Open 3D Printing Environment – What You Gain by Choosing it?
Adapt to win
In the dynamic world of 3D printing, adaptability, cost-efficiency, and innovation reign supreme. Open 3D printing environment offer a powerful alternative to their closed counterparts, granting users more flexibility, creative control, and opportunities for experimentation. This article explores the advantages of open selective laser sintering (SLS) systems focusing on user benefits, customizable features, and applications in research, development, and beyond. Let’s begin!
Table of Contents
- What is an open system?
- What a good Open SLS system should have?
- The Power of Openness
- Tailored to Your Needs
- Efficiency and Cost Optimization
- A Researcher’s Playground
- Beyond Research: Real-World Applications
- Why Choose an Open 3D Printing Environment?
- Be Smart = Be Flex
What is an open system?
While most of the printers on the market lean toward closed systems that can only used with the printing materials supplied by the printer manufacturer, some devices allow for the use of third-party materials, which opens a whole universe of new possibilities; from wild adjustments applied for first-party powders, through using different or cheaper powders than those offered by the manufacturer, to using completely innovative or unusual materials.
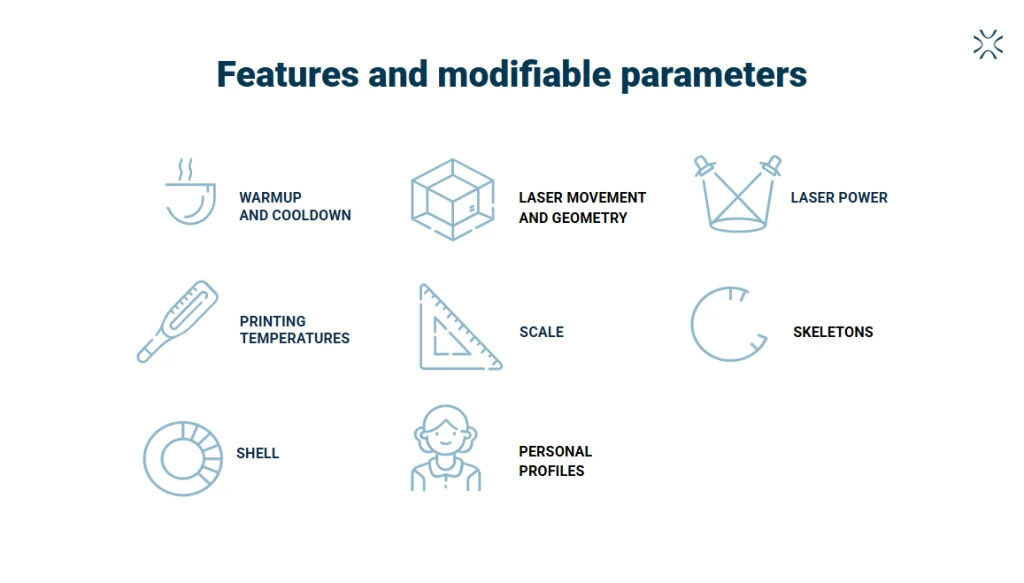
What a good Open SLS system should have?
Much like luxury means a different thing for different car manufacturers, the term “Open System” may describe a different scope of openness from printer to printer. There are however aspects of the printing process, control of which is crucial for the system to be considered open. The most important are:
Layer height
Shorter layer heights (~75μm) allow for higher details and lower the risk of surface defects. Taller layers (125μm and above) allow for the usage of coarser powders or shorten the printing time.
Temperature settings
Controlling the temperature of the powder in various parts of the printer allows for achieving the temperatures required by the sintering process, ensures steady and uniform cooling, and prevents excessive degradation of the material.
Laser adjustments
Probably the most important parameters that make the system open are those related to the laser. Controlling the laser power output makes sure that the right amount of energy is delivered while adjusting the paths of the laser helps get great mechanical and visual properties of the printout.
Inert atmosphere
A lot of the SLS materials can be printed without the presence of inert gas in the printing chamber, but some materials require an oxygen-free atmosphere inside the device. It is vital for the printer to have the option to plug in a source of inert gas, that prevents degradation of the powder.
Powder management
Another important thing is controlling the way the printer manages powder; how much powder is taken for each layer from the reservoir, how long the printer waits between recoatings, and how tall are the buffers on the bottom and top of the case.
Quick switching
Last but not least – switching between materials should be quick, easy and shouldn’t require additional accestorie. This allows for faster development of the powder profiles for existing materials and is invaluable during the development of new powders.
The Power of Openness
Open 3D printing environment unlock immense potential by enabling user-defined control over printing parameters. In the case of Sinterit’s open SLS systems, users have access to over 32 adjustable parameters allowing you to control everything from heating elements distributed across four zones in the Lisa printer series, through the laser power output to various parts of the model, to the pattern of laser paths used in the sintering process. Additionally, switching materials takes only half an hour, which can really hinder the development using big machines.
