3D print SLS: what is Selective Laser Sintering and how it works
SLS 3D printing — short for Selective Laser Sintering — is an advanced additive manufacturing method that uses a high-powered laser to fuse powdered materials into solid, functional parts. Unlike filament-based (FDM) or resin-based (SLA) printing, SLS prints don’t require support structures, because the unsintered powder naturally supports the model as it’s built.
This makes 3D print SLS technology ideal for creating durable, complex prototypes and low-volume end-use components with industrial-level precision.
What is SLS in 3D printing?
SLS (Selective Laser Sintering) refers to a 3D printing process that selectively sinters powdered thermoplastics — such as PA12 or PA11 — using a laser beam.
Unlike SLA or FDM, SLS prints:
- don’t require supports,
- allow for fully enclosed internal geometries,
- enable nested parts and assemblies in a single print job.
In short, SLS printing gives designers unmatched freedom while delivering functional strength and precision.
How does SLS printing work?
Here’s a simplified step-by-step of the SLS 3D printing process:
- a thin layer of polymer powder is spread across a heated build platform;
- a laser selectively sinters the cross-section of the part;
- the platform lowers, and a new layer of powder is added;
- the process repeats layer by layer until the entire part is built;
- the part is removed from the powder cake and depowdered.
This method delivers parts with excellent mechanical properties, dimensional accuracy, and design complexity.

An SLS print refers to any object produced using Selective Laser Sintering technology. What sets SLS prints apart from other 3D printed parts is their combination of strength, detail, and freedom of design. Whether it’s a functional prototype, an end-use mechanical part, or a customized product, an SLS print delivers performance that rivals injection molding — without the tooling cost or lead time.
What is an SLS printer?
An SLS printer — also called an SLS printing machine — is a professional-grade 3D printer designed to handle powdered materials like PA12, PA11, or flexible TPUs. It consists of a powder management system, recoating blade, laser scanning system, and a temperature-controlled build chamber. SLS printers come in various sizes, from compact benchtop models to large-format industrial systems.
They are widely used in sectors such as automotive, aerospace, consumer electronics, and medical device manufacturing.
Can SLS print metal?
Standard SLS printers do not print metal, but the concept is similar.
DMLS (Direct Metal Laser Sintering) and SLM (Selective Laser Melting) are metal-compatible processes that belong to the powder bed fusion family, just like SLS.
While 3D print SLS is specific to thermoplastics, the underlying principle — selective fusion of powder via laser — is also used in metal 3D printing, just with different materials and much higher temperatures.
SLS 3D printing diagram (visual explanation)
A typical SLS 3D printing diagram would include the following components:
- powder feed system,
- recoating blade,
- build platform,
- laser scanning unit,
- heated chamber,
- powder bed.
The diagram helps visualize how each layer is selectively fused by the laser within the bed of powder, and how the part is later removed from the unsintered surroundings.
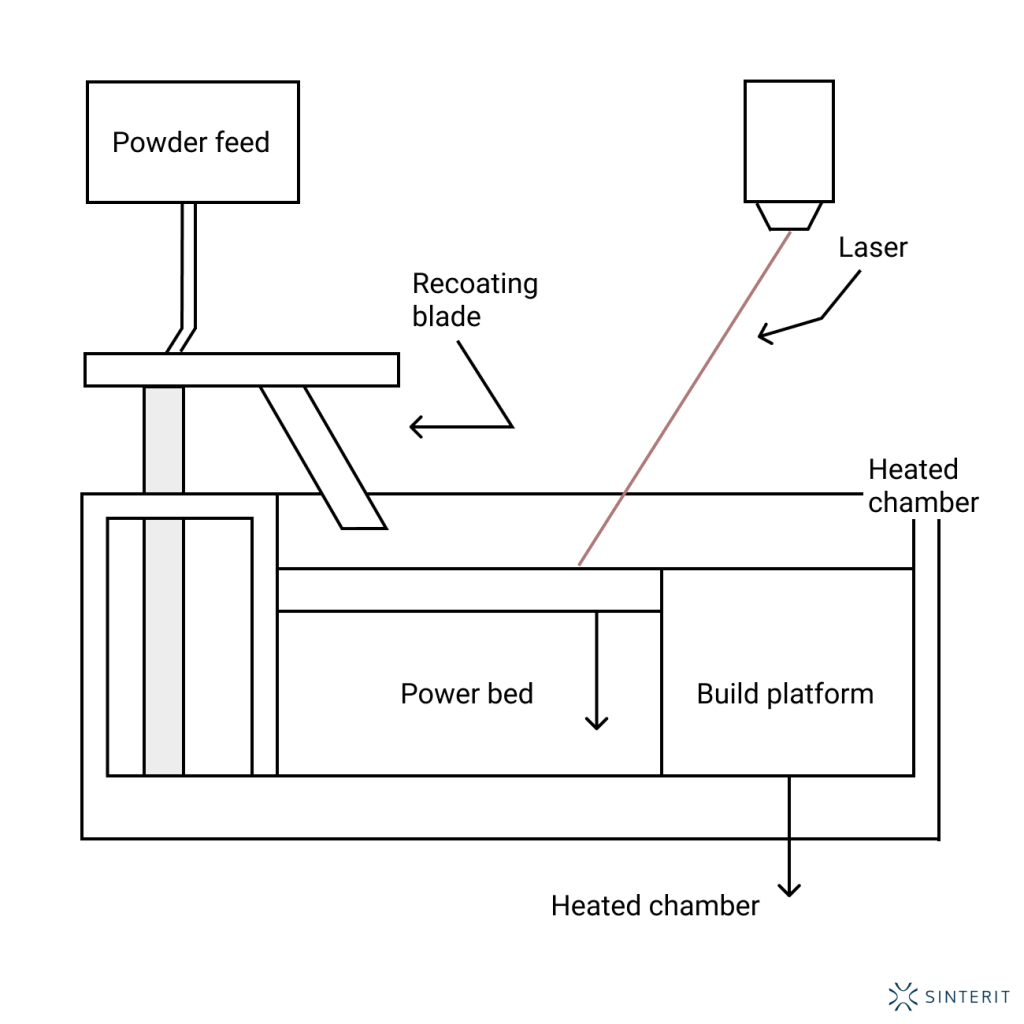
Why choose SLS printing?
