Compact SLS 3D Printing: A New Era of Speed and Efficiency
Expectations for SLS (Selective Laser Sintering) 3D printing continue to rise – everyone wants a faster, more efficient, and truly industrial solution. However, in the world of industrial 3D printing, speed is only one piece of the puzzle. True productivity depends on several factors: reliability, print quality, material versatility, and overall process optimization. In this article, we explore how compact SLS printers live up to expectations. Is speed the ultimate priority, or do flexibility and scalability define real competitive advantage? Let’s delve into the key factors that shape truly efficient SLS 3D printing technology.
To sum up, the expectations are as follows: everyone wants to print faster. Everybody wants an industrial printer. But this is the reality: In industrial 3D printing, speed is only one piece of the puzzle. A true industrial printer must not only be fast, but also deliver disruptive quality to meet the demands of specialized sectors.
True productivity in industrial 3D printing is determined by multiple critical factors, including minimizing operational downtime, optimizing cost-effectiveness relative to performance, ensuring broad material compatibility\/agility, and maintaining high reliability.
The Game-Changing Factors in 3D SLS Printing
Every 3D printer manufacturer pursues maximum printing speed, but true efficiency requires a holistic perspective. Speed alone does not define performance. Elements like post-processing, material changeovers, and overall workflow integration must be accounted for. Imagine that with some manufacturers, material transitions can exceed 3 hours, creating significant production bottlenecks.
Where is the roadmap to optimization? How do we balance speed with the factors that truly drive industrial\/prototyping performance? Is speed the most critical factor, or is there one that holds even greater disruption?
The 10-Year Vision | What Defines a Future-Proof SLS 3D Printer?
Technology evolves exponentially, but is speed truly the defining factor? Consider alternative key drivers: third-party material compatibility and the ability to print with diverse physical properties.
Imagine investing nearly €70K in a solution where speed was the main selling point. Five years later, market demands shift, and flexibility, rather than raw speed, proves to be the true differentiator. Your system, now limited in material adaptability, is struggling to meet new industry needs, and the expected ROI remains unfulfilled.
Now, contrast this with a scalable solution: one that already operates at an industrial pace but at half the initial investment. While not the absolute fastest, such cost-effective SLS solution enables continuous integration of experimental powders and advanced materials, unlocking specialized sectors and applications. After five years, ROI is not only fully realized but doubled, and the system remains future-proof.
Which vision aligns with sustainable success?
The Repeatable Pattern – The Shift in Industrial 3D Printing Trends
This is happening more and more across Industry 4.0. Flexibility is proving to be a more critical factor than pure speed.
A striking example is Amazon’s fulfillment centers, where the deployment of over 750,000 robots has transformed logistics. These robots, optimized for tasks like package transport and sorting, have elevated efficiency and adaptability – adaptability being a key factor – enabling Amazon to meet evolving market demands without being solely reliant on speed. (Business Insider)
Similarly, BMW’s integration of humanoid robots in its production lines further underscores the dominance of flexibility. These robots, engineered for complex, revolutionary tasks, are reshaping manufacturing by prioritizing adaptability over raw speed, proving that versatility outshines speed when it comes to long-term innovation and efficiency. (The Sun)
Supercharging Industrial Speed | Killer Combinations
Reliability: The Hidden Value of Industrial SLS
Reliability, surface quality, and multi-material agility play an equally vital role in overall productivity and profitability. Industrial speed, when combined with a cost-effective solution, exceptional material handling, consistent performance, top-quality surface finish, and high-quality outputs, results in superior profitability for a business that desires to expand locally.
A truly dependable system operates with predictable consistency, maintaining precision across thousands of cycles while minimizing deviations in mechanical properties. Engineering-grade repeatability ensures that every print meets rigorous quality standards, eliminating the need for costly reworks and downtime. A robust SLS solution must integrate intelligent thermal control, precise powder distribution, and stable hardware architecture to ensure that performance remains uncompromised over years of intensive use.
Surface Quality: Precision at an Unseen Level
Surface finish in SLS printing is not just about aesthetics; it dictates post-processing efficiency, mechanical performance, and part longevity. A finely tuned laser system, combined with optimized scan strategies and uniform powder spreading, is essential for achieving exceptionally smooth surfaces with sharp details. Poor surface quality results in excessive porosity, weak bonding, and costly secondary treatments. [A well-engineered SLS system delivers near injection-molded finishes straight out of the print bed, reducing polishing, sealing, or coating requirements – critical factors in high-end manufacturing and functional prototyping.]
