Polypropylene in 3D printing: material properties & applications (Part 2)
If you need an introduction, we recommend reading Part One about propylene first: Polypropylene in 3D printing: material properties & applications (Part 1)
In this second part of the article, we’ll take a closer look at the world of Polypropylene (PP) and its behavior among different technologies. If you’ve been following along, the first part provided an introduction to PP, its properties, and its applications in manufacturing processes. By now, you should have an understanding of why PP is such a versatile and widely used material. In this second part, we’ll shift our focus to the specific types of PP and how they cater to different industrial needs. Whether you’re exploring PP for its chemical resistance, flexibility, or biocompatibility, understanding its various formulations will help you make informed decisions for your projects. Let’s get started!
Table of Contents
- Polypropylene: SLS vs Injection Moulding
- Comparison of Polypropylene (PP) in SLS vs. Other 3D Printing Technologies
- Sinterit’s Polypropylene in 3D Printing
- Summary
- What are the main benefits of using polypropylene in SLS?
- What are typical applications for Polypropylene (PP)?
- How does the surface finish of polypropylene parts compare to injection-molded parts?
Polypropylene: SLS vs Injection Moulding
Why I decided the topic in the title of this paragraph? This is because I often have a feedling that some of the clients I talk to tend to consider that the polypropylene they meet daily, in eg. plastic bottles or car headlights, which come from injection moulding, is the same as in SLS. This it not true.
Polypropylene in SLS printing is nowhere near as flexible as injection-molded PP, and this often confuses many who seek for this material to in different technology to lower production costs. Injection-molded PP typically has an elongation at break of around 300%, whereas SLS-printed PP offers only about 30%. This means, for example that if someone wants to 3D print a small hinge, like the one found on a shampoo bottle, it won’t work because the printed part will break, even though the injection-molded version functions perfectly.
Definitely polypropylene used in SLS differs from PP used in injection molding due to the distinct processing methods and resulting material properties.
- In SLS, polypropylene is delivered as a fine powder that is sintered layer by layer using a laser, creating parts without the need for molds. This process can result in slightly different mechanical properties, such as lower density and slightly reduced tensile strength compared to injection-molded polypropylene.
- Additionally, SLS polypropylene often exhibits higher porosity. So probably, having seen before the injection moulded part form PP, you will not be satisfied with the surface finish received with PP in SLS. If you’re considering receiving parts that aspire to end-use products and you’d like to provide nice surface finish then beware that parts made from polypropylene in SLS often require post-processing to improve surface finish and reduce porosity, as the laser sintering process can leave parts with a rougher texture compared to injection-molded materials.
These differences make SLS polypropylene particularly suitable for applications requiring design flexibility and rapid prototyping, while injection-molded polypropylene is typically optimized for high-volume production with uniform properties.
Comparison of Polypropylene (PP) in SLS vs. Other 3D Printing Technologies
Do you like table charts? Yeah, me too. Let’s not pretend we have enough time to read everything sentence by sentence in the wall of text 🙂 Therefore, grab this summary of prons and cons presented below – it refers to polypropylene material in various technologies you’re surely familiar with.
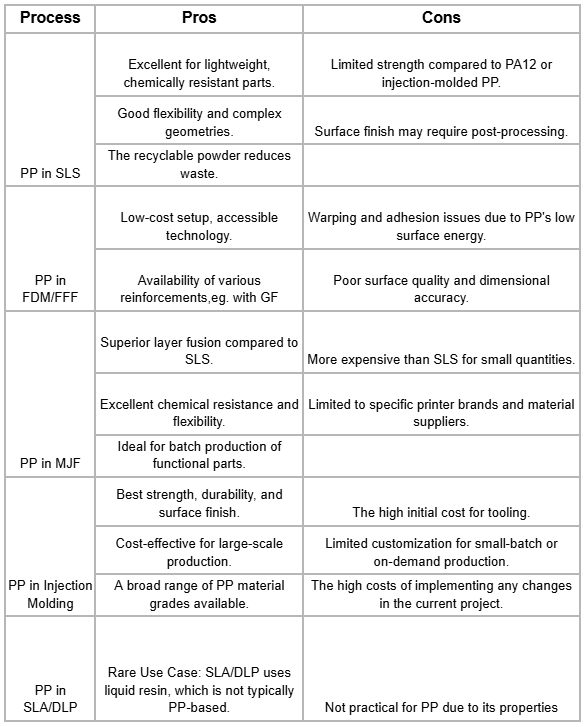
- For PP in SLS, it’s great for lightweight, tough parts with complex shapes, but it might not be as strong as other materials, and you’ll likely need some post-processing for a smoother finish.
- With PP in FDM/FFF, it’s super affordable and easy to use, but expect some issues with warping and surface quality. It’s good for simpler projects but not ideal for precision work.
- PP in MJF offers better layer bonding and flexibility, perfect for functional parts, but it can get pricey for smaller runs and is limited to specific printers.
- PP in Injection Molding gives you the best strength and finish, great for mass production, but it’s expensive upfront and not great for small batches.
