SLS 3D Printing: The Quick-Reaction Model for Crisis Situations
In times of crisis, the speed and efficiency of our response can mean the difference between life and death. This is where SLS 3D printing solutions shine, offering significant advantages over traditional manufacturing methods in disaster relief efforts.
The Role of SLS Technology in Crisis Response During the COVID-19
The COVID-19 pandemic put an immense strain on global healthcare systems, revealing critical vulnerabilities in medical supply chains. One of the technologies that played a crucial role in crisis response was Selective Laser Sintering (SLS), a form of additive manufacturing that enables the production of durable and precise components. Thanks to its flexibility and speed, SLS technology allowed medical professionals and engineers to address urgent needs on time. Below, we explore some of the most impactful applications of SLS during the pandemic.
One of the earliest and most widely recognized implementations of SLS during the COVID-19 crisis was the production of ventilator valves. In the early days of the pandemic, hospitals in Italy faced a dire shortage of ventilator components, essential for treating critically ill patients. Engineers from the company Isinnova stepped in, utilizing SLS technology to quickly produce these life-saving parts locally, preventing ventilator malfunctions and saving countless lives.
As Cristian Fracassi, CEO of Isinnova, stated, “We had no choice but to act fast. With 3D printing, we were able to deliver crucial components in record time, and that made all the difference.”
SLS 3D Printing as a Game-Changer in Medical Supply Chains During the Pandemic
This showed how the use of SLS technology helped optimize medical supply chains. The pandemic exposed severe weaknesses in traditional manufacturing and distribution networks, leading to shortages of essential equipment. To mitigate this issue, companies specializing in SLS printing, such as Technology Applied, played a key role in decentralizing production. By leveraging additive manufacturing, these companies enabled the rapid fabrication of critical medical components in hospitals and emergency facilities. This reduced dependency on international suppliers and ensured a steady flow of necessary equipment.
Beyond replacing essential components, SLS was also instrumental in producing customized medical tools. The pandemic required healthcare providers to adapt to new challenges rapidly, often necessitating specialized instruments tailored to specific situations. SLS printing allowed for the rapid prototyping and fabrication of these tools, ensuring that medical staff had access to equipment designed to meet their unique needs. The ability to manufacture customized solutions on demand proved invaluable in hospitals and research centers dealing with COVID-19 patients.
Additionally, SLS 3D printing materials were crucial in manufacturing protective shields. A great example of this is Sinterit’s response to the growing demand for them in hospitals. Sinterit joined the Additive Manufacturing movement to print and assemble face shields.
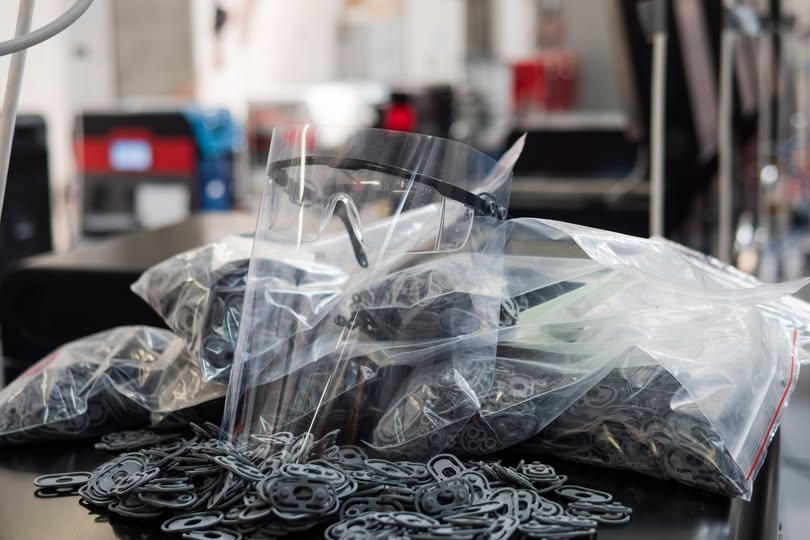
SLS 3D Printing in PPE Innovation and Pandemic Preparedness
Furthermore, SLS technology contributed to the development of advanced personal protective equipment (PPE). Traditional methods of PPE production struggled to keep pace with skyrocketing global demand, leading to shortages that put frontline workers at risk. Companies and research institutions turned to SLS printing to produce ergonomic and high-performance face shields, masks, and other protective gear. These 3D-printed PPE solutions were often more durable and reusable than their mass-produced counterparts, providing healthcare workers with superior protection against infection.
