Do PA12 Nylons Differ? Understanding the variations.
Table of Contents
- Introduction
- Where Can We Find PA12’s Friend?
- To the Point – Variations Among PA12 Materials
- Sinterit’s PA12s: PA12 Industrial vs. PA12 Smooth
- Summary – Q&A
Introduction
Selective Laser Sintering (SLS) printing is changing the game in additive manufacturing, and Polyamide 12 (PA 12) is one of its star players. Known for its strength, durability, and versatility, PA 12 is a go-to material for creating everything from prototypes to end-use parts. While SLS technology offers a wide range of materials, my experience shows that the majority of SLS enthusiasts tend to focus on PA 12 powder. Its excellent balance of durability, flexibility, and ease of printing makes it a go-to choice for a variety of applications. With the rising demand for industrial 3D printing solutions, understanding PA 12 powder properties and its variations is crucial for achieving high-quality 3D printed parts. Let’s dive into why this material is so important.
Where can we find our PA12 friend?
PA 12 material in SLS printing is like the Swiss Army knife of 3D printing – it’s incredibly versatile across a wide range of industries.In the automotive sector, for example, PA 12 is used to create lightweight yet tough components like air ducts, cable housings, and even custom brackets. These parts not only reduce vehicle weight, improving fuel efficiency, but also stand up to chemicals, and mechanical stress. The growing adoption of 3D printed car parts is making PA 12 a preferred choice for functional automotive components.
Over in aerospace, PA 12 is a go-to for manufacturing complex parts like aircraft interior parts and fuselage structural parts, housings or cabin accessories. Its high strength-to-weight ratio and ability to meet strict industry standards make it a perfect fit for applications where every gram counts.
In healthcare, PA 12 is making also significant impact. Its biocompatibility and precision allow for the production of custom prosthetics, orthotics, and surgical guides tailored to individual patients. The material’s smooth surface finish and sterilizability make it ideal for medical applications that has no contact with alive tissue or body fluids.
PA 12 is also a popular choice in consumer goods. From wearable tech to high-end eyewear and custom-fit footwear, it’s enabling designers to push the boundaries of innovation while maintaining durability and comfort.
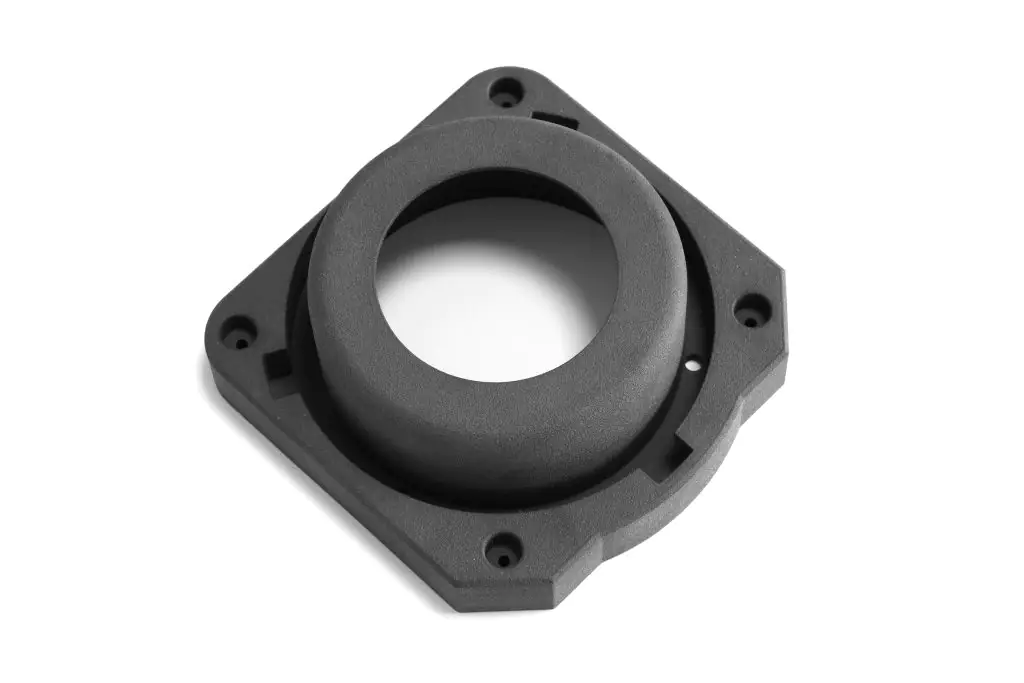
Industrial applications use the material to produce jigs, fixtures, and tooling that can withstand heavy use in manufacturing environments. For example, automotive assembly lines use PA 12 tools for repetitive tasks because they’re lightweight, durable, and resistant to wear and tear. PA 12 for industrial prototyping and functional 3D printed tools are reshaping production workflows, enabling faster design iterations and enhanced performance.
