FDM vs SLA vs SLS : quelle technologie d’impression 3D est faite pour vous ?
Lorsqu’il s’agit de choisir une technologie d’impression 3D, il est essentiel de comprendre les avantages et les compromis propres à chaque méthode. Cette comparaison entre FDM, SLA et SLS met en lumière les principales différences en termes de matériaux, de qualité de surface, de coût, de vitesse d’impression et de liberté de conception. Que vous hésitiez entre la stéréolithographie et le FDM, ou que vous évaluiez le SLS face au SLA pour la réalisation de prototypes fonctionnels, ce guide vous offre une vue d’ensemble claire pour vous aider à sélectionner la solution la mieux adaptée à votre application.
Qu’est-ce que l’impression 3D FDM ?
La technologie FDM (Fused Deposition Modeling), également connue sous le nom de FFF (Fused Filament Fabrication), est la plus répandue et fait partie de la famille des procédés d’extrusion de matière. Elle utilise des matériaux thermoplastiques, généralement sous forme de bobines de filament. Une buse chauffée fait fondre le filament, qui est ensuite déposé couche par couche sur un plateau d’impression.
Le FDM présente plusieurs avantages : le procédé est facile à maîtriser, relativement rapide et peu encombrant. La majorité des imprimantes sont de format bureau, ce qui les rend parfaitement adaptées à un environnement de travail. Cependant, il existe également des systèmes FDM industriels de grande taille, utilisés dans des processus de fabrication, où le matériau est parfois utilisé sous forme de granulés plutôt que de filament.
Les entreprises comme les utilisateurs indépendants ont recours à la technologie FDM pour créer des prototypes fonctionnels, des maquettes de concepts produits ou des outils de production rapides. L’impression de modèles médicaux gagne également en popularité, certains fabricants ayant obtenu l’homologation FDA.
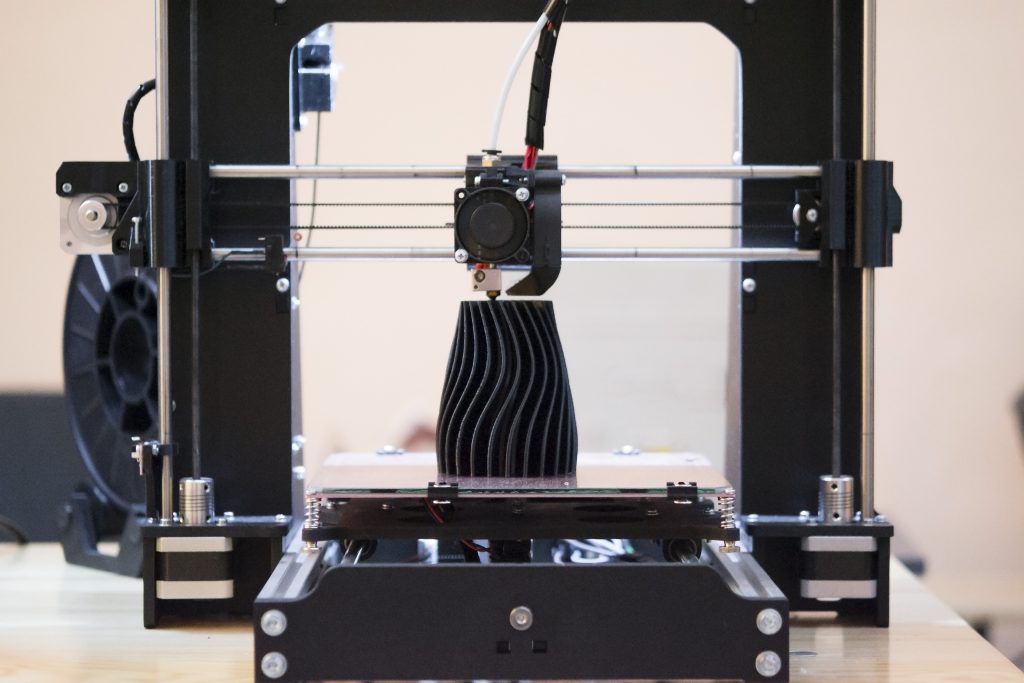
Comment concevoir pour l’impression FDM ?
