FDM vs SLS – is it comparable?
Every time a 3D printer manufacturer compares different technologies on its blog it sounds tricky. Especially when it offers only one of the compared types. This blog post isn’t to praise SLS. We will not look for the good, the bad, and the ugly amongst the most popular additive manufacturing technologies. They are all important, and the last thing we would recommend is to buy an SLS 3D printer if your application is purely FDM type.
FDM is a universal and available 3D printing technology
Is there a universal 3D printing technology for all applications? FDM fits into this framework. It is affordable and very accessible with the largest list of materials available on the market. You can choose one of the top brands or acquire a DIY kit born in China. It all depends on your budget and the projects you are working on.
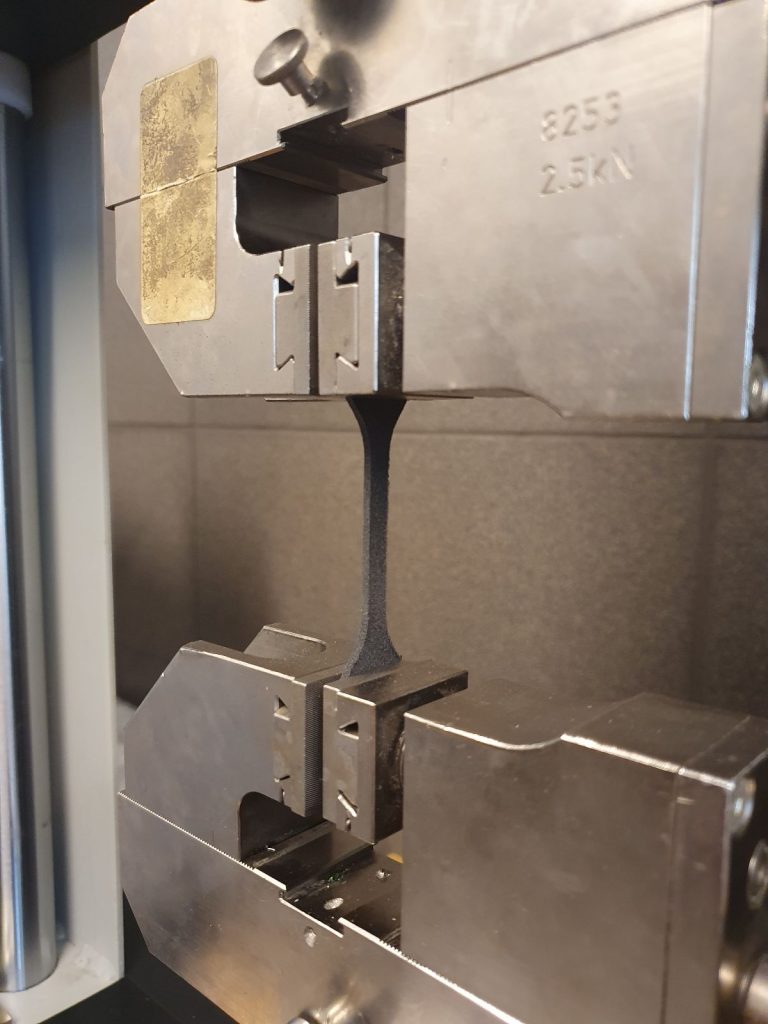
On the one hand, there is a powerful workhorse, as Markforged describes its OnyxPro, a game-changing 3D printer for Continuous Fiberglass reinforced parts. Those printouts are extremely solid. But on the other hand, you can also buy a no-name printer good enough to print a 3DBenchy, but not much more.
With such a big spectrum, where anyone could choose the best-fitting 3D printer, we may announce FDM as the number one additive manufacturing technology.
What is FDM?
Talking about FDM, we are in fact describing FFF – fused filament fabrication. FDM, which stands for fused deposition modelling, is a Stratasys trademark. Nevertheless, even industry leaders call it that way, the same as people in Poland used to name any sneakers “Adidas”, regardless of the brand.
