How Innoseal streamlined prototyping and small-batch production with Sinterit Lisa X
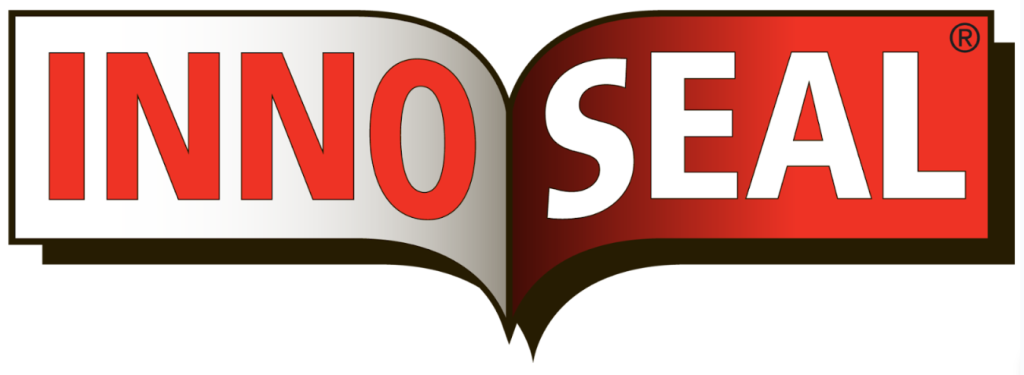
- Company: Innoseal Europe B.V
- Industry: Packaging Solutions
- Location: Tilburg, The Netherlands
- Website: www.innoseal.com
Challenge: From Prototype Bottlenecks to Innovation Flexibility
Innoseal Europe B.V., a leader in developing and producing tape-related packaging solutions, faced a common challenge in product development: balancing quality, lead times, and cost when moving from design to production.
Initially, the company adopted FDM 3D printing for testing and prototyping. While this provided some early-stage benefits, it quickly became clear that the quality of final parts was insufficient for functional testing or small-scale production.
Traditionally, Innoseal had to wait for significant market demand before committing to expensive injection molds — a process that involved large upfront investments with uncertain outcomes. To mitigate risk, they began outsourcing 3D printing, but inconsistent lead times and concerns about intellectual property leakage hindered innovation.
Solution: Choosing Lisa X and SLS Freedom
In search of an affordable, easy-to-use, open-material SLS 3D printing ecosystem, Innoseal’s team explored the available technologies. Their evaluation led them to Sinterit and the Lisa X.
“We have looked at other 3D printing methods, and other brands, but ultimately decided on SLS and chose Sinterit for their communication, and open material possibility. Something we couldn’t find in other suppliers of affordable entry level SLS printers.” recalls Daniel Aarts, Technical Director at Innoseal Europe.
A visit to Sinterit’s factory in Poland sealed the decision. “Seeing the production firsthand and speaking with the team gave us confidence in both the product and the people behind it.”
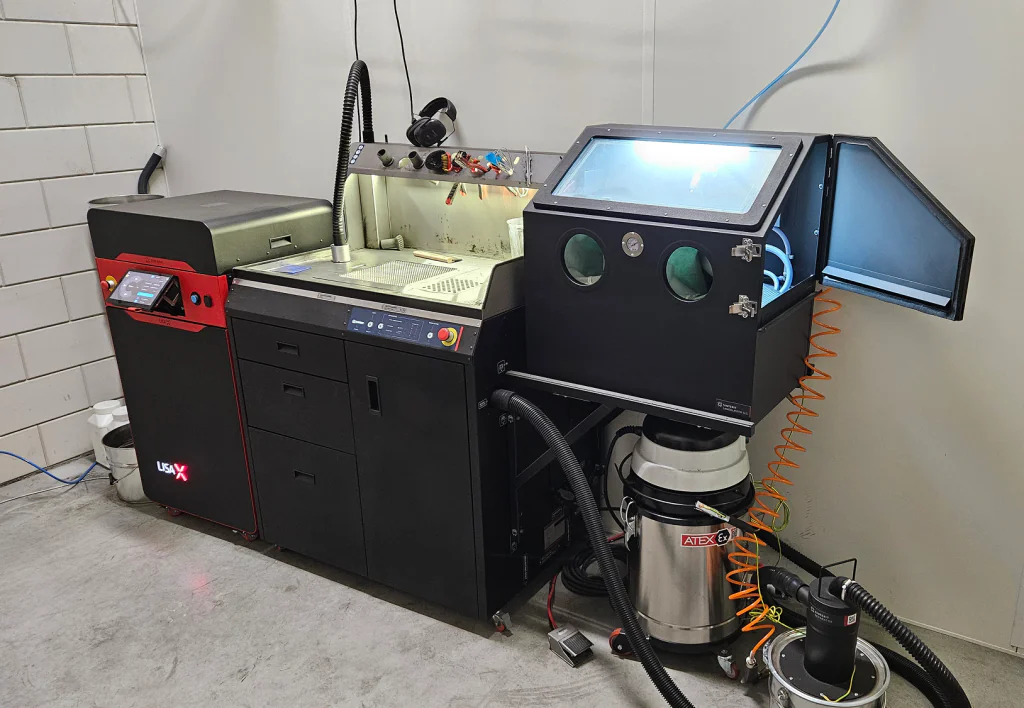
Application: Functional Parts, Prototypes, and Small Series
Today, Innoseal uses the Lisa X primarily for small, functional parts made from PA11 CF, producing prototypes and small series until volumes justify transitioning to injection molding. With an average of 1–2 prints per month and batches ranging from 10 to 50 parts, the Lisa X has become a cornerstone of their R&D and low-volume production.
