Wie Innoseal mit Sinterit Lisa X die Prototypenentwicklung und Kleinserienfertigung optimiert hat
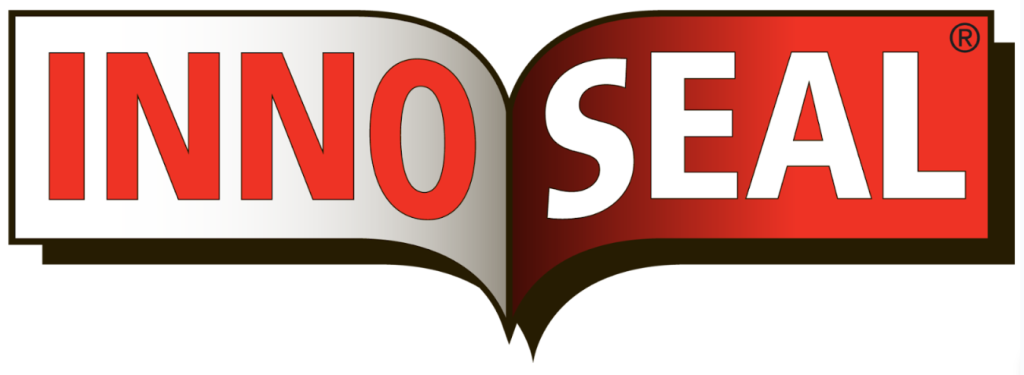
- Unternehmen: Innoseal Europe B.V
- Branche: Verpackungslösungen
- Standort: Tilburg, Niederlande
- Website: www.innoseal.com
Herausforderung: Von Engpässen bei Prototypen zu Innovationsflexibilität
Innoseal Europe B.V., ein führender Entwickler und Hersteller von Verpackungslösungen auf Bandbasis, stand bei der Produktentwicklung vor einer häufigen Herausforderung: der Balance zwischen Qualität, Vorlaufzeiten und Kosten beim Übergang vom Design zur Produktion.
Zunächst setzte das Unternehmen FDM-3D-Druck für Tests und Prototypen ein. Dies brachte zwar in der Anfangsphase einige Vorteile, doch schnell wurde klar, dass die Qualität der Endteile für Funktionstests oder die Kleinserienfertigung unzureichend war.
Traditionell musste Innoseal auf eine erhebliche Marktnachfrage warten, bevor es sich zu teuren Spritzgussformen entschließen konnte – ein Prozess, der mit hohen Vorabinvestitionen und ungewissen Ergebnissen verbunden war. Um das Risiko zu mindern, begann das Unternehmen, den 3D-Druck auszulagern, aber uneinheitliche Lieferzeiten und Bedenken hinsichtlich der Verletzung geistigen Eigentums behinderten die Innovation.
Lösung: Entscheidung für Lisa X und SLS Freedom
Auf der Suche nach einem erschwinglichen, benutzerfreundlichen und materialunabhängigen SLS-3D-Druck-Ökosystem untersuchte das Team von Innoseal die verfügbaren Technologien. Ihre Bewertung führte sie zu Sinterit und sein Lisa X Drucker.
„Wir haben uns andere 3D-Druckverfahren und andere Marken angesehen, uns aber letztendlich für SLS entschieden und Sinterit aufgrund der Kommunikation und der offenen Materialmöglichkeiten ausgewählt. Das konnten wir bei anderen Anbietern von erschwinglichen SLS-Druckern für Einsteiger nicht finden„, erinnert sich Daniel Aarts, Technischer Direktor bei Innoseal Europe.
