Polypropylene in 3D printing: material properties & applications (Part 1)
Selective Laser Sintering (SLS) printing is a technology that allows you to create strong, detailed parts without needing molds or lots of finishing work. One of the materials used in SLS, polypropylene (PP), is especially notable for being lightweight, chemical-resistant, and durable. With advancements in 3D printing, PP is becoming more popular in fields like automotive and consumer goods. Whether you’re a 3D printing hobbyist or a professional exploring new materials, this guide will help you understand the potential of polypropylene in 3D printing (SLS technology).
This is the first part of the article, so prepare yourself a cup of good tea or coffee, and let’s dive into the world of Polypropylene (PP)—a material that has revolutionized industries with its versatility, durability, and wide-ranging applications.
Table of Contents
- What is Polypropylene in 3D Printing?
- Key Features at a Glance
- Where It Shines
- Polypropylene vs different materials in SLS printing
- When to Choose Polypropylene (PP) Over Standard PA12 in SLS?
- When Nylon May Be the Better Choice?
- Summary
What is Polypropylene in 3D printing?
Polypropylene (PP) is a versatile thermoplastic polymer widely recognized for its combination of strength, durability, and affordability. It is one of the most commonly used plastics in the world. What then should come to our mind, if someone asks: “What are the features of Polypropylene (PP)? ”. “What are applications or industries for Polypropylene?”. To imagine where this specific guy may fit, take a look at these short metrics of PP:
🌟 Key Features at a Glance:
- Lightweight: Easy to handle and transport.
- Chemical Resistance: Performs exceptionally well against harsh chemicals.
- Flexibility & Toughness: Combines rigidity with resilience.
- Low Moisture Absorption: Perfect for humid or wet environments*
- Highly Recyclable: A sustainable choice for eco-conscious industries.
*reference to injection PP
🚗 Where It Shines:
- Automotive: Lightweight components, such as interior trim, ducts, and fluid reservoirs*.
- Medical: Biocompatible parts, such as surgical guides, prosthetics, and drug delivery devices.
- Consumer Goods: Durable and flexible parts, such as hinges, snap-fit components, and packaging prototypes.
- Industrial: Chemical-resistant components, such as tanks, valves, and fittings.
*reference to injection PP
With these standout qualities, it’s no wonder that polypropylene is rapidly carving out a significant place in the world of 3D printing, also in the realm of SLS applications.
Polypropylene vs different materials in SLS printing
One of the most common questions I ask customers at the beginning of their evaluation of an SLS system is about the material they plan to use for their application. My goal is to simplify the decision-making process, as experience shows that we often lean toward materials that may not be the most suitable. This leads to a question:
When should polypropylene (PP) be chosen over the standard PA12?
To help you evaluate whether polypropylene is a suitable material for your specific application, I have created the following list of key application features to consider. This overview highlights the critical factors that should guide your decision-making process when choosing polypropylene.
When to Choose Polypropylene (PP) Over Standard PA12 in SLS?
🌟 Flexibility & Impact Resistance
- Perfect for parts requiring repeated bending, such as living hinges or snap-fit designs, where nylon might be too rigid.
🧪 Superior Chemical Resistance
- Outperforms nylon in withstanding harsh substances like acids, alkalis, and organic solvents, ideal for industrial and medical applications.
🌍 Lightweight & Eco-Friendly
- PP is lighter and more recyclable, offering advantages for sustainability-focused industries and cost-effective production.
When Nylon May Be the Better Choice?
🔥 Higher Heat Resistance & Strength
- Excels under high-load conditions and in environments with elevated temperatures.
🎨 Aesthetic Superiority
- Delivers a smoother surface finish and is easier to dye, making it ideal for visually critical applications.
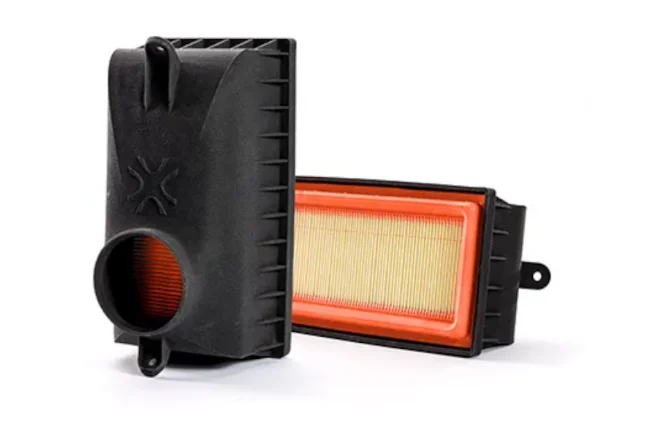
Compared to commonly used SLS materials like nylon (PA12), polypropylene (PP) offers advantages in flexibility, impact resistance, and chemical resistance. PP is ideal for parts requiring repeated bending, like living hinges or snap-fit designs, where nylon might be too rigid. It also excels in resisting acids, alkalis, and organic solvents, making it well-suited for industrial and medical environments. Additionally, PP absorbs less moisture when treated with relevant post-processing.
While nylon outperforms PP in heat resistance, strength under load, and aesthetics, PP’s lighter weight and recyclability make it a more sustainable, cost-effective option for certain industries.
The choice between the two materials depends on the project’s specific needs—PP for flexibility, chemical resistance, and light weight, and nylon for stiffness, heat resistance, and premium finishes.
Summary
In this first part of the article, I introduced polypropylene (PP), a standout material in SLS known for its lightweight nature, chemical resistance, and durability. With advancements in 3D printing, PP is gaining traction in industries like automotive and consumer goods. We also explored what polypropylene is, what are its key features and what are industries in which it’ applied.
As you might have noticed,I marked that some PP present specific properties in a specific technology. In the next part of this article, we’ll dive deeper into the different types of technologies that use PP. We’ll also explore the challenges in using PP in the additive manufacturing world.
So, grab another cup of tea or coffee, and get ready to explore the world of polypropylene in even greater detail: Polypropylene in 3D printing: material properties & applications (Part 2)
Author: Monika Jurek
SLS 3D Customer-Centric Associate with two years of experience working with companies worldwide. She specializes in helping businesses identify optimal solutions for implementing 3D printing using SLS technology.