- Finally, PP in SLA/DLP isn’t really a fit for this material since it’s all about resin, so not much use there.
Sinterit’s Polypropylene in 3D Printing
Here’s a quick sneak peek into the polypropylene (PP) we work with every day—perfect for those eager to explore the deeper properties of this remarkable material. Whether you’re the one running tests on PP-printed parts or the go-to person for material evaluation, the insights below are tailor-made for you:
Polypropylene (PP) is a co-polymer material compatible with the Sinterit Lisa PRO and Lisa X printers. It features a tensile strength of 19.3 MPa and a flexural strength of 25.6 MPa. Its melting point is 135°C, with a heat deflection temperature of 50°C at 1.8 MPa and 85°C at 0.45 MPa. PP has a 50% refresh ratio and does not require nitrogen for printing.
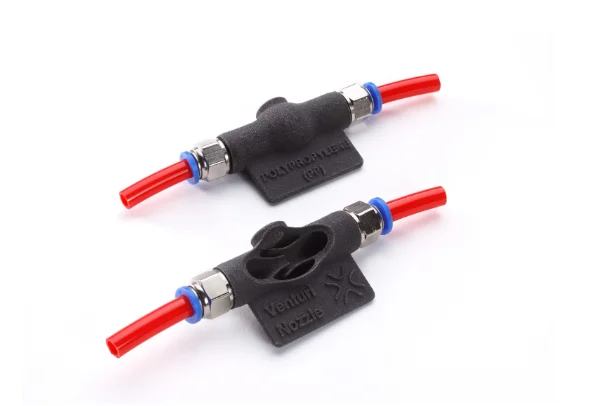
Coming back to reality – below’s the naked truth on Sinterit’s polypropylene – revealed by our R&D Manager, Piotr:
“The first topic that comes to mind regarding PP (Polypropylene) is its relatively good chemical resistance (to acids, bases) and decent mechanical properties (eg. flexibility). However, it is certainly not suitable for parts exposed to UV, as it has a high degradation rate under UV exposure. Any load-bearing components are also out of the question due to its low stiffness, although the material’s low density encourages this for applications where minimizing weight is a goal. Sinteirt’s PP* has different properties than injection moulding PP, which excludes it from most conventional PP applications. However, after being sealed with vapor smoothing, it could be useful eg. for making molds for silicone casting.“
I hope it sheds enough light of what you may expect when deciding on choosing PP. For more details on our PP, visit Sinterit website with materials porfolio.
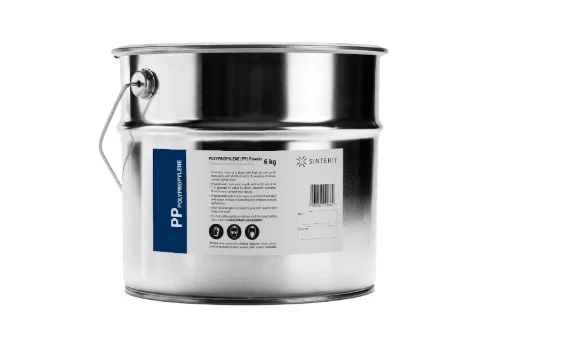
Summary
Hopefully, I did not get you bored yet and the only world that you comes to your mind when you hear Polypropylene is ‘chemical resistance’. However, if I failed and you scrolled down the article to get here – here’s the short summary of it, in my favourite – Q&A form: Let’s go!
What are the main benefits of using polypropylene in SLS?
Polypropylene in SLS offers excellent chemical resistance, low weight, and good flexibility, making it ideal for creating durable functional parts and prototypes with complex geometries.
What are typical applications for Polypropylene in 3D printing?
Polypropylene (PP) – in general – is widely used in packaging, automotive parts, and consumer goods due to its lightweight, durable, and chemical-resistant properties. It’s also common in medical devices, textiles, and industrial applications like chemical tanks and pipes. In 3D printing, PP is used for creating lightweight, functional parts, making it versatile across various industries
What’s important, we need to distinguish whether SLS or injection molding PP part made will meet requirements of our application.
- Choose PP in SLS:
- For prototyping, custom parts, or low-volume production.
- When design complexity or lightweight structures are required.
- For applications where chemical resistance or biocompatibility is critical.
- Choose PP in Injection Molding:
- For high-volume production of standardized parts.
- When high mechanical strength, durability, and surface finish are required.
- For cost-effective manufacturing of large quantities.
How does the surface finish of polypropylene parts compare to injection-molded parts?
Parts printed with polypropylene in SLS typically have a rougher surface finish due to the layer-by-layer sintering process, and may require additional post-processing like smoothing or polishing to match the finish of injection-molded parts.
It’s clear that polypropylene (PP) isn’t a one-size-fits-all material—terminology can be misleading, and the specifics are crucial. That’s why a deeper dive into its properties is essential to achieve optimal results for your application. By understanding the differences, you can avoid the frustration of testing the wrong solution and save precious time.
Author: Monika Jurek
SLS 3D Customer-Centric Associate with two years of experience working with companies worldwide. She specializes in helping businesses identify optimal solutions for implementing 3D printing using SLS technology.