Pour réaliser des modèles destinés à l’impression 3D FDM, il est nécessaire d’utiliser un logiciel de conception assistée par ordinateur (CAO) ou un logiciel de modélisation 3D. Cette technologie rencontre certaines limites lorsqu’il s’agit de pièces creuses, de contre-dépouilles ou de surplombs ; il est donc souvent indispensable d’intégrer des structures de support telles que des boîtes, des toits ou des treillis pour assurer l’imprimabilité des pièces.
Heureusement, les logiciels d’impression analysent automatiquement la géométrie des modèles et génèrent les supports adéquats. Les imprimantes FDM équipées d’un seul extrudeur fabriquent ces structures à partir du même matériau que celui utilisé pour le modèle principal, ce qui implique un retrait mécanique une fois l’impression terminée.
Les imprimantes équipées de deux extrudeurs ou plus gagnent en popularité. Cette configuration permet d’utiliser un matériau de support soluble dans l’eau. Toutefois, le processus de dissolution est relativement long et, dans certains cas, l’eau ne suffit pas : un agent comme l’acide citrique est parfois requis.
Il faut également noter que tous les matériaux d’impression ne sont pas compatibles avec les supports solubles. Un autre facteur critique à prendre en compte est l’orientation du modèle sur le plateau de fabrication. Celle-ci doit être optimisée pour limiter autant que possible l’usage de structures de support.
Avantages de l’impression 3D FDM
- La technologie FDM est globalement non toxique, bien que certains filaments comme l’ABS puissent émettre des fumées nocives lors de l’extrusion. Dans l’ensemble, il s’agit d’un procédé considéré comme respectueux de l’environnement.
- Elle permet l’utilisation d’un large éventail de matériaux d’impression colorés, accessibles en termes de coût et offrant un taux d’utilisation élevé.
- Les équipements FDM présentent des coûts d’acquisition faibles à modérés, tout comme les coûts de post-traitement liés au retrait des supports et à la finition des surfaces.
- La technologie est particulièrement adaptée à la fabrication de pièces de taille moyenne. Les composants imprimés présentent une porosité quasi nulle, ce qui assure une excellente stabilité structurelle. Les matériaux utilisés offrent également de bonnes propriétés de résistance chimique, thermique et à l’humidité.
- Enfin, le volume d’impression est relativement important par rapport aux autres technologies de bureau, atteignant jusqu’à 600 × 600 × 500 mm.
Limites et inconvénients de la technologie FDM
- Autres limitations du procédé FDM. La technologie FDM impose certaines contraintes de conception. Elle ne permet pas de réaliser facilement des parois fines, des angles aigus ou des arêtes vives dans le plan vertical.
- Les modèles imprimés présentent leur plus faible résistance dans la direction de construction verticale, en raison de l’anisotropie introduite par le processus de dépôt couche par couche. Cette caractéristique rend les pièces plus fragiles perpendiculairement aux couches.
- L’usage de structures de support est souvent indispensable, notamment pour les surplombs et les géométries complexes.
- La précision d’impression reste limitée, avec une tolérance généralement comprise entre 0,10 et 0,25 mm.
- En termes de performances mécaniques, la résistance à la traction d’un objet FDM atteint environ les deux tiers de celle d’une pièce fabriquée par injection avec le même matériau.
- Le contrôle de la température de la chambre de fabrication est un autre défi : il est difficile à stabiliser, alors qu’il est essentiel pour garantir la qualité des impressions, surtout avec les polymères techniques.
- Enfin, le phénomène de « stair-stepping » (effet de marches) est fréquent dans le plan vertical, ce qui altère la finition visuelle et peut nécessiter un post-traitement pour lisser les surfaces.
