Selective Laser Sintering (SLS) in 3D printing – process, powders, and potential
In the previous article a brief overview on Selective Laser Sintering technique was presented and placed among other 3DP approaches. Now the time has come to dig down into the details of the SLS and unveil its phenomena. You can be confused on how exactly the laser sinters the powder, why we utilise elevated temperature or even why we can use one powdered materials and others not. This article will bring answers to those questions. We will also show the perspectives for research in terms of the SLS process and used powders.
But first things first – let’s make a quick recap on SLS. It is a 3D Printing technique based on polymer or metal powder layer-by-layer sintering in elevated temperature. The recoater distributes the powder on the printer’s bed and then according to the sliced model a layer is sintered. The table moves down by an increment and the process repeats until desired printout is finished.
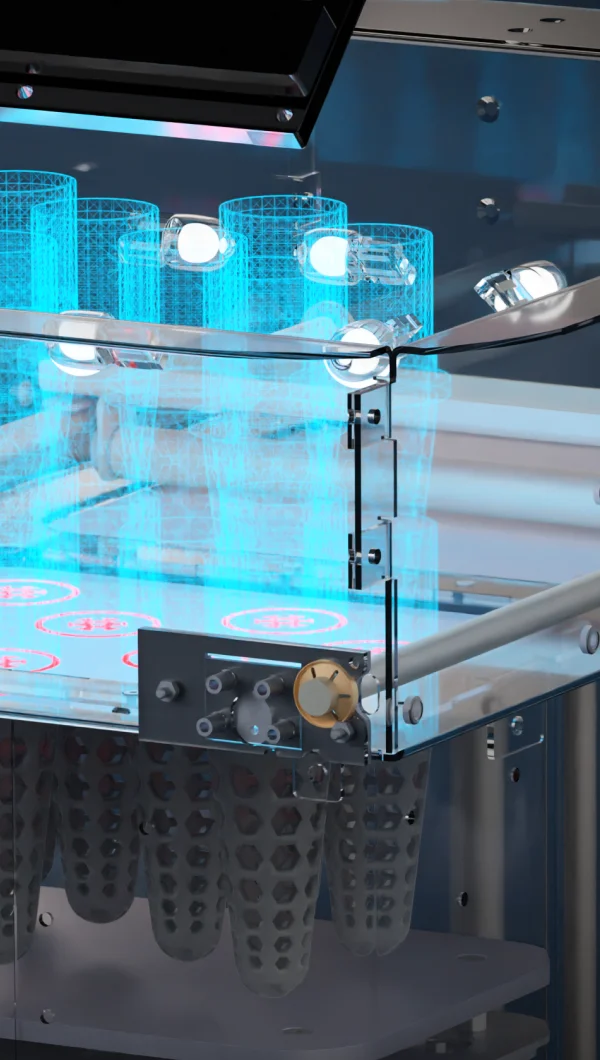
SLS 3D printing powders and how they sinter
Once we are familiar with the process itself, now we can get into details. Namely, how versatile SLS powders can be in terms of mechanical properties and why one can print with one powder and not with the others. There are specific requirements for the consolidation of the powder particles to happen. We need to distinguish between two main categories of materials: metallic and polymeric powders. First group is mostly utilised in automotive and aviation industry whilst the second one covers prototyping, medical purposes, education and small serial production of custom elements.
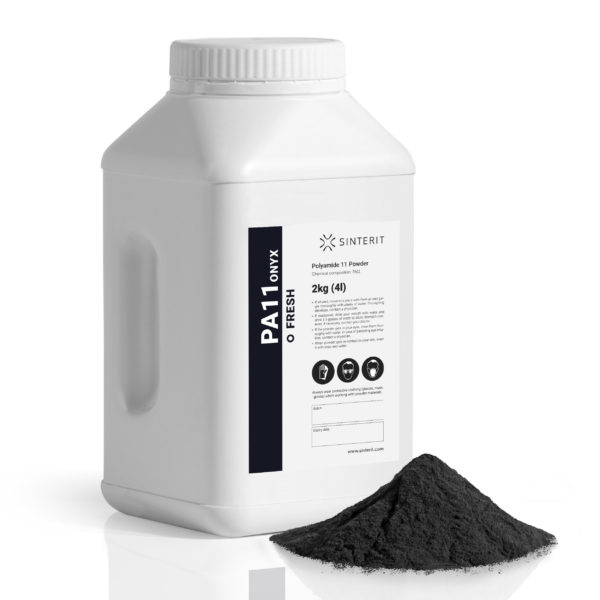
The first and the most vital parameter of the powder is the temperature window in which the sintering may occur. For describing the phenomena we will focus on polymeric powders such as polyamides (PA), thermoplastic elastomers (TPE) and thermoplastic polyurethanes (TPU) widely available in the Sinterit’s offer.
