SLS powder refresh rate – how to refresh powder for best quality prints
Refresh rate, or refresh ratio are the terms you will come across in Selective Laser Sintering 3D printing a lot. What is the meaning and importance of SLS powder refresh rate? How to reuse the material to reduce costs and be more sustainable? In this article we provide answers and also debunk some SLS powder related myths.
A powder refresh rate in a 3D printing process
Before we explain what a powder refresh rate is, you need to understand the difference between most common 3D printing materials and technologies. To make it easier, let’s focus on three most popular – FDM, SLA and SLS.

Image: printout from FDM with supports
In FDM technology you have a broad range of filaments, each of them is spooled into a reel. While 3D printing, you use as much material as needed and after the job is done, just cut the filament and you are ready to go with what’s left. Be aware, that in the FDM case, your 3d-printed supports become a waste.

Image: model printed with SLA 3D printer
Another popular additive manufacturing technology – SLA (stereolithography) gives you the possibility to print from a resin. A liquid consistency gives you a lot of benefits related to the smoothness of 3D printed parts and the sharpness of the edges. You can also reuse the resin left after the 3d printing process. But there are at least two concerns. First, SLA models still need 3D printed supports, so the amount of resin to recover is less. More concerning one is related to the need to work with potentially harmful chemicals. You also need to filter the resin, and be aware that exposing it to light may cause future printing problems.

Image: printed powder bed shortly before taking out of the SLS 3D printer
In the SLS 3D printing technology to print your models you need powder. That provides several benefits. One of them is almost isotropic properties, compared to anisotropic characteristics of filament based FDM 3D prints.
Another advantage is the ability to reuse the powder that was unsintered during the process. Because the powder itself works as natural support for your models, which is considered another advantage, it can be recovered after the 3D printing. In the FDM or SLA case, your 3d-printed supports become a waste.
When SLS technology was introduced, for industries such as automotive, aviation or even medicine it was like finding the Holy Grail. The ability to produce three-dimensional objects, strong and detailed at the same time initiated by SLA (stereolithography) gained two powerful advantages: the freedom of design, and safe material reuse capability. In this article we explain the ability to reuse your powder over and over again.
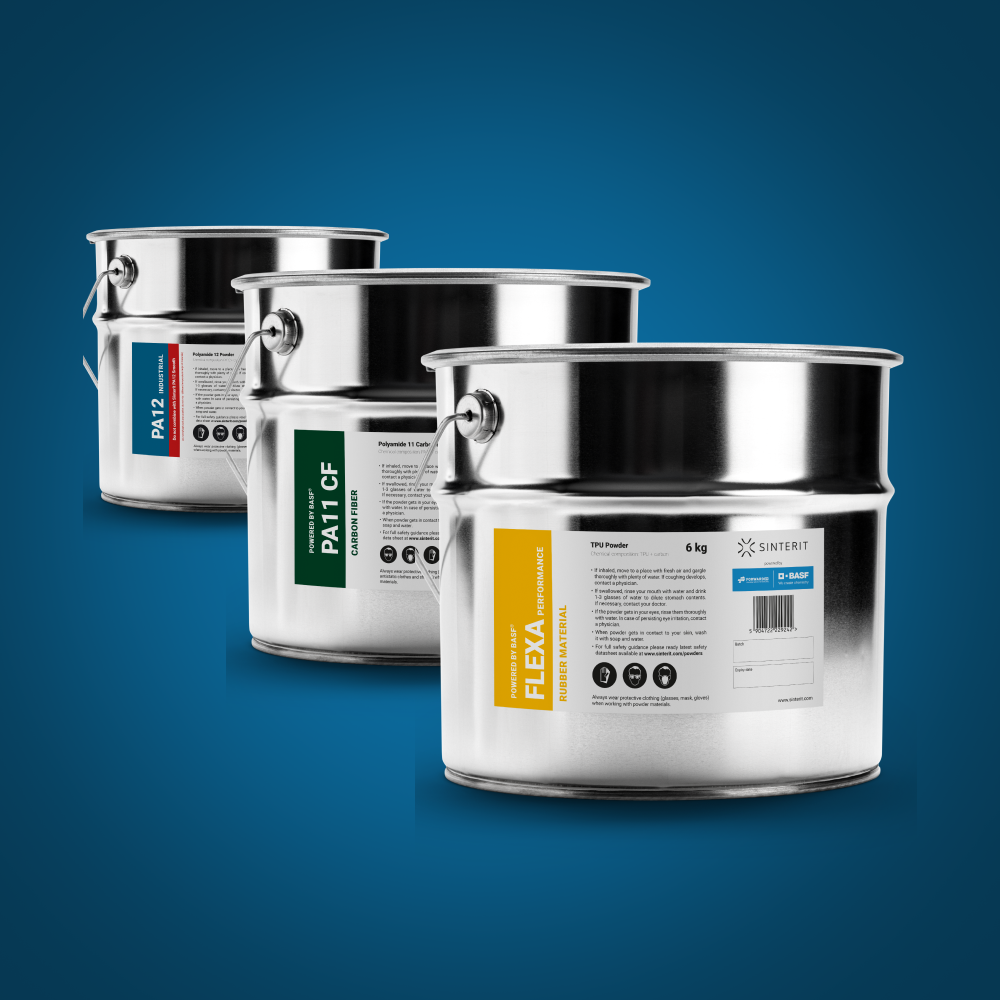
Why do we refresh powder?
In SLS 3D printing technology one of the most important success factors is temperature management. High temperature management, to be precise. Your SLS 3D printer needs to maintain heat close to the melting point of used material, while the laser adds the energy needed to melt the powder according to the STL file. Because of that the unsintered powder is constantly subjected to high temperatures. It causes powder degradation over time.
Another factor is oxidation. If the powder is still in contact with air, it will also degrade. This is one of the reasons why we recommend storing the powder in dedicated containers and adding only the calculated amount of fresh powder, but more on that later.
There is one more concern. The powder used in SLS 3D printing technology isn’t pure. So for example if you expect PA12 to be a pure nylon 12, you need to know that there are some add-ons, such as plasticizers. Thanks to them you could print, but they are also more susceptible to degradation.
To make your powder last longer, you need to add fresh powder after every print cycle. How much do you need?

