Open parameters: how to start experimenting with SLS powders
Motivation of adjusting the printing parameters
As mentioned in the previous articles, there is a wide variety of polymer powders suitable for the SLS technology. You may ask, how come that the materials have such different properties? Polyamide (PA) is strong and resistant while thermoplastic polyurethane (TPU) is elastic and rubber-like. To answer those questions you need to zoom in into the molecular structure of the polymers.
Quick recap: polymers are macromolecules formed by the same or different molecules bound together into a chain. Just for the scale – those chains can possess thousands of monomer units inside its structure. Moreover, those chains can be cross-linked or chemically modified to achieve desired properties. Of course in the frames of SLS technology powdered polymer mixture need to possess characteristics required for the sintering to happen. It is all about the chemical nature, structure and most important physicochemical parameters.
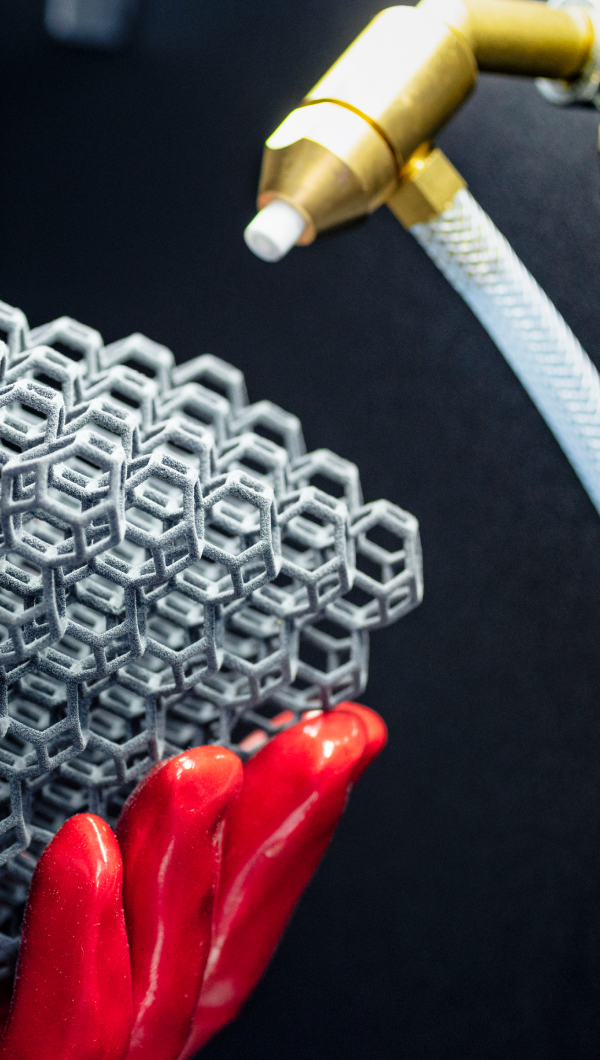
Thermal parameters
Once you have a SLS-ready mixture, you can adjust the bed temperature and laser beam power for the printout to have certain properties. You need to take into consideration crystalline state of the powder and most importantly the Differential Scanning Calorimetry (DSC) data to determine the sintering window (described in the previous article).
If you are at the lower limit of the sintering window, you limit the coalescence of the particles before sintering, but you restrict the flow of the powder maintaining the printout dimensions. If the temperature is too low, you won’t succeed in binding the particles together resulting in the failed print.
If you increase temperature to the end of the sinterint window, the situation reverses: you can achieve more “melted” state of the powder and better binding but on the other hand it can increase the desired dimensions. Adjusting the temperature of the bed might be time consuming, but you can achieve desired resolution and mechanical properties of the final model. Remember that for the commercially available powders the bed temperature values shall be given by the manufacturer.