“With open parameters, you can fine-tune your settings to suit diverse materials and achieve desired mechanical or geometric outcomes.” – Konrad Głowacki, Sinterit’s Materials Line manager.
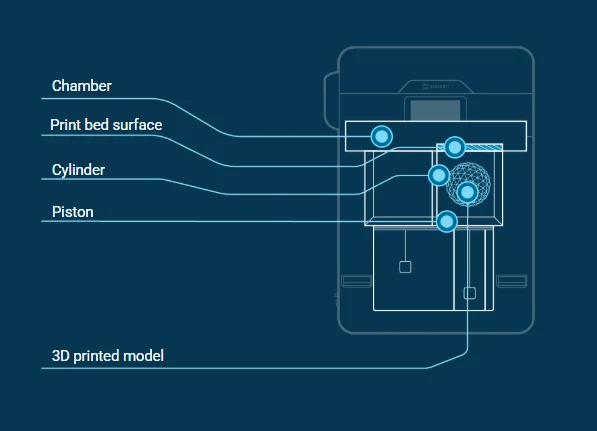
Tailored to Your Needs
Material Compatibility
Open systems are compatible with various materials, broadening the scope of applications. Whether you’re working with PA11 for impact resistance or PP for chemical resistance, these systems support a variety of materials, fostering innovation without being locked into proprietary options.
Easy Start
If you decide to use third-party material you don’t have to start from scratch – using one of the existing profiles makes a great starting point for your newly chosen powder.
Customizable Printing Parameters
Users can tailor their prints for specific applications with adjustable hatch spacing, laser power, and thermal settings. This allows for printing models with non-typical mechanical properties.
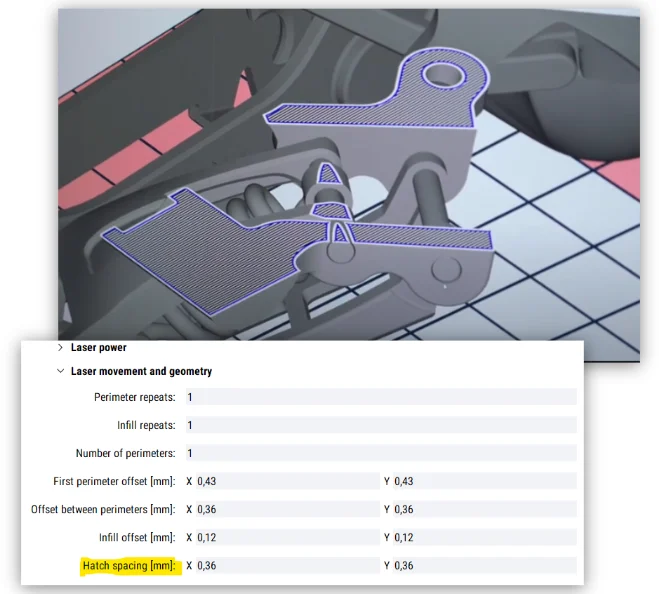
Efficiency and Cost Optimization
- Auto-Nesting for Maximum Efficiency
Sinterit’s auto-nesting functionality optimally arranges models within the printer’s chamber, maximizing space utilization along the Z-axis and reducing waste, but still preserving your optimal rotation of models. - Lower Costs with Minimal Material Waste
Open systems like Sinterit’s allow users to test new materials with as little as 1 kg of powder. Quick material changes (15 minutes) also streamline the process and reduce labour costs. - Exceed your expectation
In some cases, an Open system can allow for achieving results that seemed impossible at first glance – alteration of the amount of powder spread on each layer or printing only the shell of the model allows you to get 100% out of your printer.
“One month of dedicated work can yield 80 test runs with four different settings per print.” – Piotr Hulbój – R&D Manager
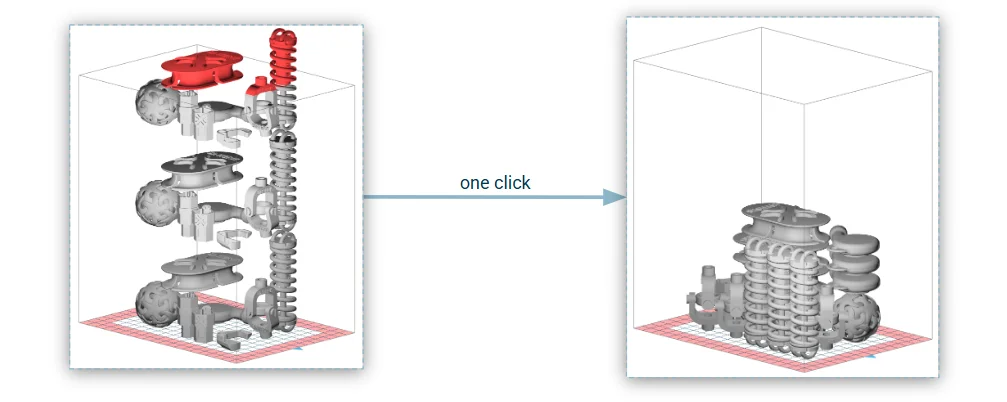
A Researcher’s Playground
- Rapid Experimentation
Researchers benefit immensely from open environments. The ability to manipulate parameters such as laser power and hatch spacing allows them to conduct thorough tests on novel materials. - Applications in Specialized Fields
Open SLS systems have been used to print pharmaceutical tablets, enabling batch-to-batch production and personalized dosages. This demonstrates the versatility and cost-effectiveness of such systems in niche applications.