Additionally, PA 12’s ability to create complex geometries with high accuracy makes it a favorite for functional prototypes across industries, allowing engineers to test and iterate designs quickly. With its tensile strength and elongation at break, PA 12 strikes a perfect balance between flexibility and strength, making it a reliable choice for both prototyping and end-use parts. Whether you’re building a car, a plane, or a custom medical device, PA 12 is the material that gets the job done with precision and reliability.
To the point – variations among PA12 materials
While PA12 nylon might seem like a one-size-fits-all material at first glance, the truth is, not all PA12 (Polyamide 12) nylons are the same – they can vary significantly depending on their formulation and additives. While the base material is consistent, manufacturers often modify PA12 to enhance specific properties, such as strength, flexibility, thermal resistance, or surface finish. For example, some PA12 materials are reinforced with glass or carbon fibers to increase stiffness and strength, making them ideal for high-stress applications in aerospace or automotive industries. Others might include additives like flame retardants for use in electrical components or colorants for aesthetic purposes. Additionally, the powder particle size and distribution can differ, affecting the resolution and surface quality of SLS-printed parts. So, while all PA12 nylons share core characteristics like durability and chemical resistance, their performance and suitability for specific tasks can vary widely based on how they’re engineered. So, while PA12 is consistently reliable, the “right” PA12 for your project depends on what you’re trying to achieve. Always check the datasheet to make sure you’re picking the one that fits your needs!
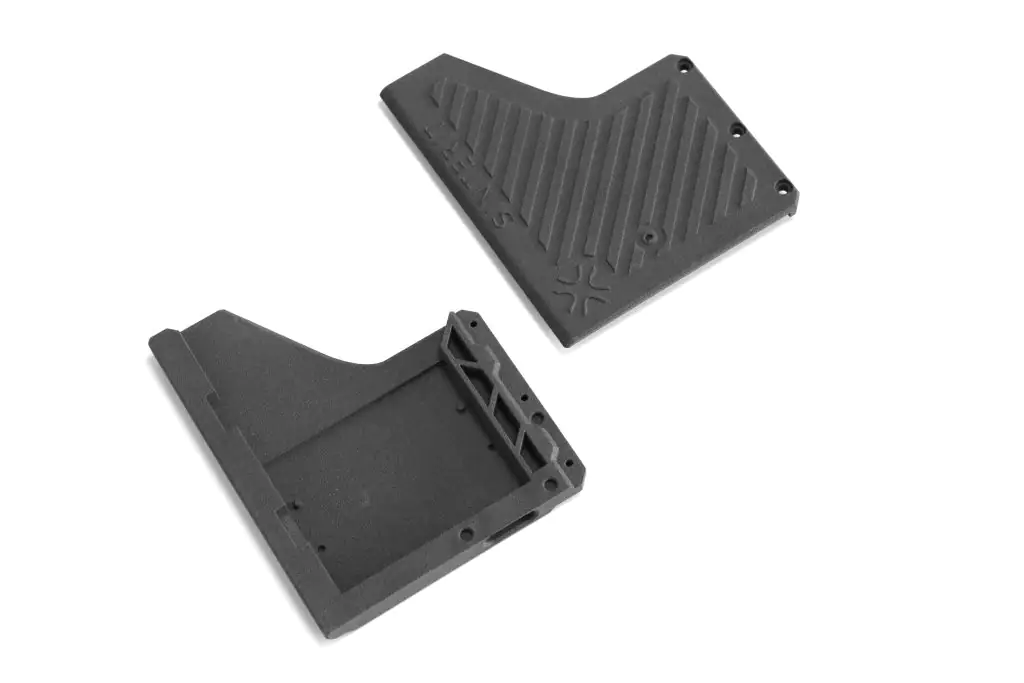
Sinterit’s PA12s: PA12 Industrial vs. PA12 Smooth
When comparing Sinterit’s PA12 Smooth and PA12 Industrial, both materials are excellent choices for SLS printing, but they cater to slightly different needs and applications. Let’s break it down so you can decide which one works best for your project:
PA12 Smooth
- Best for: High-detail, aesthetic-focused parts.