Image: refresh rate cycle
What is a powder refresh rate?
The powder refresh rate is a minimum ratio of fresh (sometimes called virgin) powder you need to add to your pre-used, unsintered powder to maintain its best printing quality. The lower the refresh rate, the better cost-efficiency you get.
Every SLS 3D printing job leaves you with a lot of unsintered powder. Even if you fill your 3D printing bed with a lot of models, like you can see on the picture below, there is still impressively a lot of free space between models, all of it filled with unsintered powder that worked as a natural support.
Image: what will be the refresh rate for this highly packed print bed?
After taking out the printouts, you can still print with the powder left by refreshing it. For example, to print models presented above, we used 12,73 l of PA12 Smooth powder, while the total volume of the models was about 1371,37 cm3.
The software that manages the SLS 3D printing process – Sinterit Studio, suggested that after you collect the leftover powder, you need to add 2,33 l of a fresh one and you are ready to go with another print job.
Image: typical refresh rate for PA12 powder
Is it difficult to refresh SLS printing powder?
The first question a lot of users have in mind is: do I have to do the maths? No, the software does it for you. All you need to do is to add an amount of powder suggested by it. It can be compared to preparing food according to the recipe, but with just one ingredient. How hard can it be?
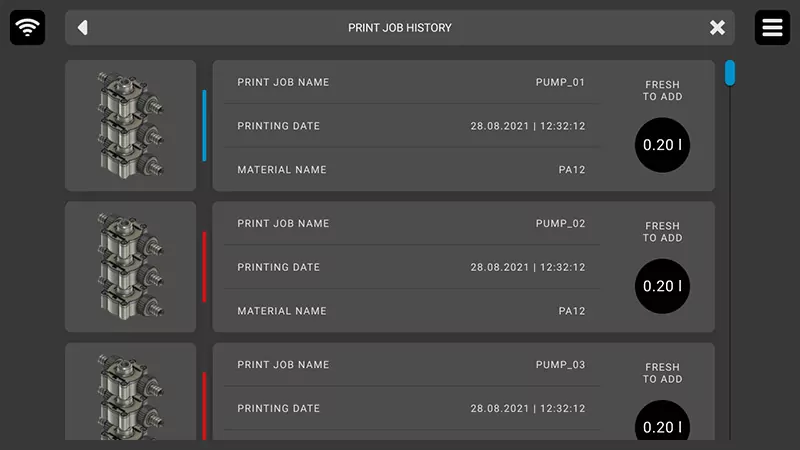
Image: This is how you are notified by the printer of how much fresh powder to add
After adding fresh powder to the used one, you need to mix them together. You can use Sinterit’s Sieve to do it for you automatically. After the sifting ends, you will get a bucket of a print ready powder.