In this technology (we will call it FDM, as it is more popular), a continuous filament of thermoplastic material is fed from a large (sometimes not so large) spool through a moving, heated printer extruder head. Then it is deposited on the growing work. Some FDM 3D printers have more than one extruder, like in the mentioned Markforged OnyxPro – the first one is dedicated to printing onyx (plastic extruder), and the second provides the reinforcement composite (fibre extruder). Other makers use two extruders to apply water-soluble support material, an option you can find in some Ultimaker 3D printers.
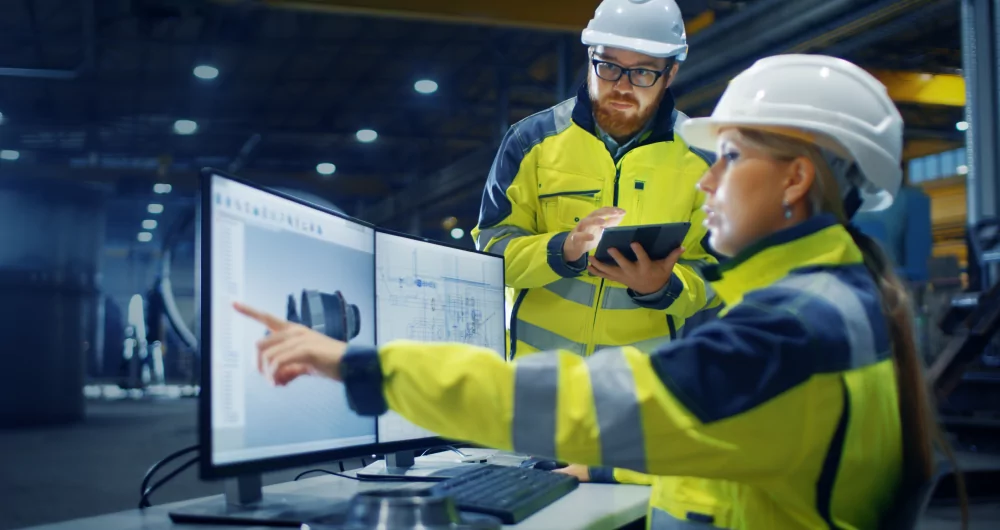
How does FDM deal with gravity?
All 3D printing technologies are dealing with gravity. Building a print, layer by layer, is like building a house. If the walls are straight, everything is going fine and smooth. But when some overhanging parts occur, it becomes precarious. As construction companies use steel props, in FDM printers this problem is solved with special supports. You don’t even need to think about designing them, they will be generated automatically by 3D printing software and printed alongside. After your printout is ready you can easily detach it with a knife, needle-nose pliers, or flush cutters. In some cases, when supports are water-soluble, just put your printout into a bucket filled with water.
Some FDM producers offer rotating print beds that can change an angle during the printing process which limits the number of needed supports. That is quite a cool solution.