But what are polymers? Imagine a very long chain composed of the same links. This chain is named polymer while the chain link is called monomer. It is formed by a polymerization reaction which adds one compound to the other eventually forming a very long chain. Those types of compounds are present all around us in a variety of different forms. Plastic packages and bottles are polymers of polyethylene (PE), polystyrene (PS) and others. Wood is a polymer of cellulose and glass of cross-linked silicone. Some of them, such as polyamide, utilised i.e in clothing industry can be adjusted for SLS technique.
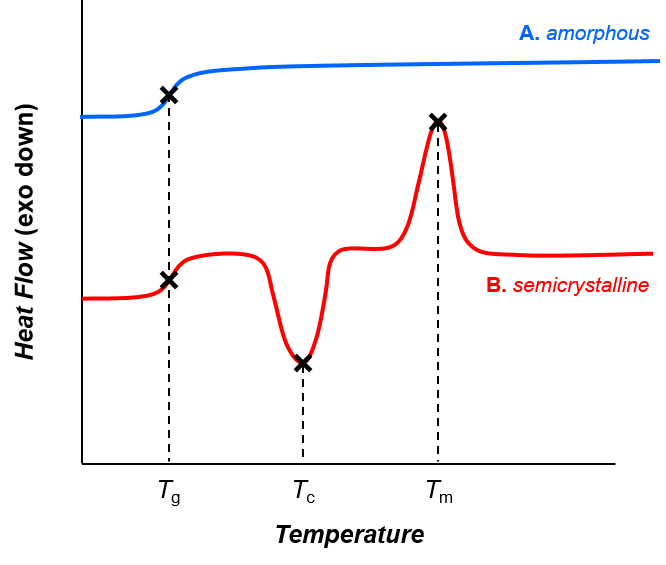
So while we know what are polymers we can distinguish between crystalline and amorphous forms of them. Don’t feel repelled – this is just the nomenclature which implicates their physical states vital for the sintering window. The former’s occur between glass transition temperature and melting temperature and the latter’s between glass transition and flow temperature – usually between 50-200°C.
This window allows diffusion of particles and enhances the bounding process by forming a so-called neck between the grains of powder. During adjusting the temperature we need to be aware that additives to the powder may affect it’s phase transition temperatures and we need to watch out not to melt the powder thoroughly. There is also a coalescence phenomenon called “neck” which happens between two particles start to bound together in elevated temperature. Imagine two spheres in contact with each other slowly merging into one elipse – that’s the thermal coalescence.
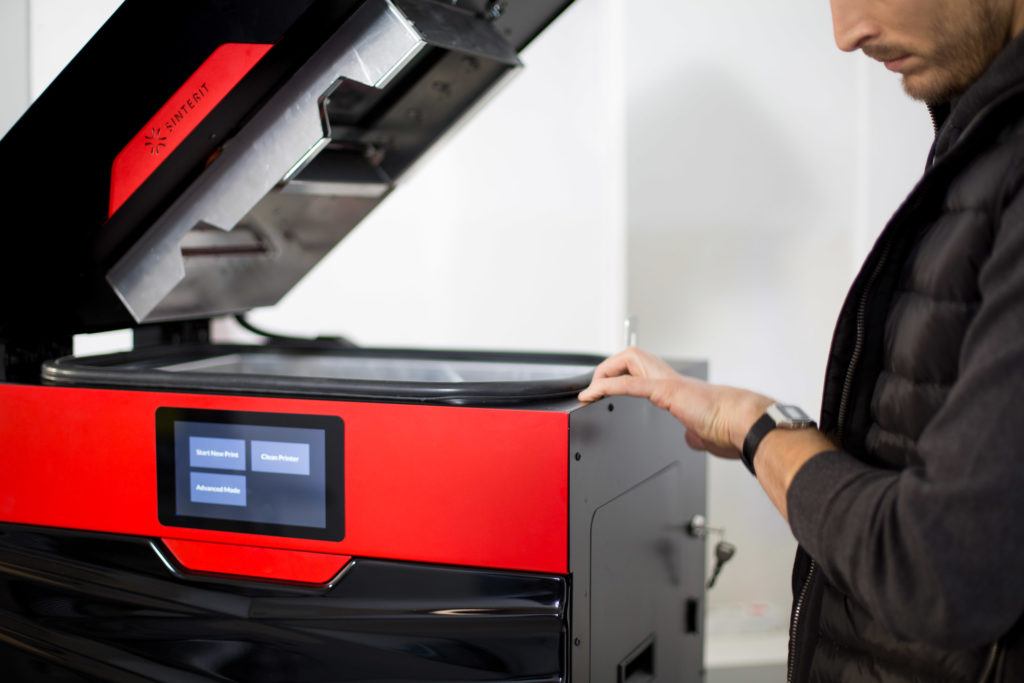
The powder consolidation is finished by a laser beam absorbed by the powder and by polymerizing the chains in the grains, forming a uniform layer of sintered powder. According to the information above the SLS powder’s particles need to possess specific diameter which varies between 45 and 90 μm for the optimal accuracy.
