Sinterit SLS 3D printing in SAE Aero Design
The SLS 3D printing technology from Sinterit was one of the components of the success that the SAE Aero Design Student Association from Warsaw University of Technology achieved in prestigious competitions in the United States.
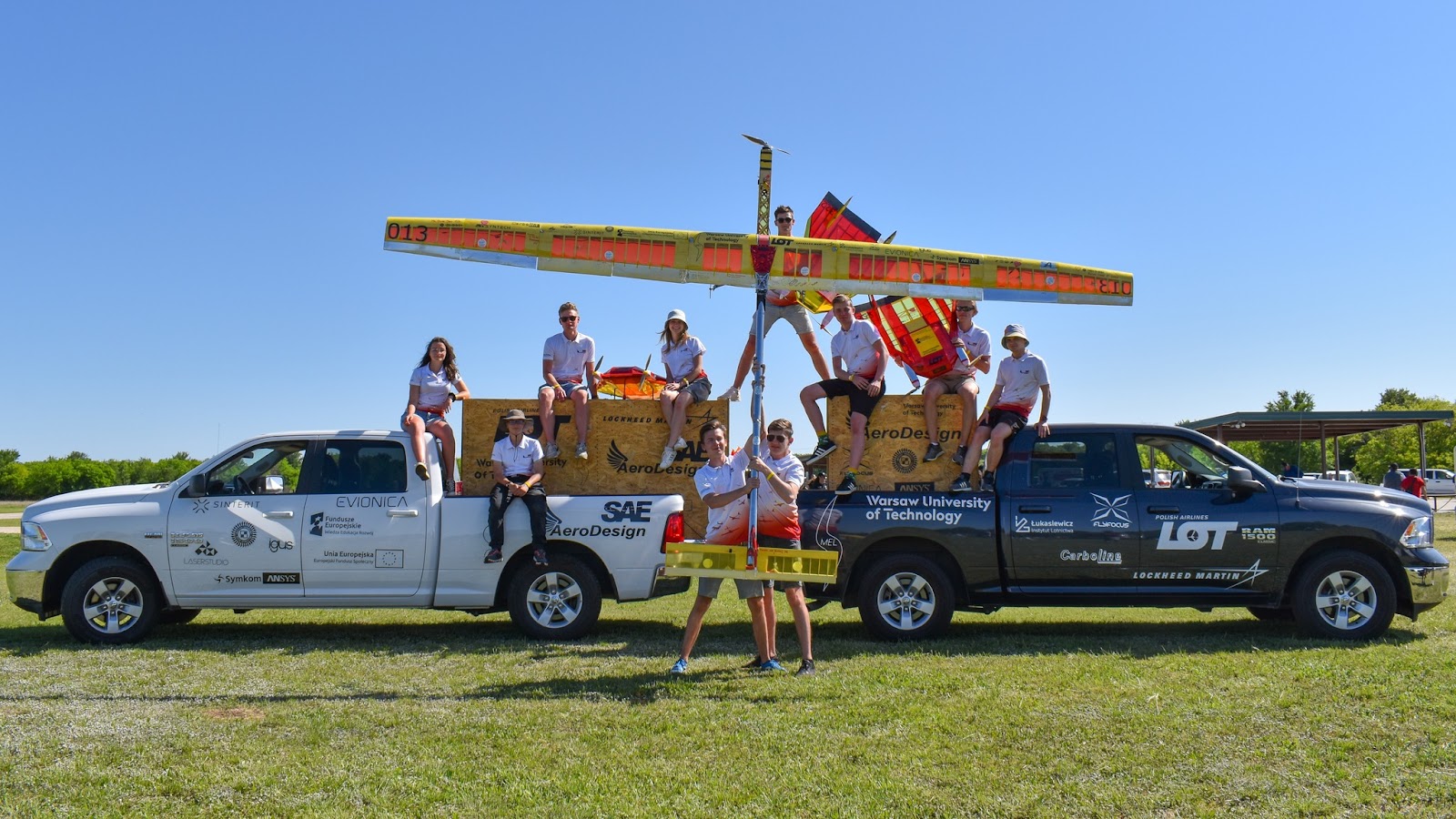
SAE Aero Design is a series of competitive aerospace and mechanical engineering events held in the US since 1986. The intent of the competition is to provide engineering students with real-life engineering challenges. The Polish team from the Warsaw University of Technology has been participating in these competitions for 31 years as one of the favorites. This year team won three general prizes during two editions East and West, first and third in different categories, and overall stood on the podium thirteen times.
The purpose of the SAE Aero Design competition is to design and build an unmanned aerial vehicle capable of lifting the heaviest possible payload. There are three categories of aircraft: Micro, Regular, and Advanced. Parts printed on Sinterit’s SLS 3D printer were used in the regular one. What were the assumptions?
The aircraft, built under the rules of the regular class, needed to have a wingspan of 120 to 216 inches, a take-off run of up to 100 feet, and electric motor power limited to 750W. Additionally, the maximum length of each of the elements used in the aircraft couldn’t exceed 48 inches.

The team of 20 students worked for six months to develop six models: four in a micro category and two in a regular one. As the SAE Aero Design has two editions, East and West, the Polish team decided to compete in both of them.
