What is SLA 3D printing?
SLA, or Stereolithography, is one of the oldest and most precise 3D printing technologies available today. It uses a focused light source—typically a UV laser or projector—to cure liquid resin into solid layers, building detailed parts with smooth surfaces. SLA is especially valued for its exceptional resolution, fine details, and clean finish, making it ideal for applications where surface quality matters.
How does SLA 3D printing work?
The SLA printing process starts with a tank filled with liquid photopolymer resin. A laser or light projector selectively cures the resin, tracing the first layer of the object onto the bottom of the tank. The build platform then lifts slightly, allowing the next layer to be exposed and cured. This process repeats until the full object is formed, suspended upside down from the build platform.
This technique offers highly accurate, intricate results and is particularly useful for creating prototypes, molds, miniatures, and dental or medical models.
SLA meaning in 3D printing
In the context of 3D printing, SLA stands for Stereolithography Apparatus. It’s a method based on the principle of photopolymerization, where light is used to turn a liquid into a solid, one layer at a time.
SLA 3D printing materials
SLA uses specialized photopolymer resins that cure when exposed to UV light. These resins come in various types, including:
- standard resin – good for general prototyping,
- tough resin – designed for strength and impact resistance,
- flexible resin – offers elasticity similar to rubber,
- castable resin – used in jewelry or dental molding,
- biocompatible resin – for medical and dental applications.
Material properties vary in terms of durability, flexibility, clarity, and heat resistance.
SLA 3D printing resolution and accuracy
One of the key advantages of SLA 3D printing is its exceptionally high resolution. SLA printers can achieve layer heights as fine as 25 microns, producing smooth, near-injection-molded surfaces. Fine details such as sharp corners, embossed text, and complex geometries are reproduced with great accuracy, making SLA a top choice for design validation and precision modeling.
SLA 3D printing process and tips
The full SLA process includes three main stages: printing, post-processing, and curing. After printing, the part must be washed (typically in isopropyl alcohol) to remove uncured resin, then UV-cured to reach its full mechanical properties.
SLA printing tips for better results:
- Keep the resin tank clean and the optical window dust-free.
- Orient parts to minimize suction forces and support marks.
- Always post-cure for full strength and durability.
- Store resin properly to avoid degradation.
SLA 3D printing cost and speed
SLA printing speed depends on the part’s height and exposure time per layer. It’s generally slower than FDM but faster than it seems for detailed models, since each layer can be exposed quickly. SLA printing time is also influenced by post-processing and curing steps.
As for SLA 3D printing cost, resin is typically more expensive than filament, and the machines themselves can range from entry-level desktop systems to high-end industrial platforms. Costs are justified by the high quality and accuracy of printed parts.
Applications of SLA 3D printing
SLA printed parts are used in industries where fine detail and accuracy are essential. Applications include:
- dental and orthodontic models,
- medical device prototyping,
- medical device prototyping,
- jewelry casting and master molds,
- product design and concept validation,
- miniatures, figurines, and collectibles.
SLA’s ability to handle intricate shapes and sharp features makes it invaluable in precision-focused fields.
SLA vs DLP 3D printing
SLA and DLP are both resin-based printing technologies, but differ in how they cure resin. SLA uses a laser to trace each layer, while DLP cures an entire layer at once using a digital light projector.
DLP is typically faster for small prints and consumes less energy per layer, but SLA generally offers smoother surfaces and slightly better resolution in complex geometries. The choice between them depends on whether you prioritize speed (DLP) or finish and detail (SLA).
SLA 3D printer parts and machine structure
A typical SLA 3D printing machine includes:
- a resin tank that holds the liquid photopolymer,
- a build platform that lifts the part out of the resin,
- a light source (UV laser or projector) to cure each layer,
- a motor system to raise and lower the build platform,
- a control unit and cooling system to manage the process.
The simplicity and precision of the setup contribute to the clean detail and reliable results that SLA is known for.
SLA 3D printing diagram (visual explanation)
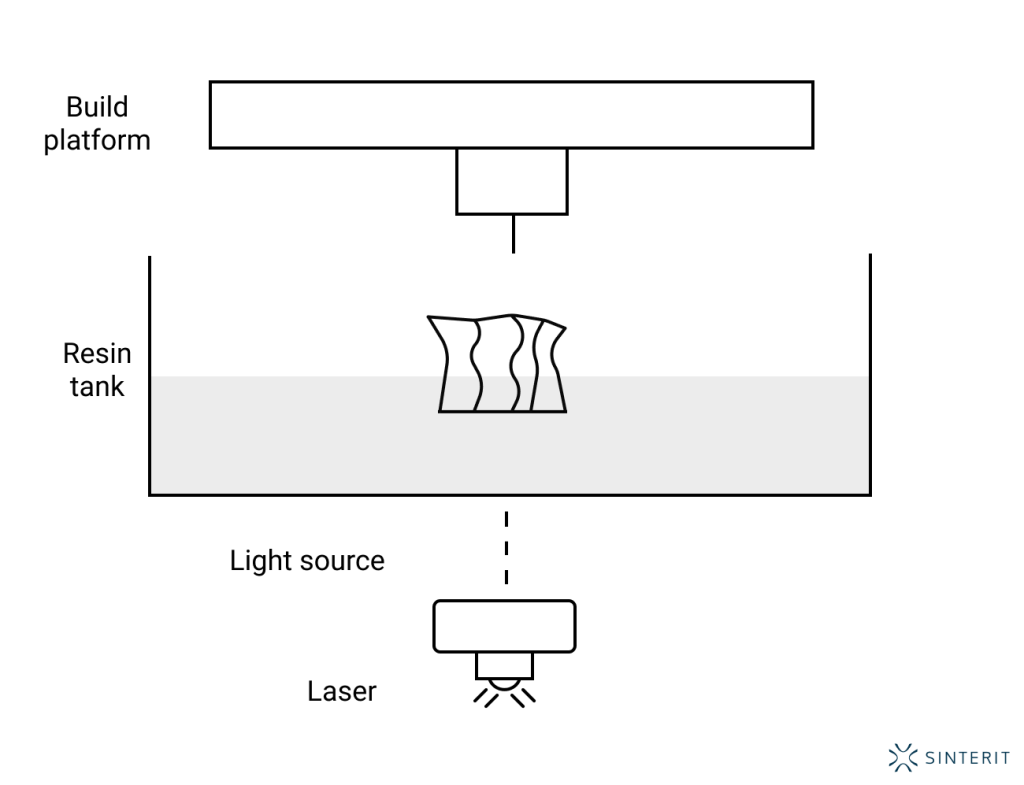
This visual breakdown helps users understand how an object grows upward, suspended above the tank, one cured layer at a time.
SLA is a cornerstone of high-resolution 3D printing. Whether you’re working in design, healthcare, or engineering, SLA 3D printing technology offers unmatched detail, clean surface finishes, and reliable dimensional accuracy — all from a compact, digitally controlled process.
[navigation_links]
Explore also
- Overview of 3D printing tech
- What is SLS printing?
- What is FDM 3D printing?
- MJF 3D printing
- DLP 3D printing
- What is DMLS and SLM 3D printing?
Related categories