Ein Besuch in der Fabrik von Sinterit in Polen besiegelte die Entscheidung. “Die Produktion aus erster Hand zu sehen und mit dem Team zu sprechen, hat uns Vertrauen in das Produkt und die Menschen dahinter gegeben.“
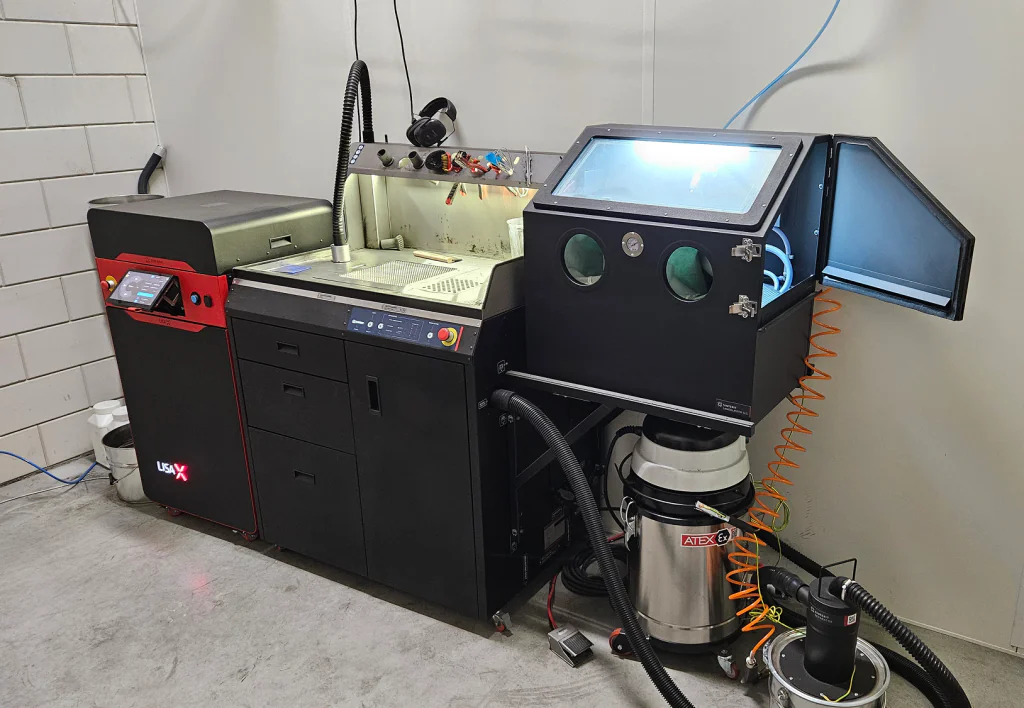
Anwendung: Funktionsteile, Prototypen und Kleinserien
Heute verwendet Innoseal die Lisa X hauptsächlich für kleine Funktionsteile aus PA11 CF und produziert Prototypen und Kleinserien, bis die Stückzahlen einen Wechsel zum Spritzguss rechtfertigen. Mit durchschnittlich 1–2 Drucken pro Monat und Losgrößen von 10 bis 50 Teilen ist die Lisa X zu einem Eckpfeiler des R&Ds sowie der Kleinserienfertigung geworden.
„Bei dem Umfang, in dem wir den SLS-Drucker einsetzen, ist es sinnlos, einen direkten ROI zu berechnen. Allerdings sind Innovationsmöglichkeiten und das Testen neuer Konzepte jetzt viel einfacher geworden. Ein schneller Test oder die Verbesserung bestehender Designs dauert jetzt nur noch Tage statt Wochen“, sagt Daniel Aarts.
Das komplette Sinterit-Ökosystem, einschließlich der Pulverhandhabungsstation (PHS) und des Sandblasters, optimiert die Nachbearbeitung. Trotz der komplexen Geometrien, die für die Teile von Innoseal typisch sind – oft mit kleinen Löchern und Innenkammern – ist die Nachbearbeitung effizient. „Bei CF-Nylon, das von Natur aus rau ist, sind wir mit der Oberflächenqualität sehr zufrieden“, bemerkt Daniel Aarts.
