How to work with multiple materials in SLS 3D printing technology?
SLS (selective laser sintering) is one of the most comprehensive 3D printing technologies available, but only a limited number of companies use its full possibilities. Why is that? How to take full advantage of SLS 3D printing technology?
Tha main concern regarding SLS 3D printing is its availability. For years only the biggest companies could afford to buy SLS 3D printer. This situation changed not less than 10 years ago when thanks to the SLS patent cliff, compact SLS printers started to spread out in the market.
First devices had not only a very limited printing area, but also the range of materials was limited to one, two materials tops. For a long time that wasn’t a problem for two reasons.
First, those 3D printers were up to twenty times more affordable than the industrial ones. Providing wide access to technology was therefore a much greater benefit than a very limited range of materials.
Second, probably more meaningful reason was that most work done with the SLS technology focuses on the use of one specific type of powder – PA12. In the industrial world; the environment in which SLS 3D printers could handle a lot more types of powder mulitmaterial capabilities are not widely used, but, interestingly, it seems that the users of compact SLS 3D printers have a greater need to go multi-material.
Why do compact SLS 3D printers like multi-materials?
There are various aspects of compact SLS that make their users chose mulatimaterial platforms more readily:
Functionality
Different materials possess distinct physical properties, such as strength, flexibility, transparency, and conductivity. By using multiple materials, SLS 3D printing enables the creation of complex, functional parts that can perform specific tasks or meet specific requirements. For example, one part of a printed object may have a rigid structure with flexible hinges made with another material..
Customization
Multi-material SLS 3D printing facilitates customization by enabling the incorporation of different properties in one project. This capability is particularly valuable in industries such as consumer products, fashion, and design, where aesthetics and personalization are important.
Prototype Development
Prototyping is a crucial phase in product development, and multi-material SLS 3D printing allows for the creation of prototypes that closely mimic the final product’s properties. By incorporating multiple materials, designers can test different functionalities, verify form and fit, and evaluate various material combinations before committing to mass production.
Overall, the use of multi-materials in SLS 3D printing expands the range of applications, enhances functionality, and improves the overall efficiency of the printing process, making it a valuable technique for various industries.
How to deal with multi-materials in SLS?
For most of the industrial printers going multi-material doesn’t really make sense – because of the complexity of the system and their sheer size. For compact SLS it’s much easier, especially if the system was designed with a multi-material platform from the get-go. We can point three areas where we will need slightly different approaches to the handling of multiple powders.
Printing
Using different materials with one printer forces thorough cleaning of the printer between print jobs – skipping this step will lead to contaminating powders wich can make them not sinter or even – in extremal cases – damage your device. It’s very difficult to do with big industrial machines, and it might take a lot of time, more than 10h of work. For compact SLS this can be done (depanding on printer) even in 20 minutes.
Cleaning and using PHS
After the printing process, the step is the cleaning of models and postprocessing the used powder. As mentioned before, SLS technology doesn’t need additional supporting structures, as it gets the natural support from a powder that is not sintered during the process. This powder can be used over and over again during the next printing process. The easiest way to receive it is using PHS – Powder Handling Station during the cleaning process. Powder Handling Station is one of the peripheral tools that are speeding up post-processing in SLS 3D printing – it helps to clean printouts fast and easy and its role in collecting unsintered powder is priceless as it has capabilities to recover even 95% of it. PHS covers all stages of post-processing. From depowdering and cleaning, through sifting and refreshing the powder.
If you work with just one material, for example PA12, it is quite simple -just collect all the leftovers and use it once again. But what to do when you print from different types of materials? Different materials used in SLS 3D printing have not only different mechanical properties, but what is even more important, different melting temperatures. For example you need a higher temperature to melt PA12 than let’s say a TPU (like Flexa Gray).
Separating powder during post-processing is crucial. Basically PHS is designed to handle one type of powder at a time. If you want to use a different type of powder with PHS you also need to clean the unit. The cleanup won’t take you more than 60 minutes, and can save you a ton of time if you’re planning on making a couple of prints before changing the material again. If you only want to go with one build using a different material than the one the PHS is setup for, you might also consider using the Sinterit Foldable Tray on top of PHS.
