FDM vs SLS – est-ce vraiment comparable ?
Chaque fois qu’un fabricant d’imprimantes 3D compare différentes technologies sur son blog, cela peut sembler délicat. Surtout lorsqu’il ne propose qu’un seul des types comparés. Ce billet de blog n’a pas pour but de faire l’éloge du SLS. Nous n’allons pas chercher à classer le bon, le mauvais et le moins bon parmi les technologies de fabrication additive les plus populaires. Elles ont toutes leur importance, et le dernier conseil que nous donnerions serait d’acheter une imprimante 3D SLS si votre application relève purement du FDM.
Le FDM, une technologie d’impression 3D universelle et accessible
Existe-t-il une technologie d’impression 3D universelle adaptée à toutes les applications ? Le FDM semble correspondre à cette définition. Elle est abordable et très accessible, avec la plus large gamme de matériaux disponibles sur le marché. Vous pouvez opter pour une marque reconnue ou choisir un kit DIY venu de Chine. Tout dépend de votre budget et des projets que vous réalisez.
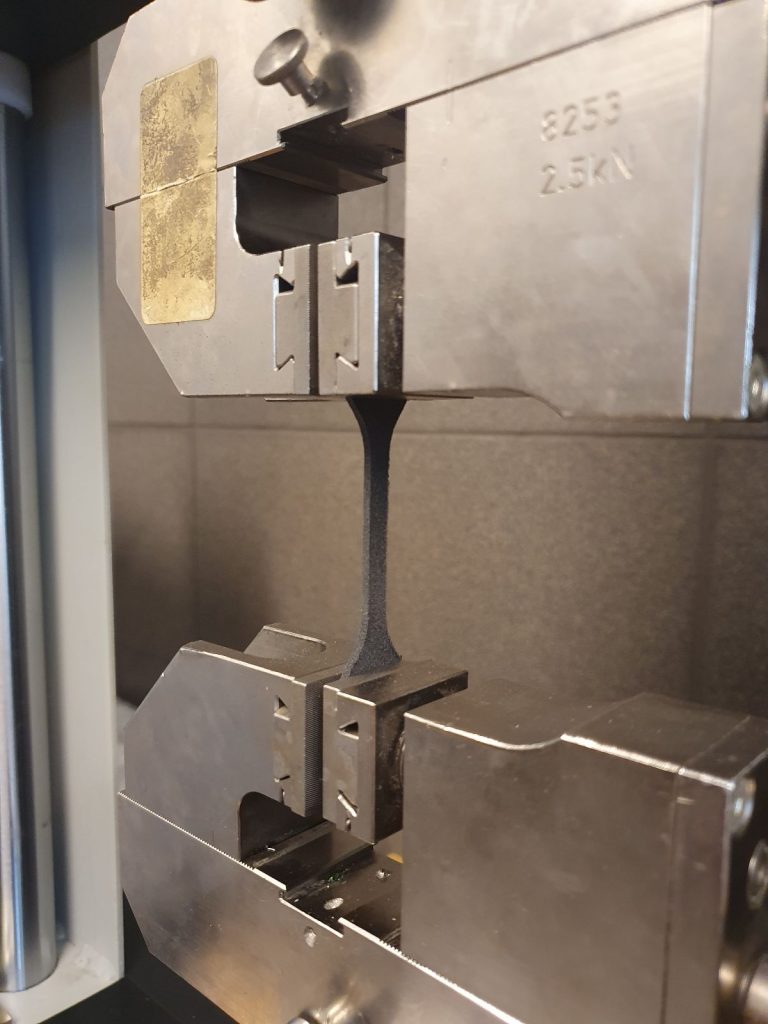
D’un côté, on trouve une véritable machine de guerre, comme le décrit Markforged avec son OnyxPro – une imprimante 3D révolutionnaire conçue pour les pièces renforcées en fibre de verre continue. Les pièces imprimées sont extrêmement solides. Mais de l’autre côté, on peut aussi acheter une imprimante sans marque, suffisante pour imprimer un 3DBenchy, mais pas beaucoup plus.
Avec un spectre aussi large, où chacun peut choisir l’imprimante 3D qui lui convient le mieux, on peut sans hésiter désigner le FDM comme la technologie numéro un de la fabrication additive.