Key parameters in Selective Laser Sintering (SLS)
The spectrum of parameters affecting the Selective Laser Sintering process is extraordinary long! However, some of them are more crucial for the quality and time of the printing. The list consists of the properties of the powder mentioned above such as the sintering window, as well as the chemical character of the substrate which is crucial for the binding process to happen. If the utilised material does not absorb the energy from the laser, we can mix it with some laser absorbing agent – this is however very delicate action and the ratio and chemical nature of the absorber must be adjusted ideally.
This additive can also affect mechanical properties of the printout as well as colour and ageing. Just to add other variables to the equation, imagine that you have to select laser of specific wavelength with the adjusted optics for the print to happen. All of the parameters mentioned above are a great field of academic and industrial research.
How to optimize SLS 3D printing results with powder settings
Being aware of the fact that almost every step on the SLS print journey affects the mechanical properties of the final print, you can play around with adjusting them. You can choose between rigid, soft, rubber and other powders. One simple thing you can do is change the printing temperature in the allowed window and other parameters of the print. It’s really easy to do it using open parameters in Sinterit Studio 2019. Simply adjusting the temperature can alter the mechanical resistance or quality of the model. Open parameters will be addressed in another article hence it is a very interesting manipulation.
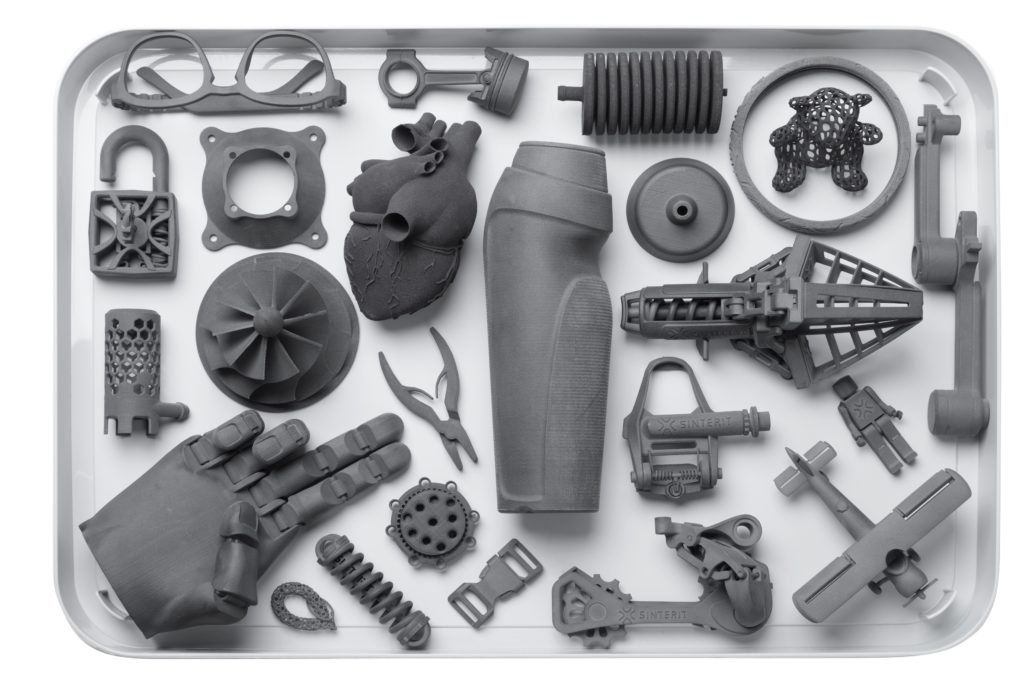
Advantages of Selective Laser Sintering in 3D printing
SLS 3D printing offers unmatched design freedom and does not require support structures. Unlike FDM or SLA, it enables the production of complex internal geometries and mechanically robust prototypes. Selective laser sintering is ideal for applications in engineering, education, automotive, and small-batch manufacturing — making it one of the most advanced 3D printing selective laser sintering methods in the additive manufacturing space.
