SLS 3D printing costs – the easy way to calculate
Understanding and managing SLS 3D printing costs is an important aspect of SLS 3D printing. Unlike SLA and FFF, calculating the cost of printing is quite tricky; in SLA, we can just measure how much resin we used, in FFF we can weigh the model with its support structures, or the spools of material before printing and after. In SLS things get more complicated – we have powder that needs to be refreshed and this costs money too.
In this article, we’ll try to demystify the process of calculating the cost of your prints. The great thing is that this method can be applied to any SLS 3D printer
Table of Contents
- General assumption
- Types of Powders and Their Roles in 3D Printing
- SLS 3D printing costs components
- Steps needed to calculate the printing cost
- Powder density, sintered powder density
- Step 1 – Calculating the powder sintered into models
- Step 2 – Calculating the initial amount of powder
- Powder refresh ratios
- Step 3 – Calculating the amount of refreshing powder
- Step 4 – Calculating how much of the used powder to reject
- Step 5 – Calculating the final SLS 3D printing costs
- Conclusion
General assumption
Let’s assume that we bought enough of the powder of our choice to fill the entire reservoir for the powder and therefore utilise 100% of the printer’s capabilities. The cost of returning to this state will effectively be the SLS 3D printing costs. To make things a bit easier we don’t have to consider the entirety of the powder in our possession, it will be enough to get back to the amount of the same conditions we had before the start of the printing. This calculation also doesn’t assume loss of powder caused by non-perfect efficiency, sandblasting or caused by user error.
In this article, we will use the easiest way to calculate the cost of printing, without focusing on nuances of optimisation. Here you can learn more about the ways of optimization, while the more in-depth calculation will be presented in a follow-up article.
Types of Powders and Their Roles in 3D Printing
Before we start calculating the SLS 3D printing costs, we first need names for the different types of powder used in the process:
- Used Powder: Powder in a “cake” that has not been sintered after printing.
- Fresh Powder: Material used to refresh used powder.
- Print-Ready Powder: A blend of used and fresh powder, ready for the next printing cycle.
- Models: (sintered powder) Powder that has been sintered into models during printing.
Additionally, the cake is an industry-wide name for a block of unsintered powder with printed models inside. This is what we remove from the printer after the printing process.
SLS 3D printing costs components
During the cleaning process after the print is done, the powder is separated from the models. First, we need to compensate for the powder that was sintered into models and also calculate the powder needed for refreshing. Combining the cost of both we will get the total cost of powder.
The volume of fresh powder equal to powder sintered into models will be added to the used powder to compensate for the printed models. Depending on the powder used in the printing process and the percentage of build occupied by the actual printouts this amount might be enough to reach the right ratio of used powder to fresh powder to refresh the used powder. If not, an additional amount, of fresh powder will be added to get to the right refresh ratio.
Steps needed to calculate the printing cost
- Determining the volume of powder sintered into models (this is the first component of cost)
- Calculating the initial volume of the powder, before the printing
- Determining the amount of fresh powder needed (this is the second component of the cost)
- Calculating the amount of used powder to be rejected
- Calculating the final SLS 3D printing costs
Powder density, sintered powder density
During the printing process particles of powder are melted together, removing the gaps between them. This increases the density of the material. As a rule of thumb, we can assure that the density of the loose powder is half of the density of the sintered powder. The table below shows the densities of all Sinterit powders. For third-party materials, these values can be obtained from their manufacturers.