Qu’est-ce que le FDM ?
Quand on parle de FDM, on désigne en réalité le procédé FFF – fused filament fabrication. FDM, pour fused deposition modelling, est une marque déposée de Stratasys. Néanmoins, même les leaders du secteur utilisent ce terme, tout comme en Pologne, on appelait autrefois toutes les baskets des “Adidas”, quelle que soit leur véritable marque.
Dans cette technologie (que nous continuerons à appeler FDM, car c’est le terme le plus couramment utilisé), un filament continu de matériau thermoplastique est acheminé depuis une bobine (parfois de grande taille, parfois non) vers une tête d’impression chauffée et mobile. Il est ensuite déposé couche par couche sur la pièce en cours de fabrication. Certaines imprimantes FDM sont équipées de plusieurs extrudeurs, comme la Markforged OnyxPro mentionnée plus tôt – le premier dédié à l’impression d’onyx (extrudeur plastique), le second assurant le renfort en composite (extrudeur pour fibre). D’autres fabricants utilisent deux extrudeurs pour appliquer un matériau de support hydrosoluble, une fonctionnalité que l’on retrouve sur certaines imprimantes Ultimaker.
Regardez le webinaire
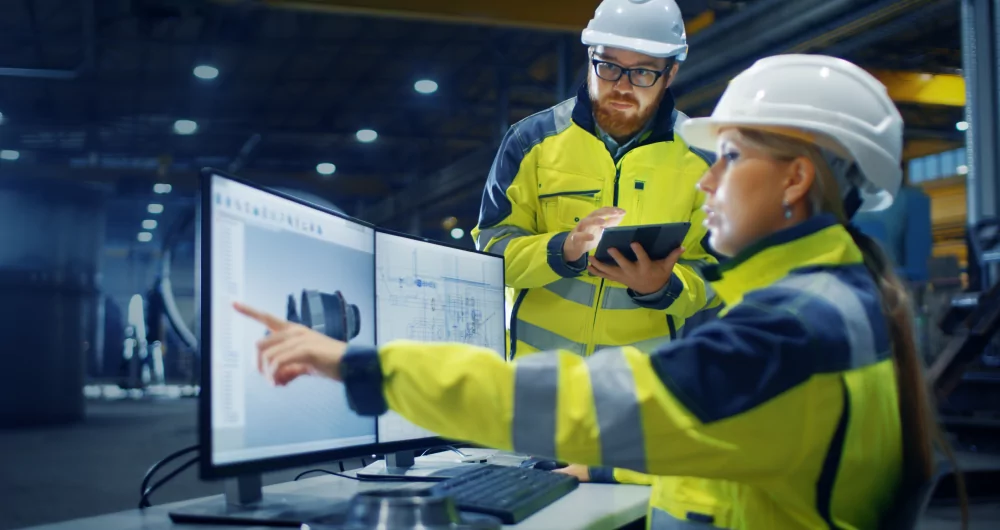
Comment le FDM gère-t-il la gravité ?
Toutes les technologies d’impression 3D doivent composer avec la gravité. Construire une impression couche par couche, c’est un peu comme bâtir une maison. Si les murs sont droits, tout se passe bien. Mais dès que des parties en surplomb apparaissent, cela devient plus complexe. Tout comme les entreprises de construction utilisent des étais métalliques, les imprimantes FDM résolvent ce problème grâce à des supports spécifiques. Vous n’avez même pas besoin de les concevoir vous-même – le logiciel d’impression 3D les génère automatiquement et les imprime en parallèle.
Une fois votre pièce terminée, vous pouvez détacher les supports facilement à l’aide d’un couteau, d’une pince à bec fin ou d’une pince coupante. Dans certains cas, lorsque les supports sont solubles dans l’eau, il suffit de plonger votre impression dans un seau rempli d’eau.
Certains fabricants FDM proposent des plateaux d’impression rotatifs capables de changer d’angle pendant le processus, ce qui réduit le nombre de supports nécessaires. C’est une solution plutôt astucieuse.