Lastly, the pandemic spurred research into antibacterial and antiviral materials for SLS printing. Scientists at the University of Wolverhampton developed innovative metal-based powders containing copper, silver, and tungsten, known for their antimicrobial properties. These new materials were used to print hospital surfaces, door handles, and filtration systems, reducing the risk of viral transmission in medical environments. By integrating these materials into 3D-printed objects, researchers created a safer and more hygienic space for both patients and medical staff.
The COVID-19 crisis demonstrated the transformative power of SLS technology in emergency response. SLS helped mitigate supply chain disruptions by enabling rapid, decentralized production of vital medical components and ensured that life-saving equipment was available when and where it was needed most. As the world continues to recover from the pandemic, the lessons learned from these applications of additive manufacturing will undoubtedly shape the future of healthcare logistics and crisis preparedness.
Warfare conflicts
The role of SLS 3D printing technology in modern warfare, particularly in conflict zones like Ukraine, cannot be overstated. However, it is crucial to critically assess the implications and limitations of its applications. While the potential for 3D printing to revolutionize military logistics and equipment is evident, there are significant concerns regarding reliance on these technologies in high-stakes environments.
- One of the more immediate applications that may be printed using SLS technology includes bleeding control bandages. While these can provide critical first aid in combat situations, their effectiveness is contingent upon quality control and material integrity – factors that can be compromised under battlefield conditions.
- Moreover, dedicated “periscopes” and optical meter devices designed for urban combat highlight a growing trend toward modularity; however, the rapid production of such devices raises questions about durability and reliability when lives are on the line.
- Additionally, uniform accessories such as hooks, buckles, and protectors are essential for soldiers operating in urban areas where standard protective gear may not suffice. The absence of adequate elbow and knee protection could severely limit a soldier’s operational capability – yet relying on 3D-printed solutions for such critical components risks compromising safety.
- Firearm modifications – including front sights and stocks tailored to specific battlefield distances – are another area where SLS technology shows promise. Yet this adaptability must not come at the expense of proven engineering; hastily produced components could lead to malfunctions when precision is paramount.
- Light reconnaissance drones represent an exciting frontier but also underline a concerning trend: reliance on potentially fragile technologies that may not withstand rigorous combat scenarios. Similarly, mortar projectile flight devices or signal transmitters for mines require stringent testing before they can be deemed reliable enough for field use.
- Casings for communication devices like walkie-talkies or observation radars exemplify how SLS can aid in quick deployment; however, they also highlight an over-reliance on rapid production methods that might overlook essential design considerations.
- While additional equipment enhancements for combat vehicles promise increased efficiency during repair operations or quick replacements, it’s vital to remember that battlefield success relies heavily on tried-and-true methodologies rather than experimental technologies alone.
- Lastly, innovations like quick reaction containers housing 3D labs or grapplers designed for sapper robot arms present intriguing possibilities but must be approached with caution. In modern warfare’s unpredictable landscape, embracing new technologies should never overshadow the fundamental principles of military strategy and proven tactics. As we navigate this complex terrain where innovation meets necessity, it’s imperative to remain vigilant about what truly enhances our capabilities versus what simply serves as a technological novelty.