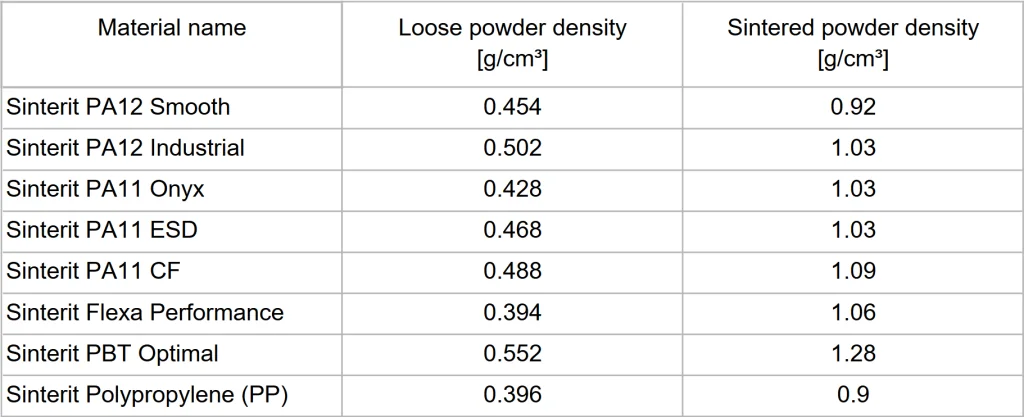
Step 1 – Calculating the powder sintered into models
In the first step of determining the cost of printing, we need to know what was the amount of powder that sintered into models. As the density of loose powder and sintered powders are different we need to accommodate this change:
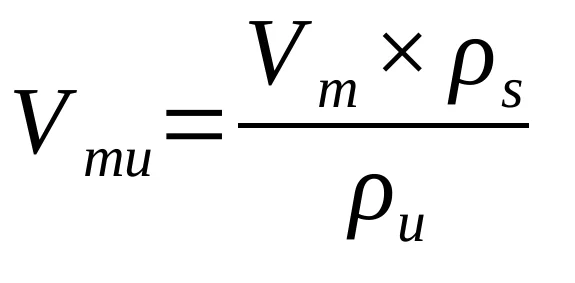
where:
Vmu – volume of powder sintered into models,
Vm – volume of models (marked in Sinterit Studio as “Total print height”),
ρs – sintered powder density,
ρu – loose powder density.
Step 2 – Calculating the initial amount of powders
In the second step of determining the cost of printing, we need to find out what was the amount of powder that ended up in the cake.
Note that this amount is different from the volume of powder needed in the reservoir before the printing process, as some of the powder will end up in the overflow bin. Because the powder in the overflow bin has been only exposed to high temperature for a brief moment, it doesn’t degrade and therefore doesn’t require refreshing, making it irrelevant in this calculation.
First, we need to calculate the volume of used powder:
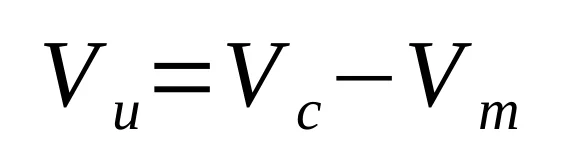
where:
Vu – volume of used powder
Vc – volume of cake
Vm – volume of models (marked in Sinterit Studio as “Models volume”)
The volume of the cake can be calculated based on the height of the build:
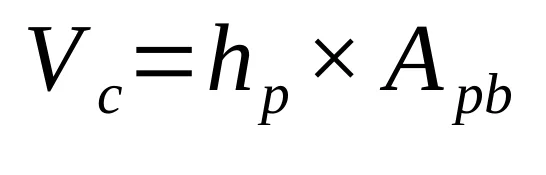
hp – height of the cake (marked in Sinterit Studio as “Models volume”)
Apb – surface area of print bed (for Lisa X – 294.80 cm²)
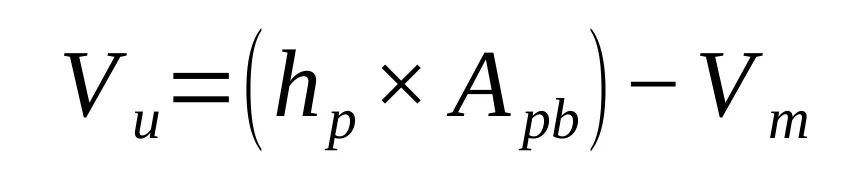
When we combine the volume of powder sintered into models with the volume of used powder we will get:

where:
Vi – volume of powder before printing.
Powder refresh ratios
The refresh ratio determines the amount of fresh powder in print-ready powder. The remaining powder is the used powder.