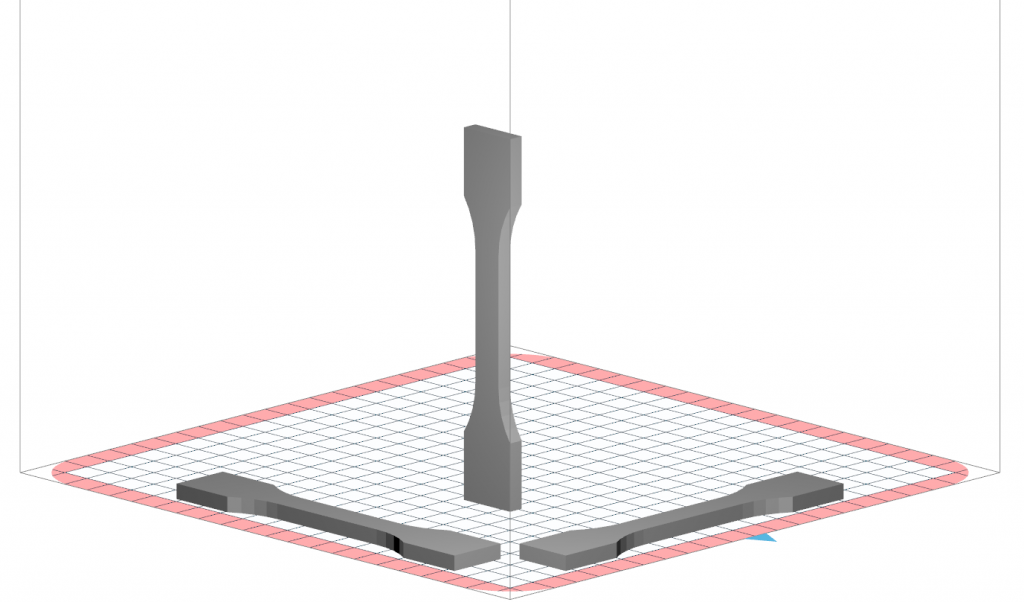
Le FDM pour les grandes pièces
Si vous recherchez de grands volumes d’impression, le FDM peut être le meilleur choix. Les principaux fabricants FDM proposent des imprimantes 3D avec un plateau d’impression de 330 x 240 x 300 mm pour moins de 6000 USD. Mais il est également possible de trouver des marques moins connues offrant des imprimantes FDM avec un plateau de 600 x 600 x 660 mm (0,25 m³) pour moins de 5000 USD. Si vous comparez cela aux 550 x 550 x 750 mm (0,23 m³) proposés par l’une des plus grandes imprimantes 3D SLS pour polymères du marché – dont le coût total avec les équipements périphériques, l’installation et la formation peut atteindre 1 million USD – vous sentez tout de suite la différence.
Pourquoi les filaments FDM semblent-ils plus résistants que les poudres SLS ?
Comme mentionné précédemment, certaines imprimantes FDM permettent de produire des pièces extrêmement résistantes, renforcées par des fibres de carbone. Mais pour une imprimante FDM typique, la résistance mécanique reste un point faible. Cela peut sembler difficile à croire lorsqu’on lit la fiche technique de certains filaments FDM. Si vous comparez la résistance à la traction de certains filaments nylon PA12 disponibles pour les imprimantes FDM avec celle de la poudre de nylon PA12 utilisée dans les imprimantes SLS, les premiers peuvent paraître plus performants. Mais ce n’est pas le cas. Pourquoi ?
Principalement parce que les pièces imprimées en FDM sont anisotropes. L’isotropie est un concept issu de la science des matériaux, qui signifie que les propriétés sont identiques dans toutes les directions. Par exemple, les pièces fabriquées par injection ou thermoformage présentent des propriétés isotropes, elles sont donc aussi résistantes selon les axes X, Y et Z. Pour les besoins de ce billet, on peut en faire une règle générale – même si certains polymères, comme les polymères à cristaux liquides, restent hautement anisotropes, même en injection.
L’anisotropie ne vient pas uniquement des matériaux utilisés en FDM, mais du procédé lui-même. La manière dont les pièces sont construites en FDM est fondamentalement anisotrope. Il est relativement facile d’arracher ou de casser une pièce FDM, surtout entre les couches. Mais à quel point est-ce facile ?