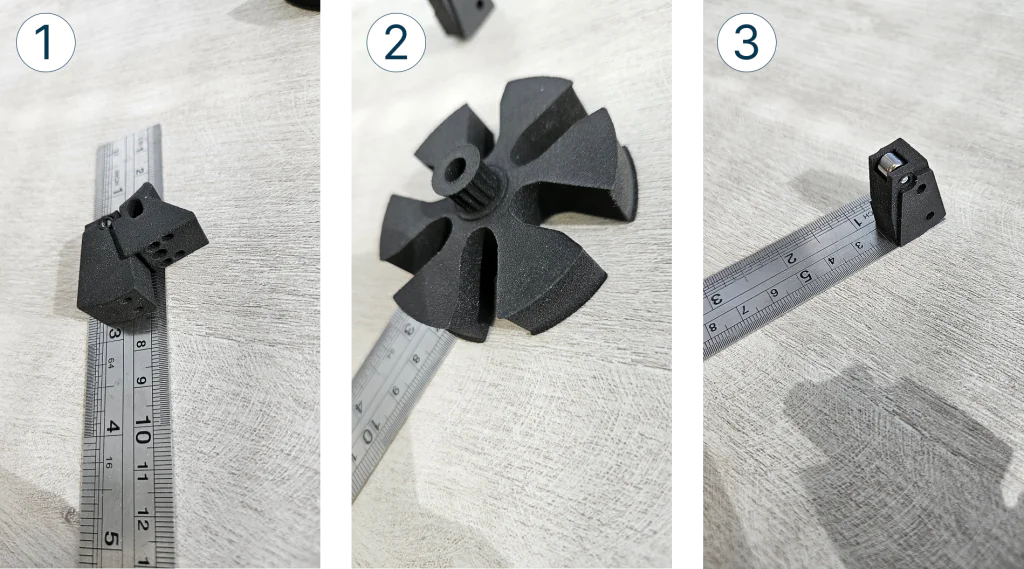
Mit dem Sinterit LISA X-Drucker gedruckte Teile:
- Schieberblock und Einwegverriegelung
- Bandrad
- Einwegverriegelungsblock
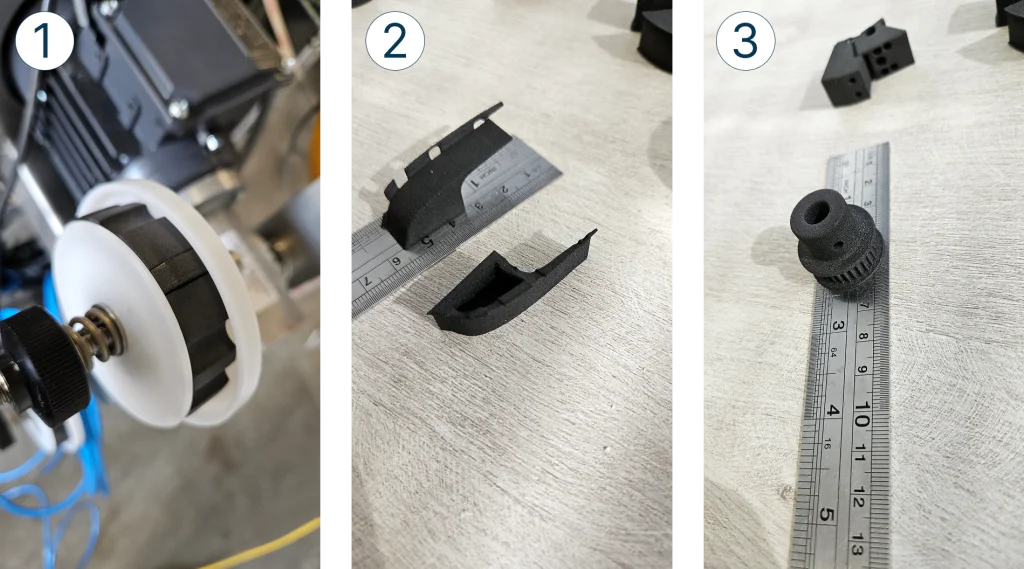
Mit dem Sinterit LISA X-Drucker gedruckte Teile:
- Bandrollenhalter in Sondergröße
- Papierführungsblöcke
- Riemenscheibe und im Hintergrund Schieberblock und Einwegverriegelung
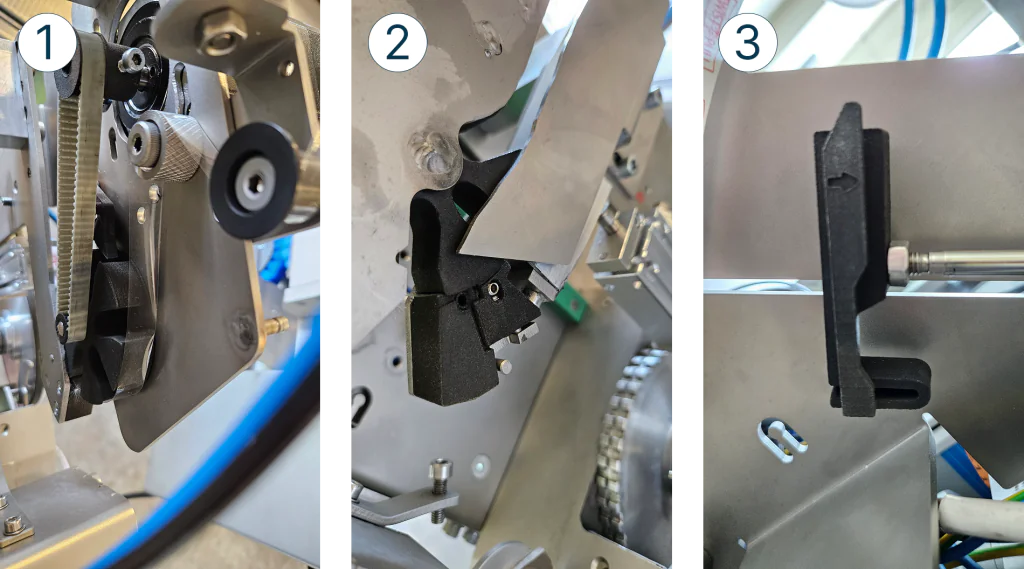
Mit dem Sinterit LISA X-Drucker gedruckte Teile:
- Bandrad in Baugruppe mit Riemenscheibe
- „Bandrad“ in Baugruppe mit dem „Schieber“ und der „Einwegverriegelung“
- Papierklemmmechanismus mit Selbstentriegelung
Auswirkungen: Schnellere Innovation, geringeres Risiko und Kosteneinsparungen
Die Einführung des Lisa X hat messbare Vorteile gebracht:
- reduzierte Nacharbeit an neuen Formen durch Validierung der Teile vor der Formenproduktion,
- erhöhte Flexibilität und Markteinführungszeit, insbesondere bei komplexen Baugruppen,
- beschleunigte Designiterationszyklen, wodurch pro Designüberarbeitung 3–5 Tage eingespart werden.
„Das klingt vielleicht nicht nach viel, aber bei mehreren Überarbeitungen summiert sich das zu einer erheblichen Zeitersparnis“, erklärt Daniel Aarts, Technischer Direktor bei Innoseal Europe. „Wenn wir bei jeder Änderung auf ausgelagerte Fräs- oder Dreharbeiten hätten warten müssen, hätten wir im letzten Jahr mehr als 18 Wochen verloren“.
Am wichtigsten ist vielleicht, dass Lisa X Innoseal zu verrückteren Experimenten ermutigt hat. „Wir können jetzt ‘wahnsinnige’ Ideen ausprobieren, die wir aufgrund finanzieller Zwänge zuvor nicht in Betracht gezogen hätten. Wenn im Bauvolumen noch Platz ist und die Aktualisierungsrate nicht überschritten ist – warum nicht drucken und ausprobieren?“