Webinaire
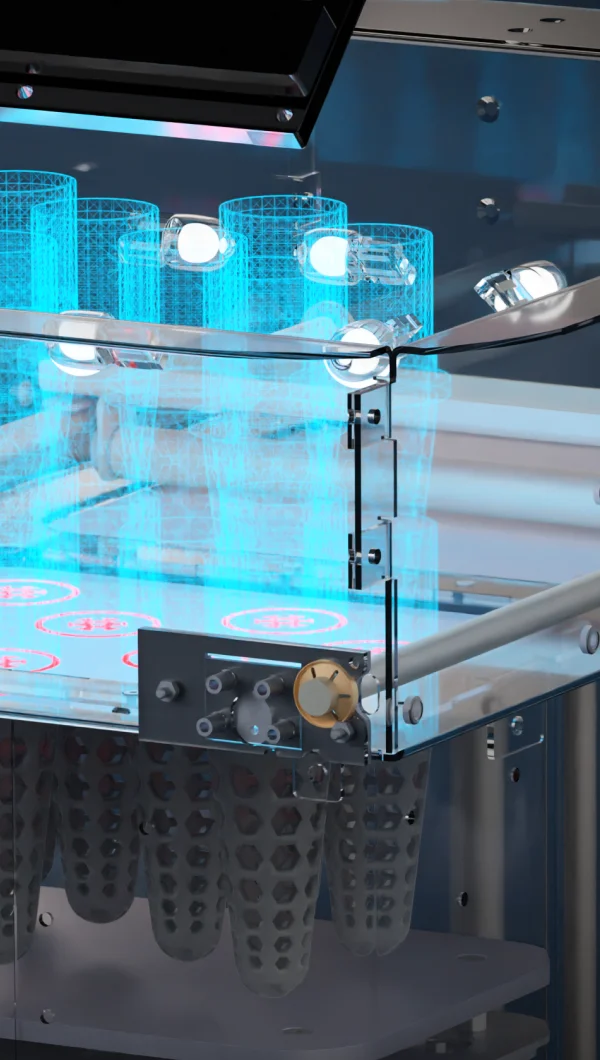
Qu’est-ce que l’impression 3D SLA ?
Le deuxième procédé le plus répandu, appelé SLA (stéréolithographie), fait partie de la famille des technologies de photopolymérisation en cuve (vat photopolymerization). Il s’agit de la toute première technologie de fabrication additive à avoir été brevetée.
Dans ce processus, une cuve contenant une résine photopolymère liquide est exposée à un faisceau laser ou à un projecteur de lumière numérique. La source lumineuse durcit sélectivement la résine, couche par couche, directement sur la plateforme de fabrication.
Une fois la couche solidifiée, la plateforme s’élève légèrement et une nouvelle couche de résine recouvre la surface pour répéter l’opération. Il est crucial que la cuve soit entièrement fermée afin d’empêcher l’échappement des vapeurs de résine. De plus, la chambre doit être opaque ou teintée pour éviter que la lumière ambiante ne vienne durcir prématurément la résine.