La résistance des pièces imprimées en 3D peut être mesurée et normalisée à l’aide de la résistance à la traction, c’est-à-dire la capacité à résister à une rupture lorsqu’elles sont soumises à une tension. Cet indicateur, largement utilisé dans l’industrie de l’impression 3D, s’exprime en mégapascals (MPa) ou en livres par pouce carré (psi) aux États-Unis, et il est essentiel pour les ingénieurs et les concepteurs lorsqu’ils recherchent un matériau ou une technologie pour des applications mécaniques. Lors du test de résistance à la traction, une éprouvette normalisée est étirée et un tensomètre enregistre le niveau de tension auquel le matériau se rompt.
En consultant les fiches techniques des filaments FDM, vous pourriez être surpris par la qualité des chiffres annoncés. La plupart des filaments nylon affichent une résistance à la traction comprise entre 50 et 80 MPa. En comparaison, le PA12 de Sinterit atteint seulement 32 MPa, ce qui pourrait faire croire que le FDM est gagnant dans cette catégorie. Mais il y a des nuances importantes.
Quatre chercheurs du département de génie mécanique de l’université chrétienne Petra en Indonésie ont testé l’effet de l’orientation dans le dépôt de filament fondu. Ils se sont intéressés à l’ABS – le matériau dont sont faits les célèbres briques Lego. Des éprouvettes de traction ont été imprimées avec du filament ABS de Bits from Bytes selon trois orientations différentes : à plat, sur la tranche et à la verticale. Ils ont ensuite effectué des tests de résistance à la traction sur chaque échantillon et ont constaté que l’orientation influence bel et bien la résistance.
L’éprouvette imprimée à plat s’est rompue à 6,8 MPa, celle imprimée sur la tranche était la plus résistante et s’est rompue à 7,66 MPa, mais la plus faible – imprimée à la verticale – s’est révélée beaucoup plus cassante. Elle s’est rompue à 3,31 MPa. La raison pour laquelle cela se produit en technologie FDM est que l’anisotropie se manifeste surtout à l’endroit où les couches se rejoignent. Il est donc important de garder à l’esprit que la résistance à la traction indiquée sur la boîte de votre filament ou dans sa fiche technique décrit celle du matériau brut, pas celle du modèle imprimé en 3D.
La bonne nouvelle, c’est qu’il est possible de renforcer vos pièces même avec l’impression FDM. En augmentant le pourcentage de remplissage (infill), vous pouvez rendre la pièce plus solide. Il en va de même si vous augmentez l’épaisseur des parois externes (shell thickness). Vous pouvez aussi opter pour un matériau plus robuste ou essayer d’imprimer votre pièce selon une orientation différente. Pour savoir comment orienter correctement votre pièce, vous devez d’abord déterminer dans quelle direction s’exercera le plus souvent la contrainte. Mais cela reste une solution de fortune, car dans certains cas, vous ne voulez pas modifier votre modèle – vous avez besoin qu’il soit résistant tel qu’il a été conçu. À quoi cela ressemble-t-il en technologie SLS ?
Le SLS pour des pièces plus solides
Les pièces imprimées en SLS sont, contrairement au FDM, presque isotropes. Cette technologie utilise un laser comme source d’énergie pour friter (fusionner) une poudre plastique. L’impression se construit couche par couche. Le processus est relativement simple : un rouleau, appelé recoater, étale une fine couche de poudre sur la surface de fabrication. Ensuite, un faisceau laser vient fusionner sélectivement certaines zones de la poudre selon le modèle défini, tandis que le reste de la poudre reste non fritté et sert de support naturel à la pièce en cours de construction.
La clé pour comprendre la technologie d’impression 3D SLS, c’est la température. Les imprimantes SLS fonctionnent dans un environnement fermé. La température dans la chambre est proche du point de fusion du matériau, et le laser n’apporte qu’un supplément de chaleur suffisant pour faire fondre la poudre. Grâce à cela, une fois que le laser termine le frittage d’une couche – processus qui relie les grains de poudre entre eux par des ponts de fusion – le refroidissement n’est pas aussi critique qu’en impression FDM, ce qui permet d’obtenir des connexions de particules presque aussi solides dans toutes les directions.