Tip |
We can offer you a few valuable tips regarding adjusting the parameters when using Lisa or Lisa PRO printers. Namely, if you increase the temperature or lower the laser beam power, you lower the probability of the model bending when using polyamide-based powders like PA12 Smooth or PA11 Onyx. If you experience well-baked “cake”, but the models are curved or tucked up you need to increase the cylinder temperature. |
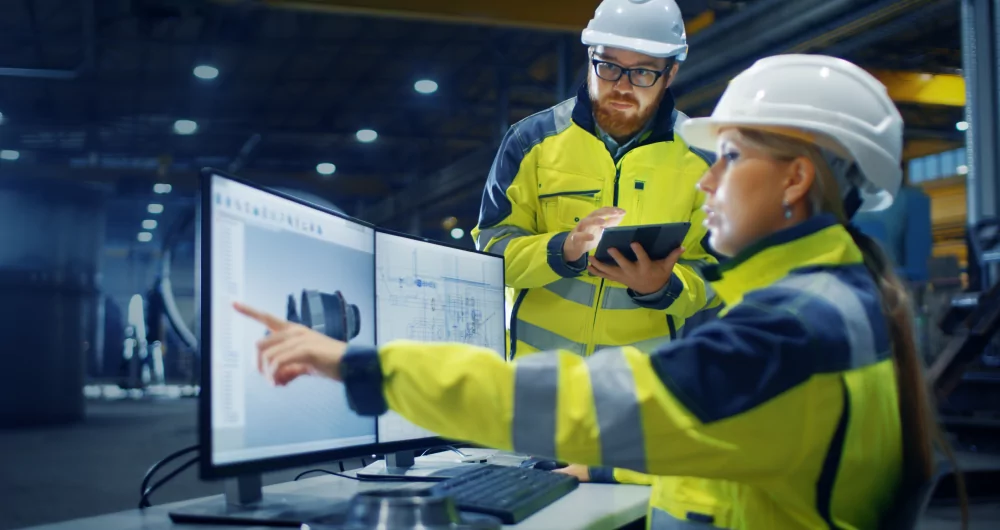
Playing with the laser
Once you are familiar with the flow of the material and you are certain that the powder density and the particle size will not affect the sintering process (i.e. electrostatic attraction of the powder to the recoater), you can proceed to adjusting the laser.
The most important thing to do if you want to submit the material to the laser sintering is checking if your mixture absorbs the laser wavelength. The absorption of the beam is essential for the binding process – if it is not present, you can simply burn the powder or else – nothing will happen. If you do not care about the final colour of the model and your powder is not affected by the beam, you can always mix it with few percents of the carbon adsorber (it affects final mechanical properties very briefly). Feel free to experiment with different compositions of the powder. However, you need to remember to clean the interior of the printer carefully if you want to change the material.
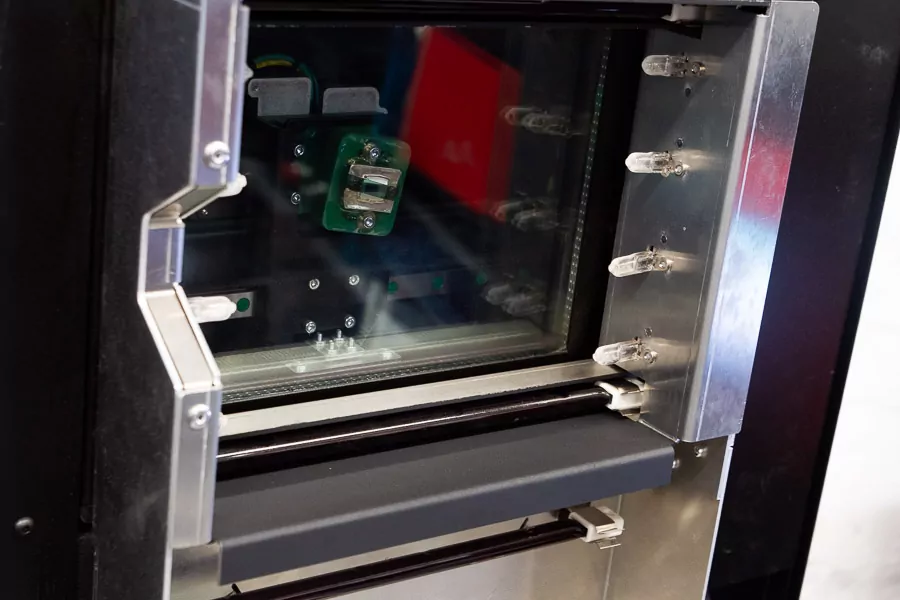
Tip |
There is a great example for adjusting the laser power for our rubber-like TPU-based powders such as Flexa Grey or Flexa Soft materials. If you go up with the power, you can greatly increase stiffness and elongation at break in exchange for a loss in detail quality. It is up to you and your printout usage whether you want to alter those properties. |
If your powder is fragile and you are aware that the laser might damage the polymer structure, you need to lower down the power. If you want to sinter the layers stronger, you can increase the power output. You need to have in mind that laser is capable of altering and even damaging the structure if you overpass a certain value.