Lieblingsfunktion: Sorgenfreies Drucken
Daniel betont die Möglichkeit, einen Druck zu starten und wegzugehen, als eines der wertvollsten Merkmale von Lisa X. Im Gegensatz zu FDM, wo Adhäsionsprobleme lange Drucke ruinieren können, bietet Lisa X Zuverlässigkeit und Sicherheit.
„Kein Warten an der Bauplatte, um zu sehen, ob die ersten Schichten haften. Keine ruinierten 48-Stunden-Drucke. Allein das spart uns unzählige Stunden und Frust.“
Bonus-Interview: Lektionen, Überraschungen und Zukunftspläne mit LISA X
Neugierig, wie die tägliche Arbeit mit der LISA X wirklich aussieht? In diesem exklusiven Video erzählt Daniel Aarts, Technischer Direktor bei Innoseal, was ihn in den ersten Monaten am meisten überrascht hat, wie der Drucker ihre Herangehensweise an das Prototyping verändert hat und was den täglichen Betrieb reibungsloser macht als erwartet. Außerdem gibt er Tipps für Unternehmen, die über die Anschaffung ihres ersten SLS-3D-Druckers nachdenken, und gibt einen Einblick in die Zukunft von SLS bei Innoseal und darüber hinaus.
Schaue dich das Video an und lass dich von den Erfahrungen aus der Praxis inspirieren!
Fazit
„Mit Lisa X von Sinterit konnten wir die Vorlaufzeiten verkürzen und bessere Lösungen schneller entwickeln, sodass wir unsere Kunden zufriedenstellen können“, fasst Daniel Aarts zusammen.
Für Innoseal Europe ging es bei der Investition in Lisa X nicht nur um den Druck von Teilen. Es ging darum, Innovationen zu erschließen, Risiken zu reduzieren und die Flexibilität zu gewinnen, um mit der Geschwindigkeit ihrer Ideen Schritt zu halten.