“Calculating for a direct ROI is pointless on the scale we use the SLS printer. However, innovation possibilities and testing new concepts have become so much easier. Running a quick test or improving existing designs now takes days instead of weeks,” says Daniel Aarts.
The complete Sinterit ecosystem, including the Powder Handling Station (PHS) and Sandblaster, streamlines post-processing. Despite the complex geometries typical of Innoseal’s parts — often featuring small holes and internal chambers — post-processing is efficient. “For CF Nylon, which is inherently rough, we are very satisfied with the surface quality,” Daniel Aarts notes.
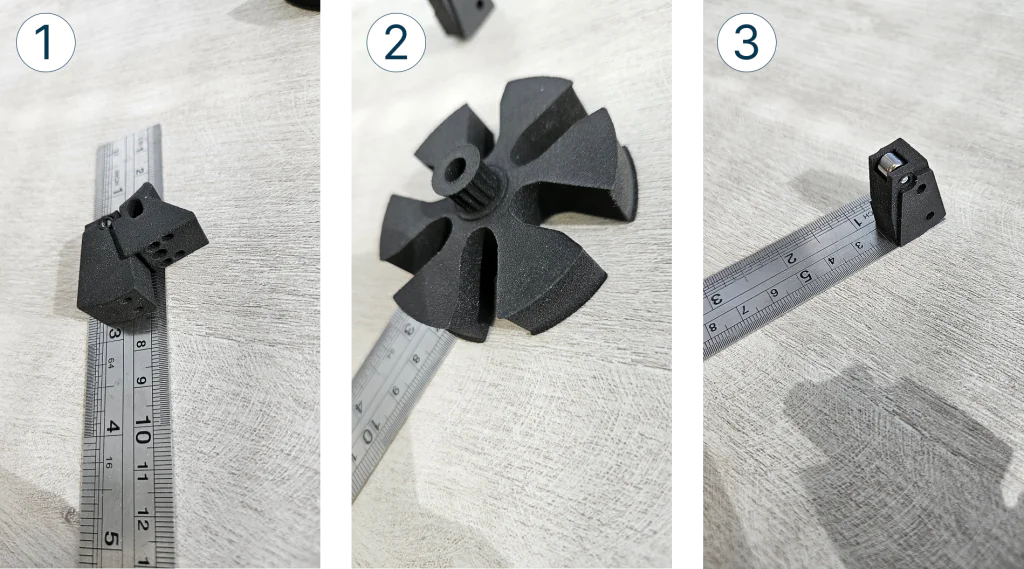
Parts printed with the Sinterit LISA X printer:
- Pusher block and one way lock
- Tape wheel
- One way lock block
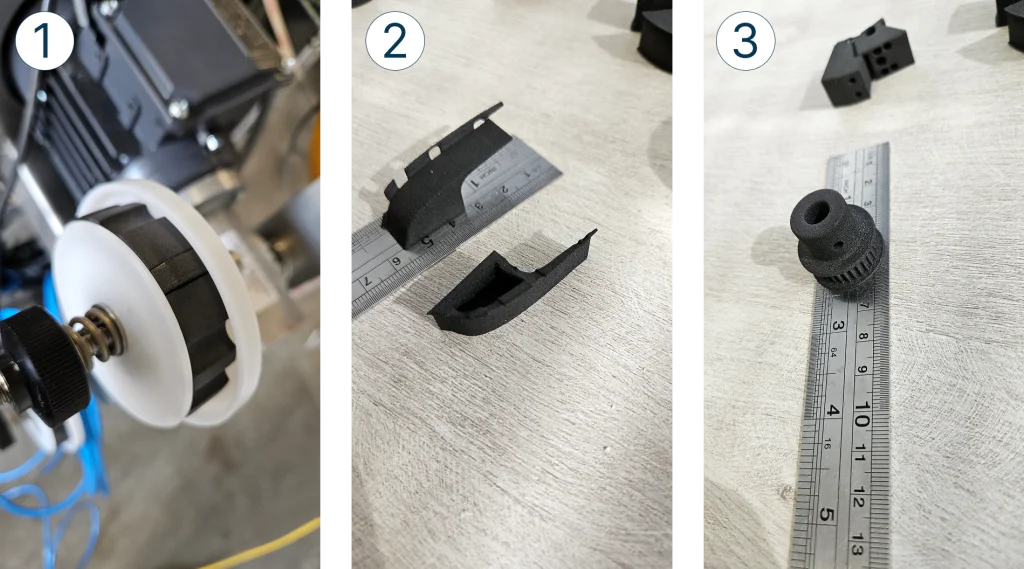
Parts printed with the Sinterit LISA X printer:
- Tape roll holder custom size
- Paper guide blocks
- Pully and in background pusher block and one-way lock
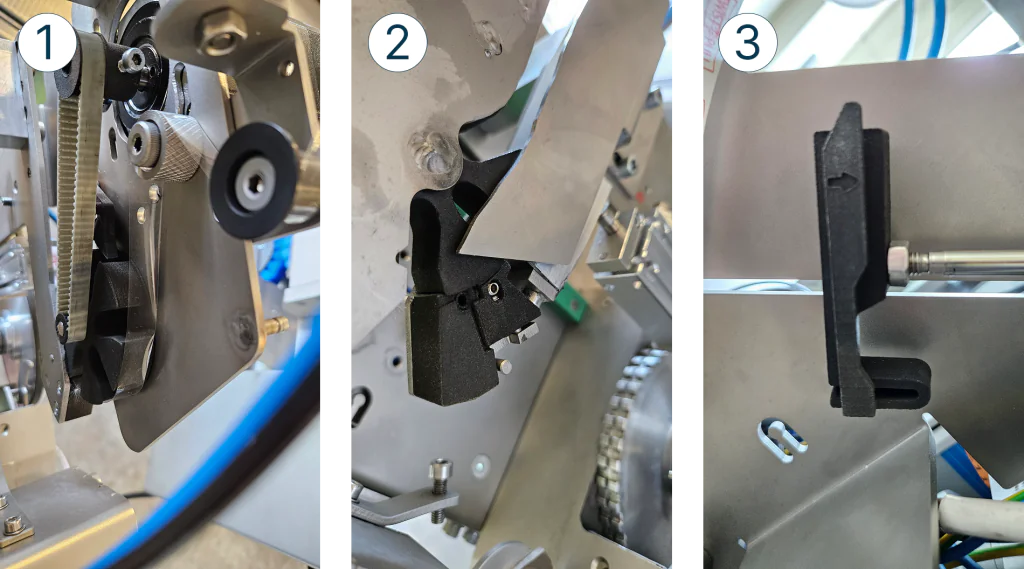
Parts printed with the Sinterit LISA X printer:
- Tape wheel in assembly with pully
- “Tape wheel” in assembly with “pusher” and “one way lock”
- Paper clamping mechanism with self release
Impact: Faster Innovation, Reduced Risk, and Cost Savings
Implementing the Lisa X has produced measurable benefits:
- Reduced rework on new molds by validating parts before mold production.
- Increased flexibility and time-to-market, especially for complex assemblies.
- Accelerated design iteration cycles, saving 3–5 days per design revision.
“It might not sound like much, but over multiple revisions, it adds up to significant time savings,” explains Daniel Aarts, Technical Director at Innoseal Europe. “If we had to wait on outsourced milling or lathing for each change, we would have lost more than 18 weeks over the past year.”