Aircraft design and preparation
The quality and accuracy of the parts along with their light weight are crucial in the aerospace industry. The use ofSLS 3D printer, Lisa X from Sinterit, was a natural choice. The key feature of SLS technology is virtually unlimited freedom in designing geometry, which accompanied by isotropic mechanical properties of the printout resulted in making strong, lightweight parts. As the rules of the SAE Aero Design competition prohibit the use of fiber composites, Lisa X printouts stepped in with success.
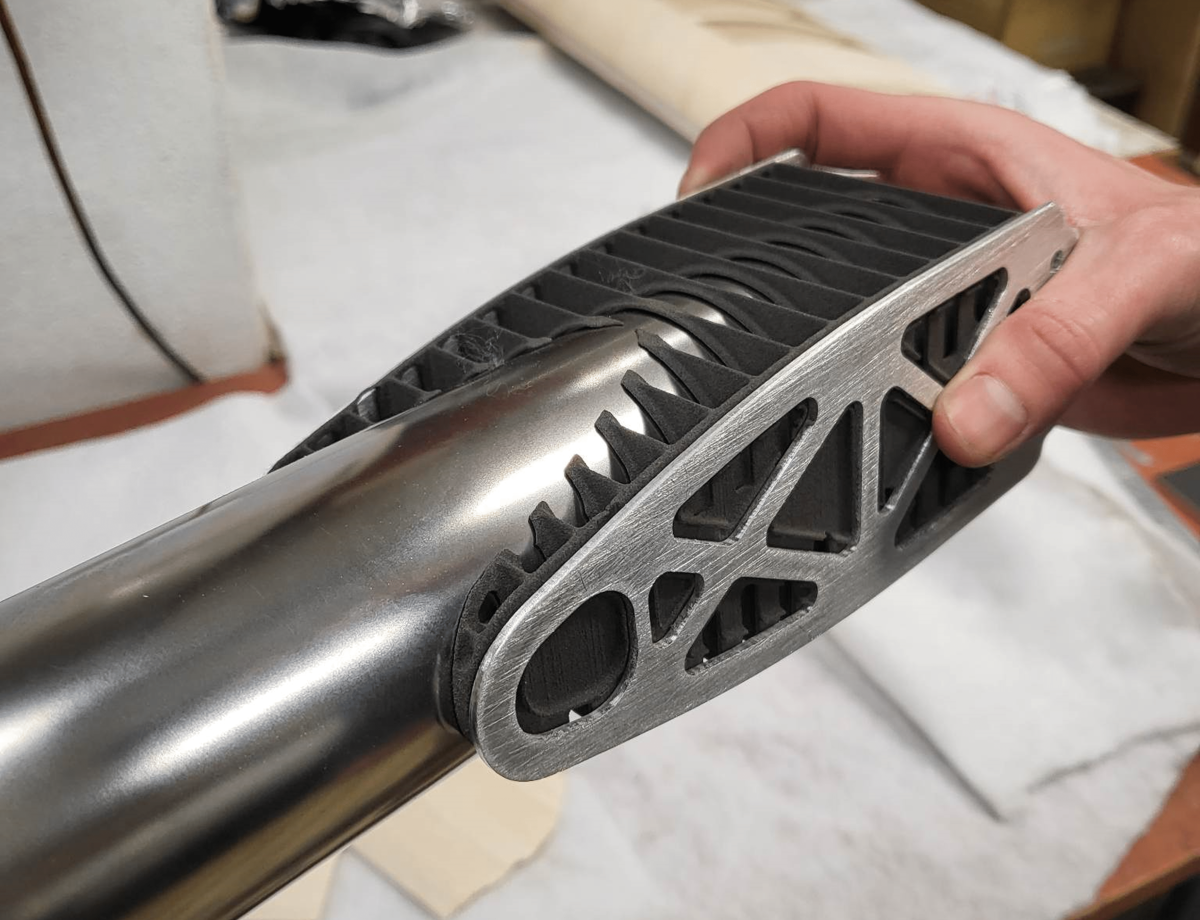
– SLS printing allows us to design parts with complex geometry and precision that is not achievable in fdm/fff printers. This is crucial when reducing weight. The practically isotropic mechanical properties of the finished print (as opposed to fdm/fff printing) are also very important. This allows for a much freer design of elements. – says Michał Włodarczyk, Regular class plane coordinator.
Students from the Warsaw University of Technology designed one of the mounting elements of the R23 (the name of the plane) tail boom with SLS technology in mind. The tail boom mount transmits very high forces and moments, being at the same time a very important element of the structure. Thanks to the virtually unlimited possibilities of geometry design, it was possible to make a very light and durable element.
The competition
The Aero Design East took place at the Paradise Field in Lakeland, Florida. During the three days of competition, the plane called “Czapla” (heron) performed eight flights with a maximum load of 7,47 kg and a curb weight of 8,7 kg. Overall, the team finished fourth.
A month later, at the Thunderbird Field in Fort Worth, Texas “Czajka” performed eight flights, this time being third in the regular class defeating sixty teams from around the world. Meanwhile, the Aero Design West competition brought an ultimate victory in the micro class in which The Warsaw University of Technology team won the first prize.
As it was the 31st participation in this competition, but the first one using SLS 3D printing technology it is this opens up a good perspective for the future and even better use of advanced 3D printing capabilities in creating competition-winning aircraft.