Outlook
I hope that this article carried you out to the Selective Laser Sintering world and ignited you to think about the complexity of the process and outlook on the future of SLS. I greatly encourage the Academics as well as industry and hobbyists to experiment and put their ideas to the test! If you would like to further deepen your knowledge of Selective Laser Sintering, click here for an easy-to-follow webinar that will guide you through the most frequently asked questions. 3D printing may have a great effect on our future so let’s put effort into shaping it!
Selective Laser Sintering FAQ
Selective laser sintering (SLS) is an industrial 3D printing technology that uses a laser to fuse layers of powdered thermoplastic into solid objects. It allows for high-precision, support-free prints with excellent mechanical properties. This method is widely used in engineering, medical prototyping, and functional product development.
SLS 3D printing begins by spreading a thin layer of powder over a heated bed. A laser then sinters the selected areas based on the sliced model. This process repeats layer by layer until the entire object is formed within the powder bed, which supports it throughout the print.
The most common SLS 3D printing materials are thermoplastic powders like PA12, PA11, TPU, and TPE. These materials are chosen for their durability, chemical resistance, and thermal stability. The powder particle size and sintering temperature range are key to successful prints.
Selective laser sintering 3D printing does not require supports, allowing for complex designs and nested parts. It offers higher mechanical strength than SLA and greater design freedom than FDM. It’s ideal for end-use parts, not just prototypes.
SLS 3D printers and powders can be costly, and the process requires careful powder management. Post-processing such as depowdering is essential. Despite these challenges, it remains one of the most versatile industrial 3D printing methods.
Paweł Piszko
Scientific advisor
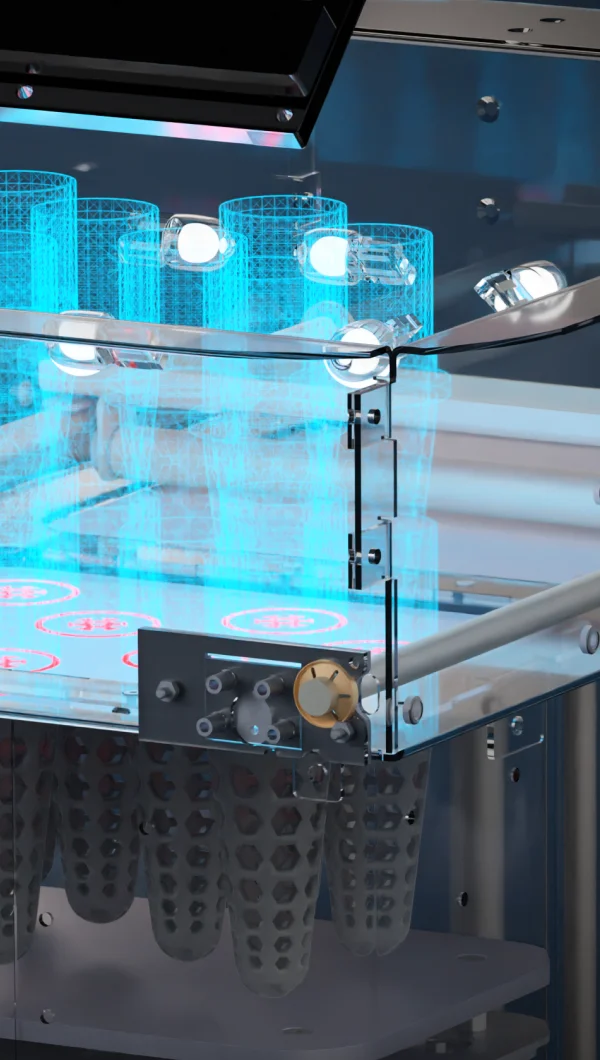