus 3rd-party materials.
· 32 adjustable printing parameters.
· Direct support from Sinterit’s team and 50+ worldwide partners
#2 A multi-material environment
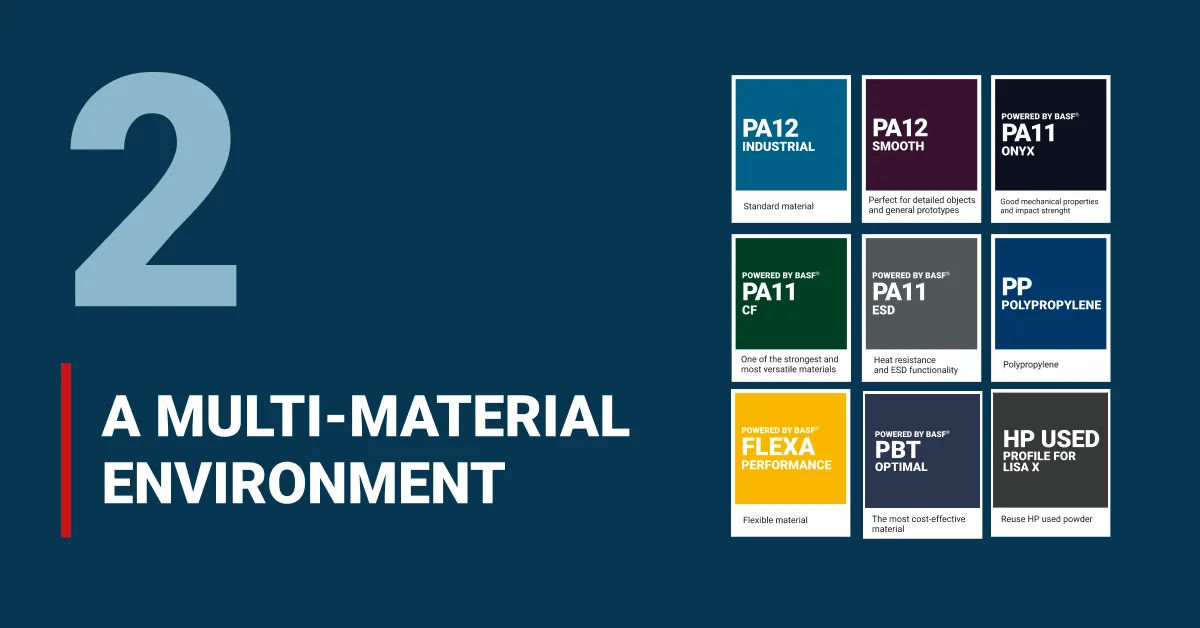
Do I need a multi-material SLS 3D printer? If you look for freedom and efficiency, the answer is simply “yes”. Sinterit’s SLS 3D printers were built not only to last, but to maximize the usability. Our R&D department worked hard to create a hardware and software environment that will make it possible to use one SLS 3d printer with different kinds of SLS powders. Now, with the widest SLS powders portfolio in the compact SLS market, Sinterit’s printers are also known for the easiest material changeover.
But 7 is not enough. We are still developing new powders. You also can experiment with third party materials. To learn more about the multi-material SLS 3D printer approach read this article.
What are the most important reasons to use a multi-material SLS 3D printer?