Perhaps most importantly, Lisa X empowered Innoseal to experiment more boldly. “We can now try ‘wild’ ideas that we wouldn’t have considered before because of financial constraints. If there’s room left in a build volume and it’s under the refresh rate — why not print and try?”
Favorite Feature: Worry-Free Printing
Daniel emphasizes the ability to start a print and walk away as one of Lisa X’s most valuable features. Unlike FDM, where adhesion issues can ruin long prints, Lisa X offers reliability and peace of mind.
“No waiting at the build plate to see if the first layers stick. No ruined 48-hour prints. That alone saves us countless hours and frustration.”
Bonus Interview: Lessons, Surprises & Future Plans with LISA X
Curious about what it’s really like to use the LISA X day to day? In this exclusive video, Daniel Aarts, Technical Director at Innoseal, shares what surprised them most in the first months, how the printer changed their approach to prototyping, and what makes daily operation smoother than expected.
You’ll also hear their advice for companies considering their first SLS 3D printer – and a glimpse into the future of SLS at Innoseal and beyond.
Take a look and get inspired by real-world experience!
Final Thoughts
“Sinterit’s Lisa X has allowed us to reduce lead-times and create better solutions — faster, helping us satisfy our customers,” concludes Daniel Aarts.
For Innoseal Europe, investing in the Lisa X was not just about printing parts. It was about unlocking innovation, reducing risk, and gaining the flexibility to move at the speed of their ideas.