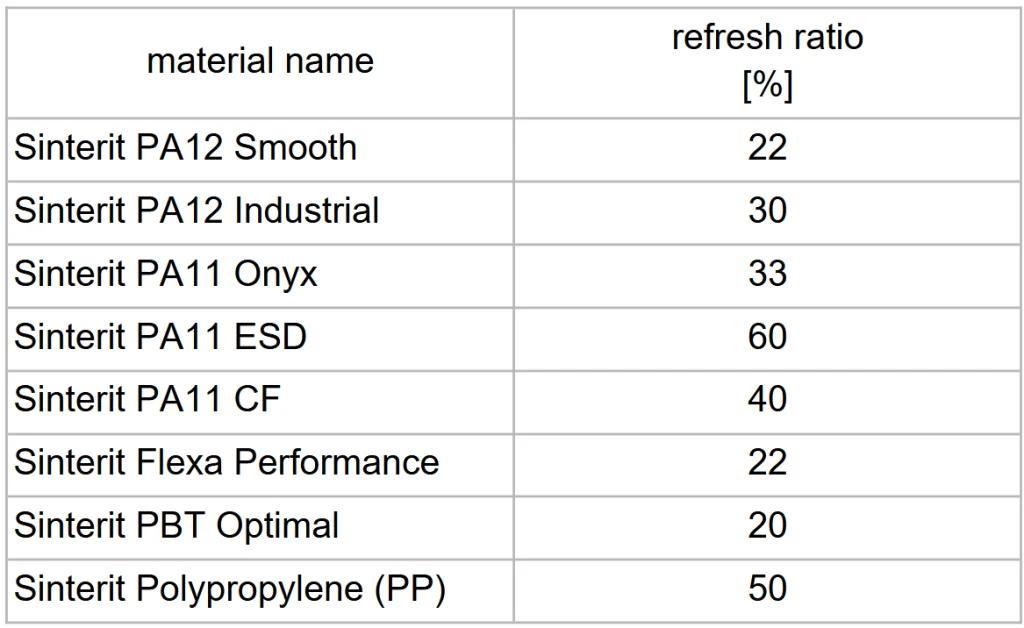
Step 3 – Calculating the amount of refreshing powder
In the third step of determining the cost of printing, we are calculating how much powder we need to add for refreshing.
First, we need to calculate what’s the minimal amount of fresh powder required in the initial amount of powder.
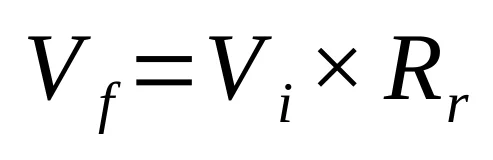
where:
Vf – volume of fresh powder in the initial volume of powder,
Rr – refresh ratio for the selected material.
Now we can calculate the actual amount of refreshing powder we need to add to the used powder along with the fresh powder we add to compensate for the models:

where:
Vfmax – volume of fresh powder to be added
Step 4 – Calculating how much of the used powder to reject
If the volume of the models is very low compared to the volume of the cake it might be beneficial to reject some of the used powder in order not to refresh its entirety. Refreshing everything will require more fresh powder, driving the cost of printing higher. Additionally after refreshing the amount of print-ready powder is higher than the initial amount of powder, which, with subsequent prints will cause a growing amount of excess powder. To alleviate this, we can simply reject a small amount of used powder and not refresh it.

where:
Vumax – volume of used powder to be refreshed.
Step 5 – Calculating the final SLS 3D printing costs
Combining the volume of powder sintered into models with the powder needed for refreshing we get the total powder used for the printing process. This volume can be then calculated into the weight of the powder which will allow you to calculate the final cost of printing.

where:
Ctotal – total cost of printing,Vftotal – total volume of powder,
Cp – cost of powder per 1g.
This cost can be a basis to calculate ROI.
Conclusion
Is it complex to calculate SLS 3D printing costs?
Calculating the SLS 3D printing costs printing may seem complex at first, but by breaking it into logical steps, you can gain full control over your printing expenses. From understanding the different types of powder involved to calculating powder refresh ratios and determining how much fresh powder is needed, this guide provides a straightforward approach to managing costs.
Is it the best way to calculate 3D printing costs in SLS technology?
The outlined method ensures precision and flexibility, allowing you to adapt calculations based on your specific materials, printer type, and project requirements. Using this method we can not only quite simply calculate the cost of printing but also make sure to somewhat optimize the refreshing cost by not refreshing the entirety of the used powder. There are however other possible approaches to this topic that can significantly impact the final calculated cost, for example changing the general assumption that we are only refreshing to reach the initial amount of powder.
Author: Jakub Malec
Application Engineer with six years of experience working with SLS 3D printing. He specializes in helping businesses discover how SLS 3D printing can empower their productivity and optimize costs.