· Better ROI
· Increasing efficiency of processes (tooling, maintenance etc)
· Faster time to market with new products
· Enriched portfolio with new services (service providers)
#3 The most versatile platform
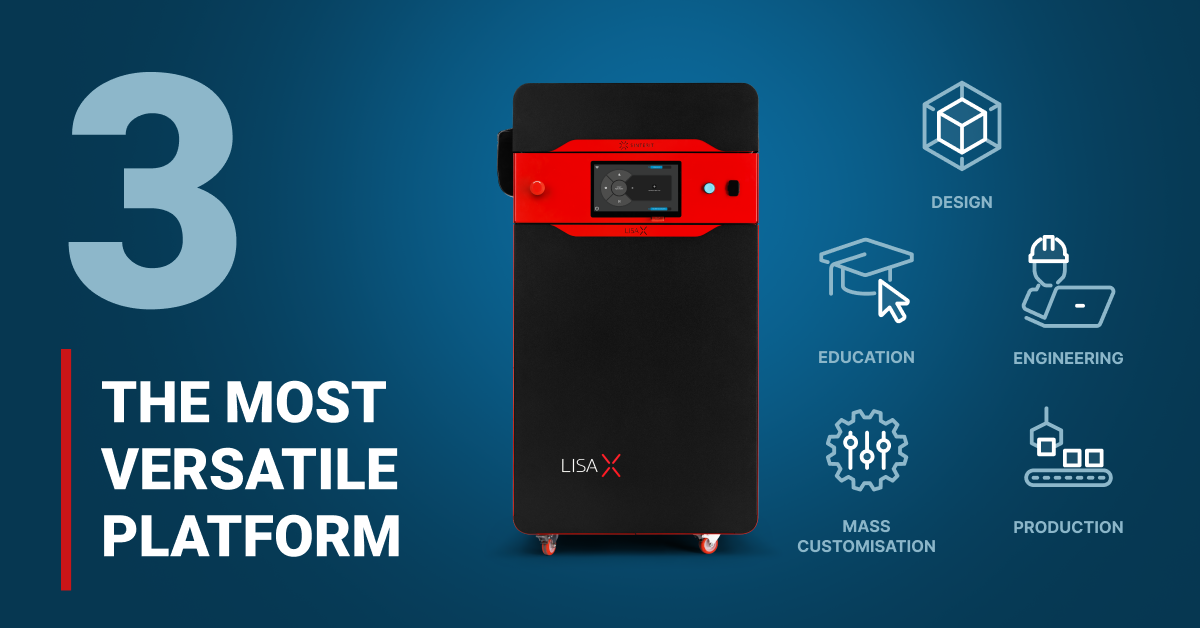
Is versatility important? It depends. If you are printing only long, cylindrical elements or use only dedicated SLS powders, without wide possibilities to change parameters or changeover the powder type between 3D printing jobs – there may be other solutions that will be interesting for you.
But if you need more versatility, use more powder types or even use less powder to print higher models (thanks to the rectangular shape of the printing bed) you should try one of the available Sinterit SLS 3D printers.
One of our cornerstones was an “easy to clean” design approach. And this is not a marketing concept, but an obvious practical benefit. For example: it takes 15 to 30 minutes to clean our biggest compact printer Lisa X. All thanks to an “easy to clean” design and step-by-step guide built into the GUI. After that you are free to use any material that your next print job requires.
At the end of the day, you could design or print versatile projects using more materials, so the number of available applications you can use Sinterit’s SLS printers for will grow.
#4 High performance solutions
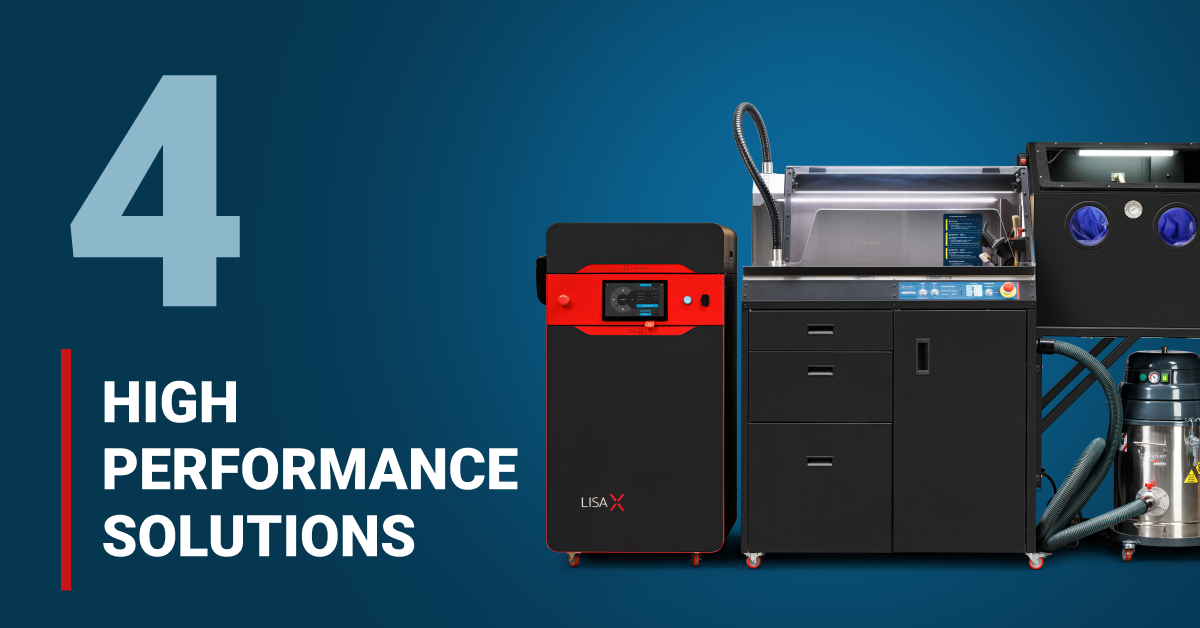
While the birth of the compact SLS 3D printing branch brought the fresh air to the market, democratized it and made it more available for average companies, the price that had to be paid for easier access to these printers was the low printing speed. But with Lisa X SLS 3D printer this problem was also solved.