- Surface Finish: As the name suggests, PA12 Smooth is all about delivering a sleek, almost polished surface right off the printer. It’s perfect for parts where appearance matters, like consumer products, prototypes, or design models.
- Applications: Think ergonomic designs, custom-fit products, or anything where a smooth, professional look is key.
- Ease of Use: It’s user-friendly and works well for both beginners and experienced users who want reliable results without extra post-processing.
PA12 Industrial
- Best for: Functional, durable parts that need to withstand tough conditions.
- Strength and Durability: PA12 Industrial is engineered for heavy-duty applications. It’s stiffer and more robust than PA12 Smooth, making it ideal for mechanical parts, tools, or components that face stress, friction, or harsh environments.
- Thermal and Chemical Resistance: It performs well under higher temperatures and exposure to chemicals, so but for higher expectations, it’s better to go for PA11 here.
- Applications: Think jigs, fixtures, functional prototypes, or end-use parts that need to last.
- Post-Processing: While it might not have the same “out-of-the-printer” smoothness as PA12 Smooth, it’s still a high-quality material that can be finished further if needed.
Which One Should You Choose?
- Go for PA12 Smooth if you’re focused on aesthetics, flexibility, and ease of use – perfect for design-driven projects or prototypes.
- Choose PA12 Industrial if you need strength, durability, and resistance to tough conditions—ideal for functional parts in demanding environments.
Both materials are fantastic in their own right, so it really comes down to what your project requires. If you’re ever in doubt, Sinterit’s material datasheets are a great resource to dive deeper into the specifics!
For a deeper dive into the specifics of PA12 Smooth and PA12 Industrial, don’t forget to download the material datasheets—they’re packed with all the details you need to make the best choice of the material.
Summary – Q&A
Q: Why is PA12 so popular in SLS 3D printing?
A: PA12 is a go-to material for SLS 3D printing because it’s strong, durable, and versatile, making it suitable for various industries.
Q: Are all PA12 nylons the same?
A: No, not all PA12 nylons are the same. They can vary greatly depending on the formulation, additives, and even the particle size, which affects their properties and applications.
Q: What are some common variations of PA12?
A: Some PA12 materials are enhanced with glass or carbon fibers for added strength, while others may include flame retardants or colorants for specific applications.
Q: How do Sinterit’s PA12 Smooth and PA12 Industrial differ?
A: Sinterit offers two PA12 variants: PA12 Smooth, which is ideal for aesthetic applications with its fine surface finish, and PA12 Industrial, which is designed for toughness and mechanical performance.
Q: How do I choose the right PA12 for my project?
A: The key is to match the PA12 material to your project’s needs, whether that’s for aesthetics, flexibility, or heavy-duty performance. Always check the material datasheets to find the best fit for your specific requirements.
Author: Monika Jurek
SLS 3D Customer-Centric Associate with two years of experience working with companies worldwide. She specializes in helping businesses identify optimal solutions for implementing 3D printing using SLS technology.