Entwicklung von Medizinprodukten, der präzise Toleranzkontrolle der SLS LISA Lösung zugrunde liegt
- showing a design concept print multiple iterations of the parts
- prototype new products make significant leaps in timelines due to being able to rapidly prototype parts
- perform functional test how parts interact with one another and how ergonomic they feel
Background
The ECA Medical is the undisputed worldwide leader in single-use torque limiting. With 39 years experience partnering with world-leading implant companies and shipping more than 35 milion torque limiters, there is no better choice for experts in single-use torque limting.
Leading orthopedic implant companies turns to them to fill gaps in their portfolio. As healthcare shifts from free- for-service to value and as producers are increasingly growing in the outpatient segment, ECA Medical has quickly enabled these companies to make healthcare better by delivering pragmatic turn-key solutions
Problem
Fast prototyping has been a critical factor to reduce the time of product development. They used to have a couple of suppliers for 3D printing, but they needed more efficiency. They design products and molds internally, so the opportunity to have a real piece even in an early stage of the project is beneficial. Showing the customers a design concept transformed in a few hours into a real piece has changed.
In the past, ECA Medical outsourced its parts to get them printed, which not only cost a significant amount of money but also took many weeks at times. They often found that they did not have control of tolerances when outsourcing, received parts that did not end work due to the mating components.
Previously they used only in-house mold injection, when designing parts it is difficult and highly labor-intensive to do any type of interactive testing or prototyping, as they would need to develop manufacture, implement and troubleshoot the mold it once it was in the injection machine. If there was anything wrong with the model, they needed to change the design and start the whole process again. This procedure became time-consuming and expensive.
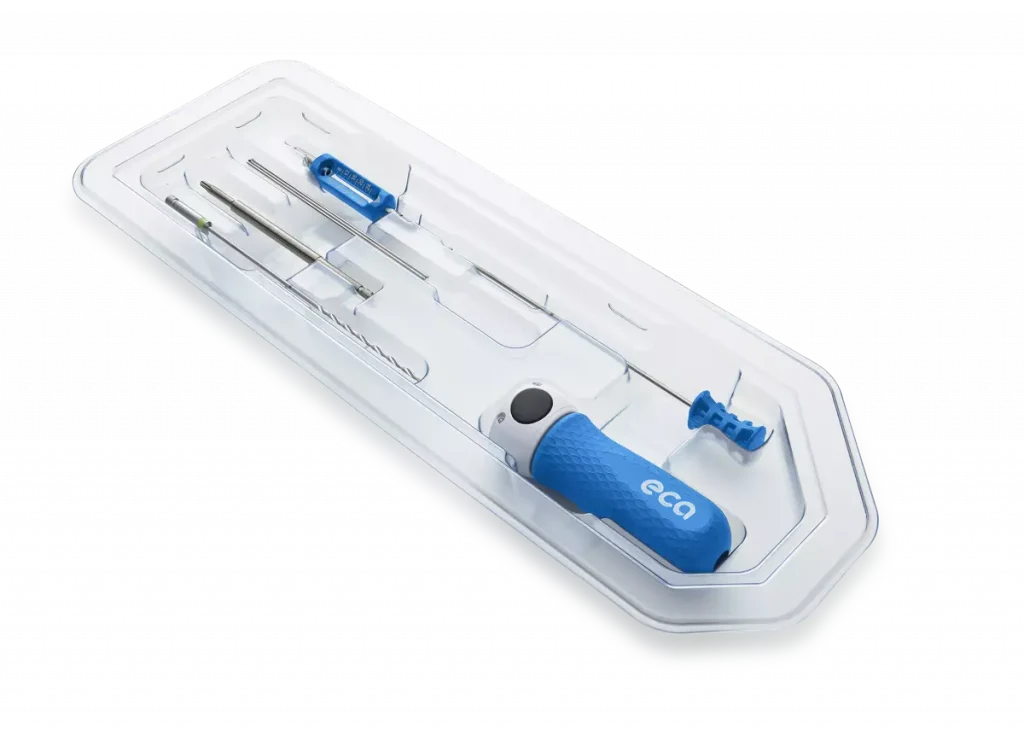
Solution
After looking for alternative design methods and doing research, ECA Medical decided to get the Lisa PRO printer. They have been using it for over a year; with in-house printing they can control the tolerance and orientation, make rapid changes and print multiple interations of parts that they could test in succession.
ECA Medical made significant leaps in timelines due to being able to rapidly prototype parts and quickly implement changes that need to be done on the next print build. With SLS, they can make most of those design changes on the printer, and once they felt they were ready and comfortable to get the part mold injected, they would proceed to that process. This saved a significant
amount of time and money.
Often ECA Medical tests fits to see how parts interact with one another and how ergonomic they feel. They have sent pieces to doctors and surgeons to get their feedback on handles that would be used in the operating room.
“One of the main benefits of SLS is the ability to print complex geometry in quick succession to do rapid prototyping.”

Visit our customer’s website:
- showing a design concept print multiple iterations of the parts
- prototype new products make significant leaps in timelines due to being able to rapidly prototype parts
- perform functional test how parts interact with one another and how ergonomic they feel