That fast industrial-grade printer, Lisa X, is equipped with a 30W IR laser and a Galvo laser scanner. What does this mean for your daily operations?
Printing the full bed (130x180x340 mm for Lisa X) can be done in around 30h, and for most printouts parts will be available the next day.
Another feature that improves performance of our solution are self-check procedures. Before every new printout device is checking all crucial components to ensure that the started print job will be done correctly. This procedure includes a lifetime counter for consumable parts.
Versatility and easy-to-use approach is something that we mentioned last week, but this is worth repeating in a context of performance and productivity.
If you need to switch materials, it takes around 20 minutes to prepare Lisa X for such a change.
#5 Open environment
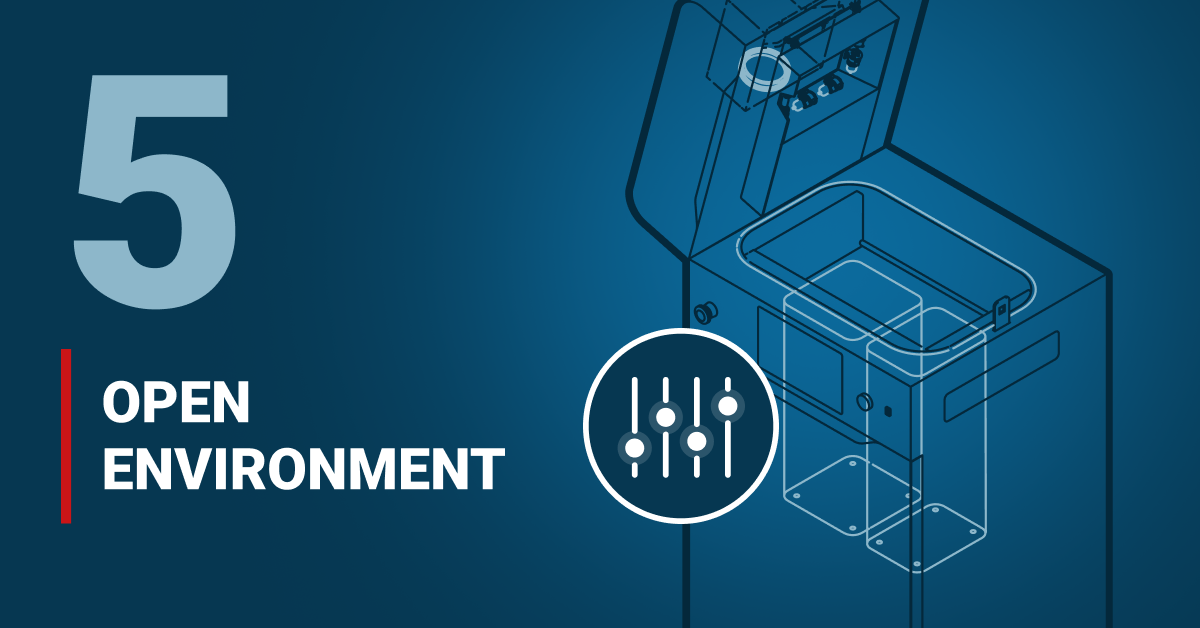
Sometimes we believe that the word “open” should be part of Sinterit’s brand name. Openness is our DNA. And when we say “open environment,” we think about a complete SLS solution, not just a printer.
For some clients, especially from the field of education, the open environment of a 3D printer is a must. Without this openness the printer could not be used for research purposes. It is understandable. To discover something, find a new solution, you need to go beyond the predefined settings.
With Sinterit Studio Advanced, we offer more than 30 printing parameters that you can adjust to achieve different effects on your print jobs. Sounds complicated? The whole system is very user-friendly and adjusting every parameter is simple and intuitive. And for those of you who don’t want to change anything we have implemented, calibrated, and ready-to-use profiles for each of our materials. So it’s not only open but also a plug & print solution.
But the hardware (SLS 3D printers) combined with software (Sinterit Studio) is just a part of the whole SLS 3D printing solution. In the offer you will also find post-processing units, like the Multi Powder Handling Station, equipped with all the tools needed to handle SLS printouts – ATEX vacuum cleaner and sandblaster.
Conclusion
With these 5 reasons in mind, feel free to contact us any time to ask for more details. All applications are different and we will be more than happy to show you the possibilities of Sinterit’s SLS 3D printing solution.