“Printing pharmaceutical tablets reduces processing steps while allowing personalized dosage forms.” – Prof. Dennis Douroumis, University of Greenwich.
Explore our case study, showcasing the potential of an open 3D printing environment: Producing specified drug tablets with LISA.
Beyond Research: Real-World Applications
- Engineering and Prototyping
Engineers can explore material properties like strength and energy density, tailoring their designs to suit mechanical performance needs. - Education and Training
The intuitive design of systems like Sinterit makes them ideal for educational settings, helping users learn the intricacies of SLS printing. - Business and Product Development
Open environments enable businesses to refine products, optimize costs, and even offer custom solutions to clients. Designers can experiment with limitless material possibilities without relying on subcontractors.
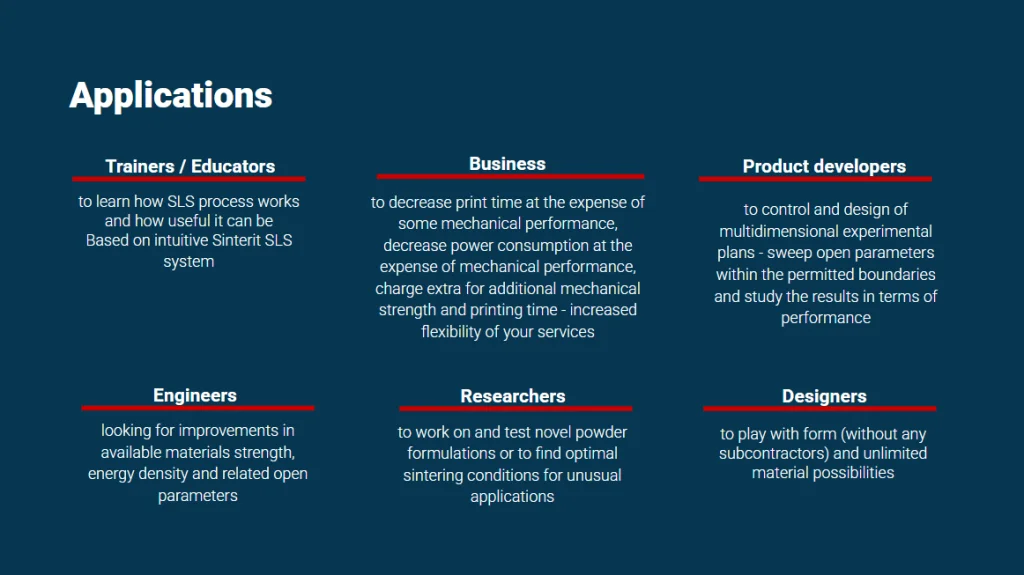
Why Choose an Open 3D Printing Environment?
- Unmatched Flexibility
From mechanical adjustments to geometric precision, the ability to modify printing parameters ensures high adaptability for diverse applications. - Innovation at Lower Costs
Open systems reduce entry barriers, making advanced technology accessible to small businesses and researchers alike. - Fostering Innovation
By removing proprietary constraints, open environments allow users to focus on creativity and problem-solving.
“Open systems are not just for researchers; they’re for anyone seeking innovation at an affordable price.” – Carl Fruth, CEO of FIT Additive Manufacturing Group GMbH
Be Smart = Be Flex
Choosing an open 3D printing environment like Sinterit’s SLS systems means embracing a world of possibilities. Whether you are conducting cutting-edge research, developing products, or looking to enhance your educational offerings, the freedom and flexibility of open systems provide unparalleled opportunities. The ability to fine-tune parameters, test new materials, and optimize costs makes this approach a game-changer in the evolving landscape of 3D printing.
“Compact, powerful, and open – the key to innovation lies in flexibility.” – Tony Stark 😉
Author: Tomasz Frąckiewicz
AM Sales Manager with over 12 years of experience in distribution in more than 50 countries on 4 continents. Specialized in analyzing and introducing laser technologies into distributorship portfolios or customer business models. Privately, an avid traveler, a new tech freak, and a modern art & music enjoyer.