What is FDM 3D printing? A guide to Fused Deposition Modeling
FDM 3D printing (Fused Deposition Modeling) is one of the most accessible and widely adopted additive manufacturing technologies in use today. It’s a cost-effective, beginner-friendly, and scalable solution — ideal for both hobbyists and industrial users. Whether you’re exploring what FDM 3D printing is or planning to implement it in a professional workflow, this technology offers an excellent balance of usability, material options, and performance.
The term FDM is often used interchangeably with FFF (Fused Filament Fabrication) — the open-source version of the same process. The difference is mostly historical and branding-related, with no functional distinction between the two.
How FDM 3D printing works
The FDM 3D printing process starts with a digital 3D model, which is sliced into layers using dedicated software. The printer’s extruder melts a filament and deposits it along predefined paths to form each layer. As the material cools and solidifies, new layers are added on top, gradually creating the final object from the bottom up.
FDM printing technology is well known for its simplicity, reliability, and ability to produce functional 3D printed parts quickly and affordably.
Materials for FDM 3D printing
One of FDM’s biggest advantages is the variety of materials it can process. These include widely available and affordable options like PLA, more durable plastics like PETG and ABS, as well as flexible or engineering-grade materials such as TPU and Nylon. Each filament type brings different properties in terms of strength, flexibility, temperature resistance, or printability, allowing users to tailor the material to the intended application.
FDM 3D printing quality & tolerances
The quality of an FDM print depends on several factors, including layer height, nozzle diameter, print speed, and cooling efficiency. While it can’t match the ultra-fine resolution of resin-based methods like SLA, FDM delivers functional and visually acceptable parts — especially when well-tuned.
Dimensional tolerances typically range between ±0.1 mm and ±0.3 mm, which is sufficient for many mechanical and design applications.
Key benefits of FDM 3D printing
FDM offers a compelling balance between cost, usability, and output quality. Its key advantages include:
- low equipment and material cost,
- easy setup and maintenance,
- wide availability of materials and printers.
These qualities make it an excellent choice for both individual makers and industrial teams looking for fast iteration and low-risk development.
Limitations of FDM 3D printing
Despite its strengths, FDM comes with certain trade-offs. The most common limitations are lower surface smoothness, visible layer lines, and potential warping or weak interlayer adhesion in some materials. Additionally, overhangs may require support structures, which add post-processing time.
However, many of these drawbacks can be managed through careful calibration, design optimization, and appropriate material selection.
SLA vs FDM 3D printing comparison
While FDM is great for producing durable, functional parts, SLA (Stereolithography) is often the better choice when high resolution and fine surface finish are required. SLA uses light to cure resin, allowing for smoother, more detailed results — though it also comes with higher costs, longer cleanup, and more complex handling. In short, FDM excels at practicality and speed; SLA excels at detail and aesthetics.
FDM 3D printing applications
From rapid prototyping to end-use production, FDM 3D printing finds applications in engineering, education, healthcare, and small-scale manufacturing. It’s a go-to method for prototyping, mechanical testing, DIY projects, custom tooling, and even low-volume end-use parts. In education, it plays a key role in hands-on learning environments, helping students understand engineering principles and digital fabrication.
FDM 3D printing diagram (visual explanation)
A typical FDM 3D printing diagram shows the key components: a filament spool feeding material into an extruder, which heats and deposits the filament through a nozzle onto a build plate. The print head moves along X and Y axes, while the platform adjusts on the Z axis to build up layers.
Understanding this setup helps explain why FDM is so straightforward to operate, yet powerful enough for serious work.
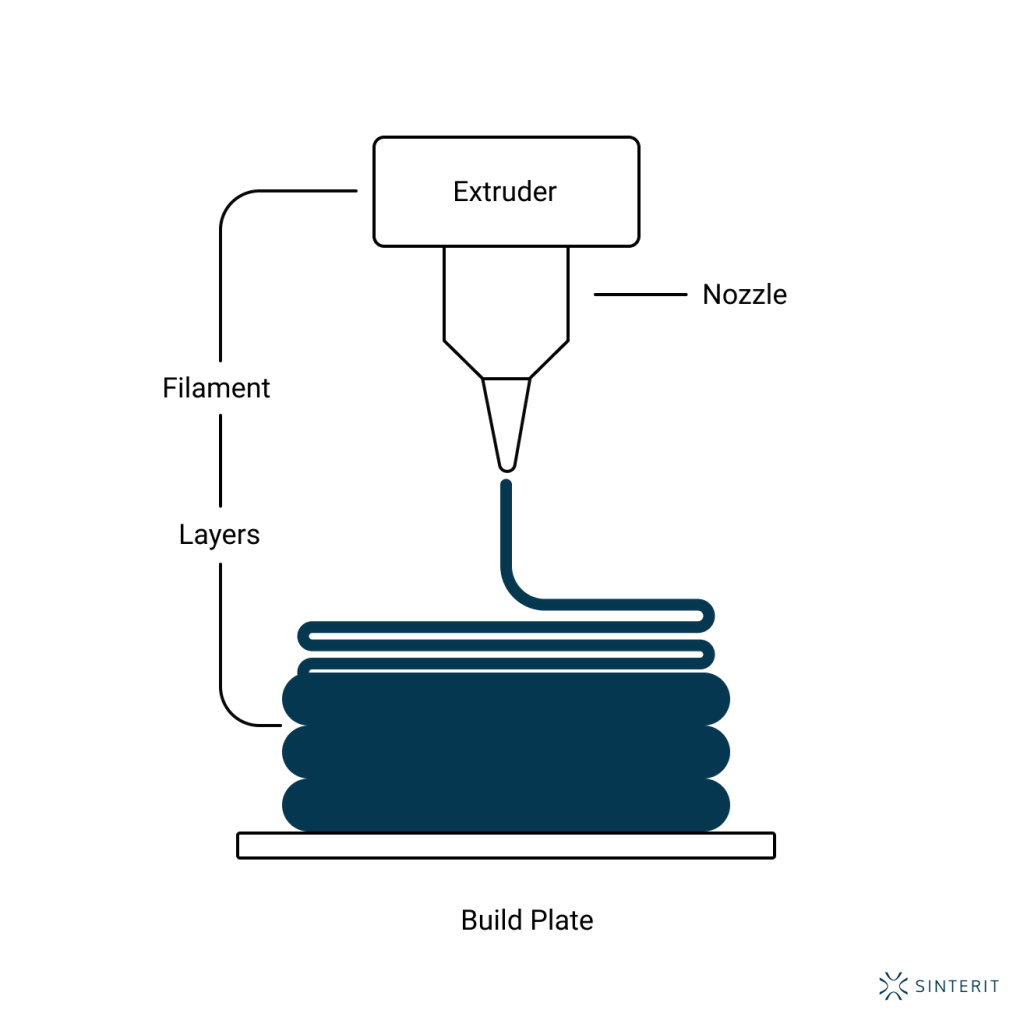
[navigation_links]
Explore also
- Overview of 3D printing tech
- What is SLS printing?
- What is SLA 3D printing?
- MJF 3D printing
- DLP 3D printing
- What is DMLS and SLM 3D printing?
Related categories