New to SLS? Expand 3D printing applications in manufacturing
Even after acquiring industrial 3D systems, most companies fail to move past prototyping. McKinsey reports that only 21% of firms scale additive manufacturing into production or service. Gartner notes a productivity stagnation, caused not by the machines but by the inability to identify new applications. Companies don’t lack tools, they lack the vision to use them.
This gap is often rooted in three causes:
- application blindness, teams don’t see problems as printable,
- functional silos, no link between 3D SLS, teams and operations,
- misunderstood value, benefits stay invisible if not tied to cost or speed.
How SLS unlocks new real 3D printing applications in manufacturing
A mid-sized industrial manufacturer bought an SLS system only for prototyping, aiming to speed up design iterations and improve communication with engineering. Using the printer beyond prototyping was never considered.
Initially, they printed only rapid prototypes. After six months, the 3D SLS printer lead worked closely with maintenance and production teams, discovering long lead times for tooling, costly spare part inventories and frequent workarounds.
New applications emerged:
- tooling components printed on demand, reducing lead time from weeks to days,
- spare parts printed locally, eliminating stockouts and urgent shipments,
- custom jigs and fixtures improving assembly,
- functional parts adding value beyond prototypes and enabling new SKUs.
The printer stopped being just a prototyping tool, becoming a strategic asset that reduced costs, increased agility and reshaped operations.
This mindset shift unlocked value beyond expectations, transforming the company’s innovation capacity.
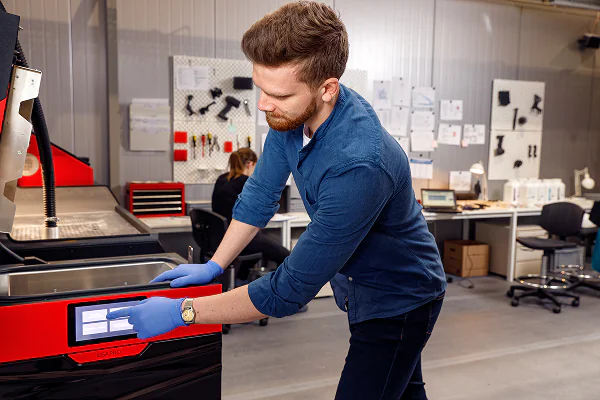
How to identify profitable 3D printing applications in manufacturing using SLS
- Problem-first mapping, start from operational frictions, then match to 3D capabilities: weight, complexity, delay, MOQ.
- Inventory analysis, look at high-SKU, low-demand parts, this is where 3D saves both cost and risk.
- Interdepartmental scouting, assign 3D engineers to work short-term inside production, service or logistics teams.
Tooling and spare parts: the most cost-effective 3D printing applications in manufacturing
According to BCG and Roland Berger, companies spend 5 to 15% of their OPEX on areas ideal for 3D printing applications in manufacturing, like tooling, maintenance and spare parts. With in-house SLS, the entire cycle is cut to degrees never seen before:
- tooling lead time drops from 3–6 weeks to 1–2 days,
- costs reduced by 50 to 90% per tool,
- spare parts printed on demand, no warehousing, no obsolescence.
An aerospace supplier saved over €200,000 annually by switching 37 metal jigs to polymer SLS with comparable performance in daily use.
Real-world use cases: SLS in daily 3D printing applications in manufacturing
A European machinery company started with just jigs. After 6 months of cross-functional workshops, they added:
- on-demand production of guides, brackets, clamps,
- custom tooling adapted per operator,
- in-field spare parts delivered as STL to technicians abroad,
- enclosures with integrated functions,
- modular production aids reused across product lines.
The success came from one insight: 3D SLS is not a tool, it is a method. Every delay, order or workaround hides a printable solution, often a new use‑case hidden in plain sight.
From prototypes to products: evolving 3D printing applications in manufacturing with SLS
Most companies stop at the obvious. But SLS printing is not just faster prototyping, it’s also a tool to unlock entirely new product categories. By looking beyond design iterations, companies begin identifying components they’ve never considered printable until now.
Real-world use‑cases include:
- batch production of modular accessories and kits,
- reinforced components for internal assemblies,
- custom-fit parts adapted to regional or customer-specific needs,
- high-performance housings with integrated geometries.
These applications don’t replace existing products, they expand the product ecosystem. They fill gaps legacy production ignores due to tooling cost, MOQ constraints or low-volume demand.
Most missed use‑cases live between departments, in service, in packaging and in technical support. SLS is the bridge between need and speed.
Expand your product line through 3D printing applications in manufacturing
SLS allows companies to develop adjacent products with zero tooling investment. You can create variants, add-ons or accessory SKUs using 3D printing applications in manufacturing without touching your main production line. This leads to:
- faster time to market for special editions,
- custom parts per client or industry without affecting base SKUs,
- small series pilot runs with real performance data,
- value-added parts for service contracts and upgrades.
In one case, a company introduced 12 new part numbers using only their SLS machine and existing CAD work. These became upsell elements and field-replaceable units, opening new revenue streams without disrupting production.
FAQ: 3D printing applications in manufacturing
Because they don’t link 3D printing applications in manufacturing to real operational pain. They see parts, not problems. SLS sits idle while teams keep solving issues the old way.
In tooling and in-house spare parts, where savings in lead time, inventory and cost are immediate and proven. No MOQ, no warehousing, no delay.
By embedding 3D engineers into service, production and supply chain teams. Applications come from friction, not from the machine.
Low-demand, high-SKU, or high-customization parts, especially tooling, fixtures, spare components, and short-run functional parts.
It reduces tooling and part lead times from weeks to days, and enables on-demand production, helping teams respond faster to changes or disruptions.
Not always—but it complements it by filling gaps where injection molding, CNC, or casting are too costly, slow, or inflexible.
It allows for easy creation of add-ons, accessories, and limited series SKUs with no tooling investment—ideal for testing, customization, or upselling.
Lack of cross-functional collaboration, unclear ROI, and failure to align AM capabilities with real business priorities.
Stop thinking of 3D printers as prototyping tools. Start treating them as strategic enablers of 3D printing applications in manufacturing, capable of transforming how you design, produce, and deliver.