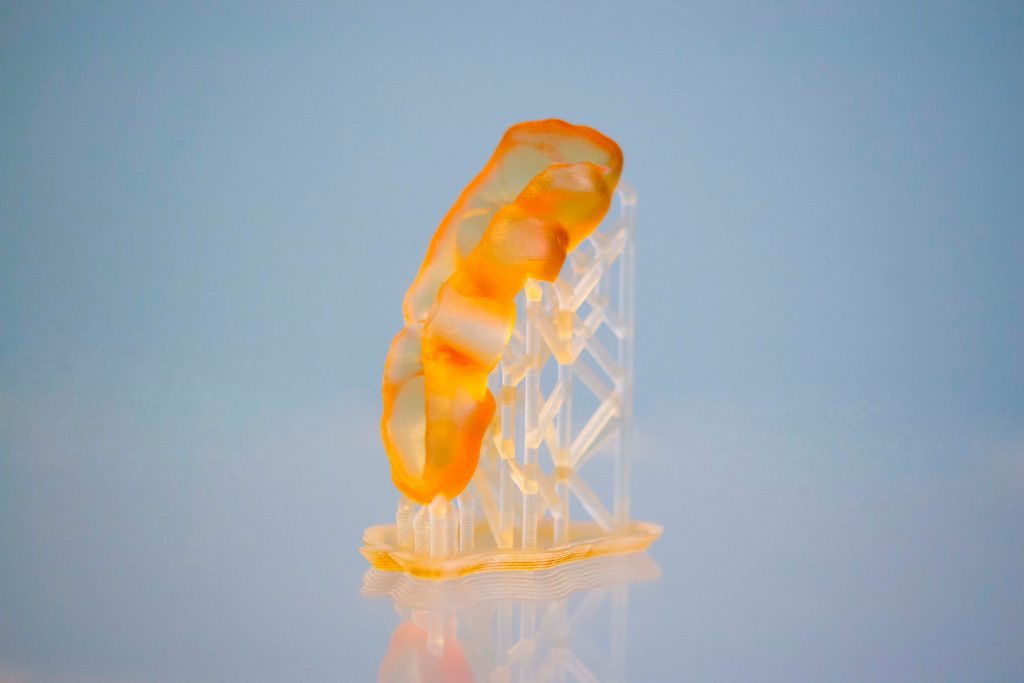
Dans la stéréolithographie, tout comme en FDM, des structures de support sont nécessaires. Cependant, dans ce cas, elles sont toujours fabriquées à partir du même matériau que la pièce elle-même. Une fois l’impression terminée, la pièce est d’abord égouttée, puis nettoyée dans un solvant afin d’éliminer l’excès de résine. Elle est ensuite exposée à une lumière UV pour finaliser la polymérisation et durcir complètement le composant. Ce n’est qu’à ce stade que les structures de support peuvent être retirées, généralement par découpe mécanique.
La technologie SLA permet l’utilisation d’un large éventail de photopolymères, notamment l’époxy, l’uréthane, les acrylates, les élastomères et le vinyle. Ces matériaux sont adaptés à la fabrication de prototypes non fonctionnels, d’assemblages à encliquetage, de charnières, de modèles médicaux – en particulier dans le domaine dentaire – ainsi que de modèles maîtres pour les applications de moulage.
SLS (Selective Laser Sintering) : impression industrielle sans supports
Lors de la conception de modèles pour la stéréolithographie (SLA), il convient de respecter des règles très similaires à celles de la technologie FDM. En raison de la nécessité de structures de support, la pièce doit être orientée de manière à réduire au maximum leur utilisation. Dans le cas du SLA, les supports peuvent prendre la forme de treillis, de points d’ancrage, de voûtes ou de renforts.
Les pièces obtenues en SLA sont généralement translucides, avec une épaisseur de couche pouvant atteindre 0,05 à 0,15 mm.
Points forts de l’impression SLA
- Excellente finition de surface grâce à une épaisseur de couche fine, comprise entre 0,05 et 0,15 mm
- Pièces imprimées pouvant être peintes après traitement
- Vitesse d’impression modérée
- Rentable pour les petites séries (1 à 20 pièces)
Inconvénients et risques de la stéréolithographie
- Matériaux coûteux.
- Le post-traitement est non seulement nécessaire, mais aussi complexe et salissant. Une fois l’impression terminée, la résine doit être nettoyée dans un bain à ultrasons ou en immergeant la pièce dans de l’alcool isopropylique (IPA), puis les supports doivent être retirés, et enfin les impressions doivent être durcies à la lumière UV.
- La résine seule est toxique, mais mélangée à l’IPA, elle devient encore plus dangereuse. Ce liquide doit être sécurisé et envoyé à une entreprise spécialisée pour son élimination.