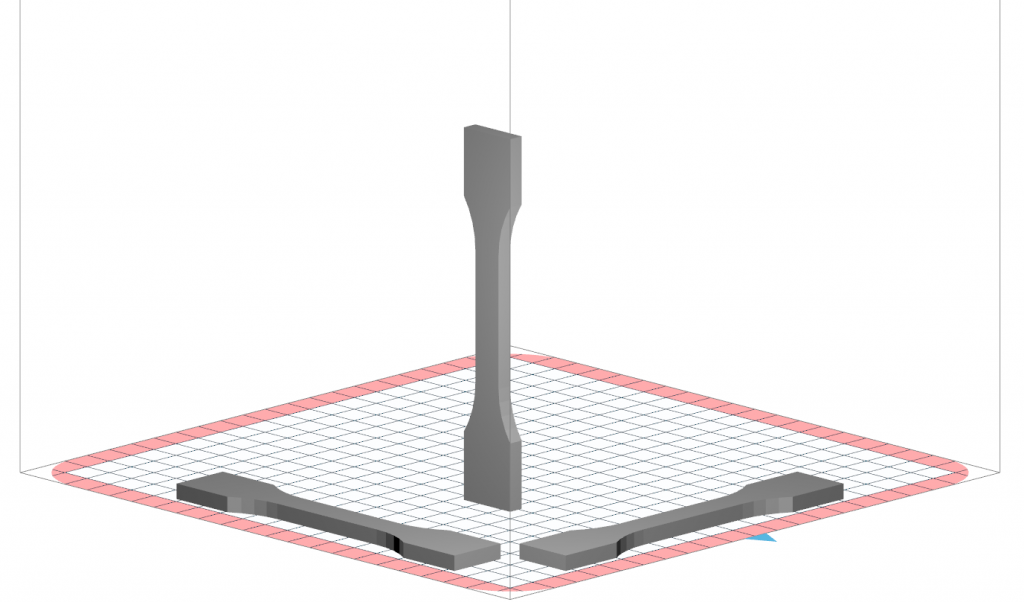
FDM for bigger parts
If you are looking for big printouts, FDM may be the best choice. Top FDM producers offer 3D printers with a printing bed of 330 x 240 x 300 for less than 6000 USD. But you can also find less-known brands that sell 600 x 600 x 660 mm (0,25 m3) printing bed FDM printers for less than 5000 USD. If you compare it with 550 x 550 x 750 mm (0,23 m3) provided by one of the biggest polymer SLS 3D printers on the market, that with all needed peripheral equipment, installation and training will cost you even 1M USD, you can feel the difference.
Why do FDM filaments seem stronger than SLS powders?
As mentioned before, some FDM printers offer extremely durable, carbon-fibre-reinforced parts. But for a typical FDM printer, strength is a weakness. It may be hard to understand while reading the specification of some FDM filaments. When you compare the tensile strength of some PA 12 nylon filaments available for FDM 3D printers with PA 12 nylon powder used on SLS 3D printers, the first one may seem stronger. But it isn’t. Why?
Mainly because FDM prints are anisotropic. Isotropy is a term used in materials science where “isotropic” means having identical values of a property in all directions. For example, parts made with injection moulding or thermoforming have isotropic properties, so they are equally strong in X, Y, and Z directions. For the purposes of this blog, we can take it as a rule of thumb, because some polymers, like liquid crystal polymers, are highly anisotropic, even with injection moulding.
Anisotropy is not only the case of materials used for FDM 3D printing, but the process itself. The way parts are built with FDM is utterly anisotropic. It’s relatively easy to tear FDM printed models apart, especially between layers. How easy is it?
The strength of 3D printed parts can be measured and standardised with tensile strength, which is the ability to resist breakage when under tension. This most widely used 3D printing industry indicator, expressed in megapascals (MPa) or pounds per square inch in the US (psi), is important for engineers and designers when looking for a material or technology for mechanical applications. During the tensile strength test, a standardised tensile test specimen is being pulled and a tensometer records the degree of tension at which the material breaks.
Checking the specification of FDM filaments you may be shocked how good they look on paper. Most nylon filaments have tensile strength between 50 and 80 MPa. So comparing it to Sinterit’s PA12 with only 32 MPa you may consider FDM a winner in this category. But there are caveats.
Four researchers from the Mechanical Engineering Department of Petra Christian University in Indonesia tested the effect of orientation difference in fused deposition. They were interested in ABS material – the one Lego bricks are made of. Tensile test specimen was printed with Bits from Bytes ABS polymer filament in three different orientations: flat, on the edge and upright. Then they performed tensile strength tests for all of the specimens. As they figured out that the orientation influences tensile strength.
Flat specimen broke at 6,8 MPa, the one printed on edge was the strongest, and broke at 7,66 MPa, but the weakest one, printed upright, showed that it is way more brittle. It broke at 3,31 MPa. The reason why it happens in FDM technology is that anisotropy is most noticeable where the layer connects. So remember, that tensile strength mentioned on the box of your filament or in the attached specification describes the tensile strength of the material itself, not of the 3D printed model.