Multi-Material Agility: The Breakthrough of Compact SLS
Adaptability in material selection is a key differentiator in industrial SLS. The ability to switch between polymers with varying mechanical, thermal, and chemical properties allows manufacturers to serve diverse applications, from aerospace to biomedical engineering. However, multi-material printing requires precise parameter control, ensuring that each powder type sinters flawlessly under optimized conditions. A system designed for seamless material transitions, open-parameter tuning, and advanced powder refresh ratios unlocks new possibilities, enabling engineers to push the boundaries of material science while maintaining industrial-grade efficiency.
The Real Margin Builder: Quality Over Raw Speed
It’s undeniable that large-scale industrial 3D printers deliver exceptional part quality and precision, but their massive size and operational complexity come at a cost, both financially and logistically. While these systems promise high throughput, the return on investment (ROI) often stretches beyond a decade, limiting accessibility for many businesses. According to Wohlers Report, high-end industrial SLS systems can exceed €300,000-500,000 in total costs when factoring in materials, maintenance, and auxiliary equipment, making them a long-term financial commitment rather than an agile solution.
However, modern compact SLS technology is redefining efficiency. By leveraging modular printing strategies, manufacturers can split large components into interlocking sections, enabling scalability without the need for oversized equipment. This approach reduces upfront investment, accelerates break-even timelines, and enhances cost control, making low-volume production and high-mix manufacturing far more profitable.Moreover, compact industrial 3D printers enable margin expansion by maintaining the same material performance and mechanical integrity found in larger systems while offering flexibility in production. Companies that prioritize precision, surface finish, and part strength over pure build volume can capture a broader customer base, deliver repeatable, high-quality results, and maximize profitability, without waiting a decade for ROI.
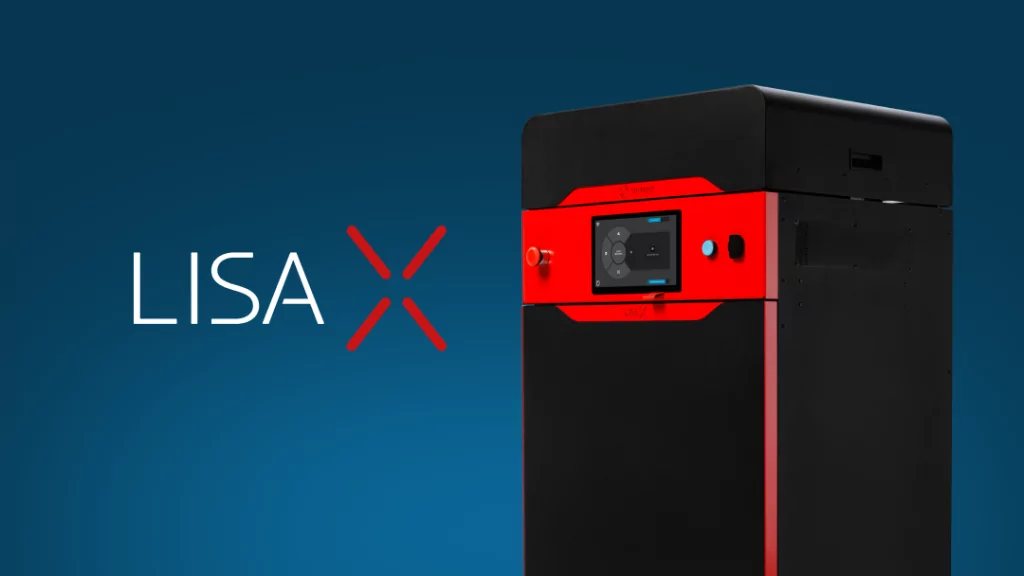
COMPACT 3D SLS: A SUMMARY OF SPEED & KEY INSIGHTS
How can the gap between speed expectations and actual outcomes in compact SLS printing impact your business strategy?
Balancing speed with material compatibility and cost-effectiveness ensures long-term efficiency and scalable growth. Industrial speed is widely available in the market.
Is focusing on faster printing the best approach, or should businesses invest in more flexible, adaptable SLS systems to future-proof their production?
Long-term value comes from adaptability, choosing the right balance of speed and flexibility drives accelerated ROI.
How does surface quality in compact SLS printing affect the cost-effectiveness of your production processes?
High surface quality reduces post-processing costs and increases mechanical performance, making it a key factor in driving overall efficiency.
What’s the real ROI of investing in a compact industrial 3D SLS system when speed is balanced with material flexibility and consistent performance?
Compact 3D SLS systems provide faster returns by offering flexibility and scalability without the massive upfront costs of huge systems.
Author: Adrian Moreno
Senior Consultant: Leads global adoption of SLS technology, helping engineers and businesses define how to achieve advanced physical properties for specialized sectors from the very first step.