Image: powder sieve as a part of PHS (Powder Handling Station)
What are the refresh rates of Sinterit’s powders?
If you have looked at the offers of various SLS 3D printers producers you may be a little confused about the difference in recommended powder refresh rate. Let’s look at the most popular SLS powder – PA12. This nylon needs refreshing of about 20-30% and most producers operate in this range. If you are printing a lot, this 10% gap may be important for you. So what does it depend on?
First of all it depends on the powder characteristics. In Sinterit we have a dedicated department that tests every powder available on the market, and cooperates with companies such as BASF to create final products that work best with Lisa, Lisa Pro and Lisa X SLS 3D printers. The better quality and longevity of powder means lower refresh rate and more refresh cycle to perform.
Another factor is packing density. Some producers recommend adding as much fresh (virgin) powder as is used to print models. So if your pack density is 25%, then your refresh rate is also 25%. But if you print with smaller density, like below 20% it becomes tricky. It is unrecommended by any producer to add lower than 15% of a fresh powder. But there are some materials, like TPU, which don’t need to be refreshed at all.
Let’s talk
Would you like to know more about refresh rate? Tell us about your application.

Refresh rate for different powders
As PA12 is the most popular, SLS 3D printers give you a lot more powder options. It is especially visible in Sinterit’s powder portfolio which consists of 9 powders with the tenth to be released soon. Some of them don’t need refreshment at all. If you use the Flexa line of powders, elastic TPU materials, your refresh rate will be 0% and you can print with it as long as you are happy with the result.
Image: refresh rate of TPU materials
On the other hand, more rigid materials, such as PA11 have a bigger refresh rate. PA11 Onyx, that is often used for printouts that need to maintain great mechanical properties, impact resistant with high elongation at break offers refresh rate of 33%, the stronger PA11 CF, the strongest and most versatile material available to SLS 3D printers has refresh rate of 40% and the biggest refresh rate you need comes with PA11 ESD, bio-sourced nylon material with heat resistance and ESD functionality.
Image: refresh rate of PA11 ESD material
How many refreshing cycles can I perform?
Powder, as every physical thing, degrades at times. It is hard to determine how many 3D printing cycles are best for it because one is not equal to the other. For example, if you print small parts, and your print job is short, the unsintered powder will stay in a high temperature environment for much less time than when you print nearly a full bed of models. It doesn’t affect your refresh rate. But you need to have in mind that with more cycles the edges of your 3D printed parts could become less smooth and edges less sharp, so if it is a case, you could try to raise your refresh rate a little bit.
Refreshing powder is easy
After reading this article you already know why you need to refresh your powder, what are the recommended proportions for individual types of powders, and that you get the exact amount of fresh powder to add in Sinterit Studio software. All you have to do is pour the amount of fresh powder measured with a measuring cup to the recollected powder. The best way to do this is by using Sinterit sieve which will automatically mix the powder for you. It is simple, and easy. Just like preparing food with just two ingredients. After mixing, we still recommend that you keep the print ready powder in a closed box. Now you are ready to refresh. Oh, and remember to shake the box when it is mixed. At the end of the day some things need to be shaken, not stirred.
Lower the costs of your SLS 3D printing
Read our latest e-book and make your SLS 3D printing more cost-effective