Un groupe de chercheurs issus du Marwadi Education Foundations Group of Institutions (Inde), de la Vaal University of Technology et de la North West University à Potchefstroom (Afrique du Sud) a mené une expérience presque identique à celle mentionnée précédemment avec le FDM. Ils ont étudié l’effet de l’orientation sur la résistance à la traction de pièces frittées au laser avec de la poudre PA12. Les échantillons ont été imprimés selon trois orientations différentes en utilisant une EOS Formiga P100. Les résultats ont montré que bien qu’il existe une variation de résistance à la traction entre les différentes orientations, l’écart reste relativement faible. La contrainte maximale moyenne observée variait entre 43,47 et 46,15 MPa. « Réduire l’anisotropie est souhaitable afin de permettre aux fabricants de construire des pièces dans n’importe quelle orientation sans compromettre les propriétés mécaniques des pièces produites » – indique le rapport.
Si la résistance mécanique est votre priorité, la technologie SLS peut s’avérer être un meilleur choix que le FDM. Vous n’obtiendrez pas des pièces aussi solides que celles issues de l’injection plastique, du thermoformage ou de l’usinage CNC, mais parmi les technologies de fabrication additive, le SLS peut sans doute être votre option numéro un.
Pièces creuses, légères mais solides
Le recours à la poudre non frittée comme support naturel dans la technologie SLS permet non seulement de produire des pièces sans renforts supplémentaires pendant le processus d’impression 3D, mais ouvre aussi la voie à des optimisations structurelles avancées. L’intégration de structures lattices, lorsqu’elle est bien réalisée, permet de concevoir des pièces à la fois plus légères et plus résistantes. Et ce n’est pas tout : cela permet également de réduire la quantité de matière utilisée pour l’impression, voire d’améliorer les capacités d’absorption d’énergie de la pièce.
Les structures lattices sont utilisées dans de nombreux secteurs, allant de l’automobile, au médical, en passant par le sport et d’autres produits grand public. Grâce à des logiciels comme Autodesk Fusion 360 et Netfabb, Gen3D Sulis, Materialise 3-Matic ou encore Altair Optistruct & Inspire, il est possible d’ajouter des structures lattices à un modèle sans avoir à les dessiner manuellement.
Même si ces structures peuvent être intégrées aussi bien en technologies SLS qu’en FDM, le processus est plus simple avec le SLS. En effet, lors du post-traitement, il n’y a pas de risque de les confondre avec des structures de support comme cela peut arriver avec le FDM.
Avantages et inconvénients des technologies FDM et SLS
Avantages du FDM
- Large gamme de matériaux d’impression
- Abordable – coûts d’équipement faibles à modérés
- Coûts de post-traitement faibles à modérés (retrait des supports et finition de surface)
- Idéal pour les pièces de taille moyenne à grande
- Composants quasiment sans porosité
- Excellente stabilité structurelle, résistance chimique, à l’eau et à la température des matériaux
- Volume d’impression plus grand que celui des autres technologies de bureau
Cons of FDM
- Les pièces imprimées sont beaucoup plus faibles dans la direction verticale à cause de l’anisotropie des propriétés du matériau
- Besoin de structures de support (mais pas systématiquement)
- La température dans la chambre d’impression ne peut pas être contrôlée précisément
- Moins précis que les technologies SLA ou SLS, avec un effet de « marches d’escalier » visible sur les plans verticaux
Avantages du SLS
- Pièces solides et durables
- Pas besoin de structures de support
- Intégration facile de structures lattices ou d’éléments creux
- Surfaces lisses – les couches sont à peine visibles
- La poudre peut être réutilisée après impression
Inconvénients du SLS
- Les objets imprimés sont de petite à moyenne taille
- Fonctionne de manière optimale avec des outils de post-traitement complets comme une station de traitement de poudre
- Le nettoyage de la machine doit être effectué avec précision lors du changement de matériau pour éviter toute contamination
- Plus coûteux qu’une imprimante FDM moyenne
Réduisez les coûts de votre impression 3D SLS