SLS offers a unique combination of material performance, design freedom, and production-grade results. It’s one of the few 3D printing technologies capable of producing complex, durable, and precise parts without any support material—making it both efficient and cost-effective for small to medium batch production.
Whether you’re developing functional prototypes, spare parts, or end-use components, SLS 3D printing technology gives you industrial capabilities in a compact, additive workflow.
What makes a good SLS print?
A successful SLS print combines material performance, dimensional accuracy, and process control. While Selective Laser Sintering offers more freedom than most 3D printing methods, achieving consistently high-quality SLS prints depends on several key factors — from file preparation to post-processing.
First, part orientation and nesting strategy significantly influence surface finish and structural strength. For optimal results, SLS parts should be oriented to minimize stair-stepping on critical surfaces and to balance heat distribution within the build chamber. Efficient nesting also allows for multiple SLS prints in a single job, maximizing throughput.
Next, material selection plays a critical role. High-performance powders like PA12 and PA11 offer excellent mechanical strength, thermal resistance, and durability — making them ideal for functional prototypes and end-use parts. For applications requiring flexibility or impact absorption, TPU-based powders are commonly used.
Consistent powder refresh rates, precise laser calibration, and thermal stability in the build chamber are also essential for minimizing warping, ensuring uniform layer bonding, and maintaining dimensional tolerance. These factors determine whether a part performs like an injection-molded equivalent — or fails under load.
Finally, post-processing steps such as depowdering, bead blasting, and dyeing not only improve the appearance of the SLS print but also enhance its usability and fit in assembled systems.
In short, a good SLS print is the result of optimized print parameters, high-quality materials, and careful process control — turning digital designs into strong, reliable, and production-ready components.
Applications of SLS prints
Because of their excellent mechanical properties, design flexibility, and production efficiency, SLS prints are widely used across industries where performance and precision matter.
One of the most common applications is the creation of functional prototypes. Unlike simple visual models, these parts are built to be tested in real-world conditions — under stress, motion, or heat — thanks to the strength and stability of materials like PA12 Smooth or PA11 Onyx. Engineers use 3D print SLS workflows to quickly iterate, test fit and function, and validate designs before moving to full-scale production.
Low-volume manufacturing is another area where SLS printing excels. Traditional tooling methods like injection molding can be cost-prohibitive for small batches. With SLS, manufacturers can produce high-quality, end-use components without molds, significantly reducing lead times and tooling expenses. This makes it an ideal solution for bridge production, custom parts, or spare components.
In automotive and aerospace, SLS prints are valued for their ability to meet tight tolerances and deliver lightweight, durable geometries. Components such as clips, housings, ducts, and enclosures can be printed on demand, reducing inventory needs and enabling just-in-time production strategies.
The medical field also benefits from SLS’s design freedom and biocompatible materials. Customized orthotics, prosthetics, surgical tools, and even anatomical models are now routinely produced using powder-based 3D printing technologies.
Whether for prototyping or production, an SLS print offers a unique combination of quality, speed, and design agility that few other manufacturing technologies can match.

SLA vs SLS 3D printing – key differences
While both SLA and SLS are considered high-precision 3D printing technologies, they differ significantly in materials, applications, and operational needs. SLA (Stereolithography) uses a light source to cure liquid resin into highly detailed parts with smooth surfaces, making it ideal for visual prototypes, dental models, and intricate designs. SLS on the other hand, works with powdered thermoplastics to produce strong, functional parts with excellent mechanical properties—without requiring support structures. SLA is best suited for aesthetic and small-scale applications, while SLS excels in industrial-grade, performance-driven use cases where strength and durability are key.
Feature | SLA (Stereolithography) | SLS (Selective Laser Sintering) |
---|---|---|
Material type | Liquid photopolymer resin | Thermoplastic powder (e.g., PA12, PA11) |
Support structures | Required | Not required (powder acts as support) |
Surface finish | Very smooth | Matte, slightly rough |
Detail and resolution | Extremely high (excellent for fine features) | High, but slightly less detailed than SLA |
Mechanical strength | Moderate | High (suitable for functional parts) |
Post-processing | Requires cleaning and UV curing | Requires depowdering |
Design freedom | Limited by support requirements | Excellent (supports complex and nested geometries) |
Best for | Prototypes, dental, jewelry, visual models | Prototypes, end-use parts, mechanical components |
Printer maintenance | Medium (resin handling and cleaning) | Higher (powder handling, temperature control) |
Common industries | Dental, medical, design, education | Aerospace, automotive, consumer products, engineering |
To see how 3D print SLS is applied in real-world cases, visit our 3D printing examples page.
[navigation_links]
Explore also
- Overview of 3D printing tech
- What is FDM 3D printing?
- What is SLA 3D printing?
- MJF 3D printing
- DLP 3D printing
- What is DMLS and SLM 3D printing?
Related categories