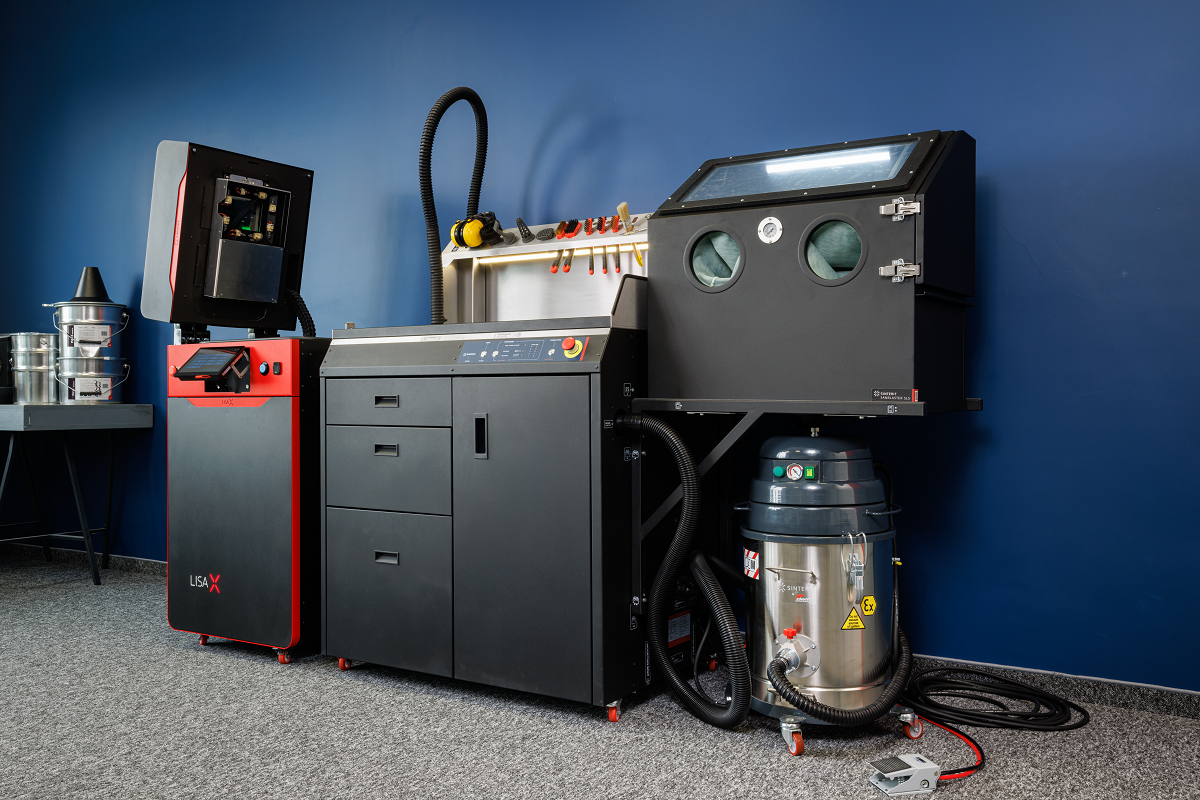
Sand blasting
Sand blasting is really the only post processing needed in SLS. It helps remove the powder residue from all the hard to reach areas as well as polishes the surface out of the loosely attached particles which allows for better dimensional accuracy. You don’t need to worry about sand blasting when using multiple materials – it doesn’t affect the sandblaster at all, so you can simply enjoy cleaning your models.
Post processing
An additional step some of the customers choose to take is one of the various types of post processing, ranging from vibratory machining, to vapor smoothing or coatings. For these additional steps it’s best to refer to the application note of the provider of the post processing to see how will it work with different types of post processing. From our experience, there are little limitations to vibratory machining or coating using multiple materials, but dying, and vapor smoothing sometimes needs to be done in separate batches.
Conclusion
Using PHS gives you a lot of flexibility and saves time. You can switch powder types even with every print job being sure that the process will be flawless.