The good news is that even with FDM 3D printing you can make some adjustments that will enforce your parts. By changing the infill percentage, you can make your part stronger. The same will happen when you increase the shell thickness (outer surfaces of the part). You can also choose another, stronger material, or try to print a part rotated. To determine how the part should be positioned, you need to know the direction in which the force will most often act on the part. But this can be a makeshift solution as there are situations where you don’t want to reinforce your model, because you need it to be strong the way it was designed. How does it look in the SLS technology?
SLS for stronger parts
Parts printed with SLS are, in contrast to FDM, almost isotropic. This technology uses a laser as an energy source to sinter (fuse) powdered plastic material. The print builds layer by layer. The process is quite simple – a roller, known as a recoater, spreads a thin layer of powder on the work surface. After that laser beam selectively fuse some of the powder, according to the given project, while the rest of the powder remains unsintered and acts as a natural support for the build.
The clue to understand SLS 3D printing technology is the temperature. SLS 3D printers are working in a closed environment. The temperature in the chamber is closed to the melting point, and the laser only adds sufficient heat to melt the powder. Thanks to that after laser finishes sintering the one layer, which ends up in melting powder grains and connecting them together by necks, the cooling process is not as significant as in FDM 3D printing, which makes necking particles in all axes almost identically strong.
The group of researchers from Marwadi Education Foundations Group of Institutions (India), Vaal University of Technology, and North West University, Potchefstroom (both from South Africa) did almost identical experiment with the SLS 3D printer as described earlier with FDM one in. They tested the effect of orientation on tensile strength of parts laser sintered with PA 12 powder. The specimen was printed in three different orientations using EOS Formiga P100. Results showed that as there is a difference in the tensile strength between differently orientated parts, results were quite narrow. The average ultimate stress that specimens experience varied between 43,47 to 46,15 MPa. “Minimising anisotropy is desirable so as to allow manufacturers to build parts in any orientation without affecting the mechanical properties of the produced parts” – states the report.
If the strength of the part is your priority, SLS 3D technology may be a better choice than FDM. You will not achieve as strong parts as those made with injection moulding, thermoforming or CNC but for additive manufacturing technologies, SLS could be your number one choice.
Hollow and lightweight but strong parts
Using unsintered powder in the SLS technology as a natural support results in the ability to produce parts that don’t need additional reinforcement during the 3D printing process, but can go even further. Appling lattice structures, if done correctly, can make parts lighter and stronger at the same time. But there are more benefits, like reducing the use of material to print the part or making the part better in energy absorption.
Lattice structures are used across many industries, starting with automotive, medical, to sport or other customer products. With software such as Autodesk Fusion 360 and Netfabb, Gen3D Sulis, Materialise 3-Matic or Altair Optistruct & Inspire it is possible to add lattice structures to your model without the need of designing them manually.
As you can use lattice structures both in SLS and FDM technologies, it is easier in the first one, as you will not confuse it with the supporting structures while post processing.
Pros and cons of FDM and SLS technologies
Pros of FDM
- Wide range of printing materials.
- Affordable – low or moderate costs of equipment
- Low or moderate post-processing costs (support removal and surface finishing).
- Best for medium-sized and big elements.
- Almost no porosity of the components.
- High structural stability, chemical, water and temperature resistance properties of materials.
- Bigger build volume compared to other desktop technologies.
Cons of FDM
- Printed model are much weaker in vertical build direction because of the anisotropy in material properties
- Support are needed (but not always)
- The temperature in print chamber can’t be precisely controlled
- Less accurate than SLA or SLS technology, with “stair-stepping” in vertical build planes.
Pros of SLS
- Durable and strong parts.
- No support structures needed.
- Easy to apply lattice structures or print hollow parts.
- Smooth surfaces – it is hard to notice the layer.
- Powder is reusable after printing.
Cons of SLS
- Printed objects are small to medium sized
- Works best with full post-processing tools such as Powder Handling Station
- Cleaning of the machine must be done precisely when changing material to avoid contamination.
- More expensive than the average FDM printer.
Lower the costs of your SLS 3D printing