Tip |
Another valuable tip is that if you experience delamination of the final model it is a sign that you have to go up with the laser power significantly. |
Open Parameters in Sinterit printers
All of the parameters mentioned above are named Open Parameters and you can play with them in the Sinterit Studio software for our printers. It is an essential tool if you want to alter the properties of the prototype. If you want to feel the Open Parameters power feel free to print the same model on “rigid” and “flexible” parameters using TPU-based powder.
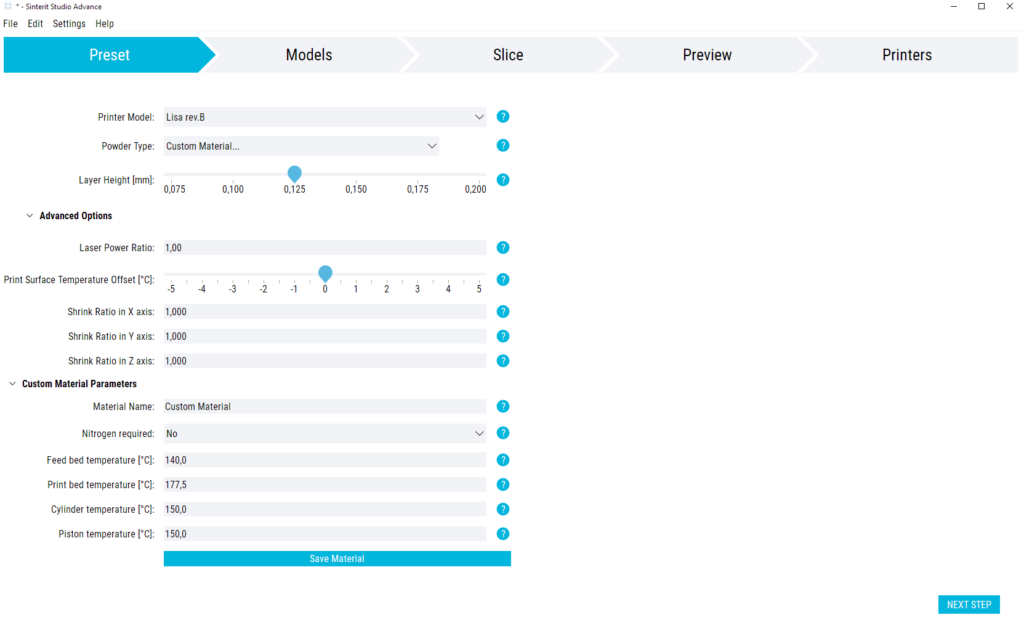
You need to distinguish between two different manipulations around the Open Parameters: playing around with them if the material is commercial and manipulation ranges are given by the manufacturer is more safe, but if you are introducing your own, powder you need to have some patience and have in mind that you might fail. Please remember that all of available SLS systems differ with the construction, sintering parameters and material accessibility.
It is even harder to compare desktop, affordable printers such as Lisa or Lisa PRO with huge and expensive industrial setups. Experiment with parameters, try to introduce new materials and remember that the 3D printing technologies are the future and not everything is yet explored and introduced to those techniques! Stay tuned for forthcoming updates!
Paweł Piszko
Scientific advisor
Lower the costs of your SLS 3D printing
Read our latest e-book and make your SLS 3D printing more cost-effective