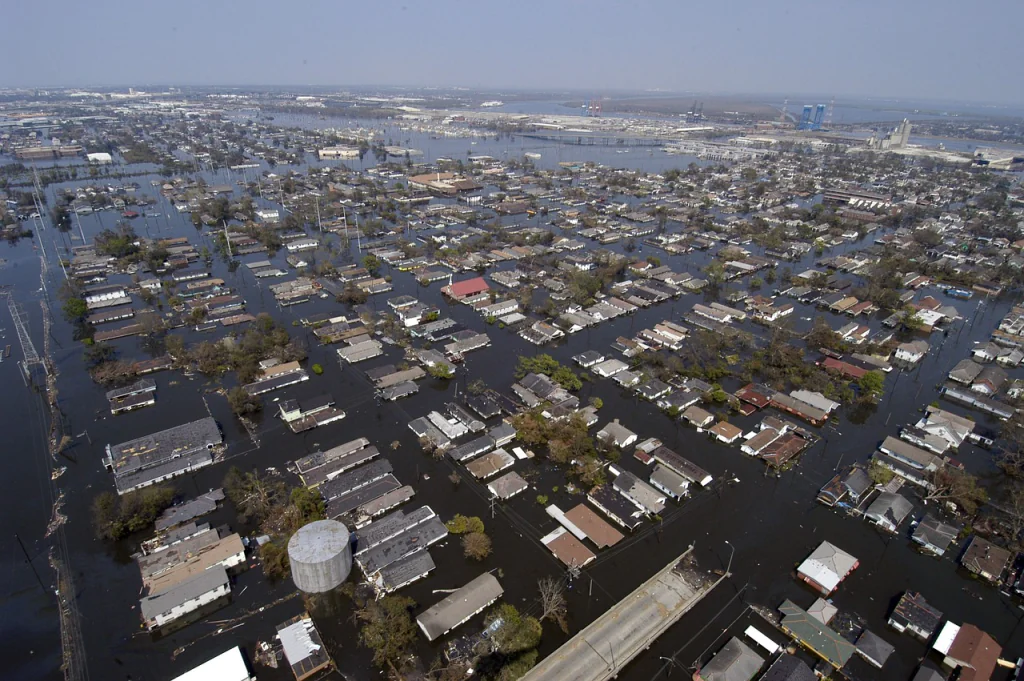
The Role of SLS Technology in Disaster Recovery and Prevention
Natural disasters such as floods and wildfires indeed cause widespread destruction, often damaging critical infrastructure and disrupting essential services. In response to these challenges, Selective Laser Sintering (SLS) has emerged as a touted tool for disaster recovery. However, the reliance on this technology raises several concerns that cannot be overlooked.
- Firstly, while SLS allows for the rapid manufacturing of replacement parts, it does not address the underlying vulnerabilities of existing infrastructure. The focus on quick fixes through 3D printing might lead stakeholders to overlook necessary investments in more robust solutions that could prevent disasters from causing such extensive damage in the first place. Relying heavily on an emerging technology like SLS may create a false sense of security.
- Secondly, although customized tools for emergency responders can be produced quickly with SLS technology, there remains a question about the quality and reliability of these tools under extreme conditions. While customization is beneficial, it does not guarantee that these hastily produced items will perform adequately when lives are at stake.
- Furthermore, the production of temporary housing and infrastructure components using SLS raises concerns about sustainability and long-term viability. The materials used in 3D printing may not always meet the durability standards required for permanent structures. This could result in a cycle where temporary solutions become permanent fixtures because of a lack of resources or planning, which ultimately extends suffering instead of alleviating it.
- In terms of medical equipment production post-disaster, while SLS has indeed shown promise in creating prosthetics and specialized devices quickly, there are significant regulatory hurdles that need addressing before such products can be deemed safe for use by healthcare providers under pressure.
- Lastly, while researchers are exploring advanced materials with enhanced fire and water resistance through SLS technology, transitioning from research to practical application remains a daunting challenge fraught with technical difficulties and financial constraints.
Summary
In conclusion, while Selective Laser Sintering offers innovative approaches to disaster recovery efforts, it is crucial not to overlook its limitations or allow it to overshadow more comprehensive strategies aimed at disaster prevention and resilient infrastructure development. A balanced approach combining new technologies with traditional methods will likely yield better outcomes for communities facing the threat of natural disasters.
By leveraging the power of SLS, we can enhance disaster resilience and recovery efforts worldwide. The ability to produce essential components quickly and efficiently is transforming how we respond to emergencies, making communities more prepared for the challenges ahead.
Sources:
“How 3D Printing Helps Disaster Response,” 3D Printing Industry
“The Role of Additive Manufacturing in Emergency Preparedness,” National Institute of Standards and Technology
“Selective Laser Sintering: A Game Changer in Crisis Response,” Journal of Advanced Manufacturing
Author: Tomasz Frąckiewicz
AM Sales Manager with over 12 years of experience in distribution in more than 50 countries on 4 continents. Specialized in analyzing and introducing laser technologies into distributorship portfolios or customer business models. Privately, an avid traveler, a new tech freak, and a modern art & music enjoyer.