- Les déchets ne sont pas recyclables et sont difficiles à gérer.
- Des structures de support sont nécessaires.
- Les impressions sont les plus faibles dans la direction verticale de fabrication en raison de l’anisotropie des propriétés du matériau liée au procédé additif.
- Le laser doit être calibré périodiquement.
- L’épaisseur de couche peut varier selon les résines.
- Les photopolymères sont toxiques, tout comme les fumées émises pendant le processus.
Qu’est-ce que l’impression 3D SLS ?
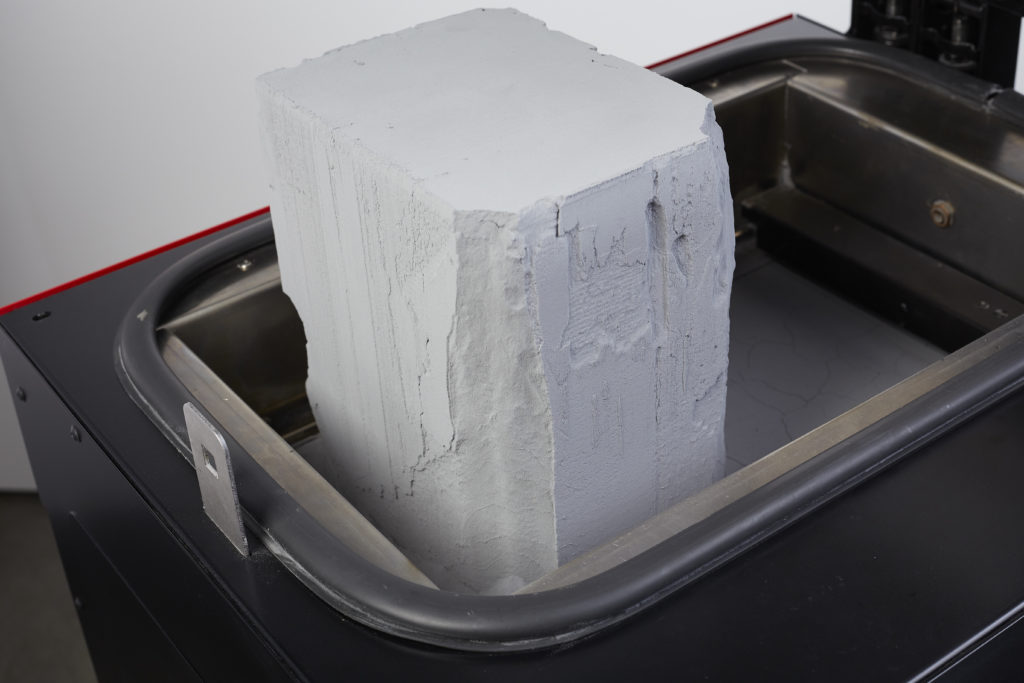
Le SLS est l’une des technologies les plus anciennes de l’industrie de l’impression 3D, la plus connue et, à ce jour, la plus prévisible parmi les méthodes de fabrication additive. Son fonctionnement est très simple. Un faisceau laser fritte un matériau en poudre dans une chambre fermée, parfois sous atmosphère inerte afin d’éviter l’oxydation. La chambre est préchauffée juste en dessous de la température de fusion de la poudre, et le laser n’apporte qu’une faible quantité d’énergie supplémentaire pour fondre le matériau.
Une fois le frittage d’une couche terminé, les plateformes se repositionnent et un mécanisme dédié répartit une nouvelle couche de poudre depuis une chambre d’alimentation vers la zone d’impression, et le processus est répété. En technologie SLS, aucun support n’est nécessaire car la poudre non frittée, entourant les pièces dans la chambre d’impression, joue naturellement le rôle de support.
La précision de la technologie SLS dépend du faisceau laser, de son diamètre et de la manière dont il est piloté : perpendiculairement à la couche (H-BOT) ou selon un angle (Galvo). Elle dépend également de la hauteur de couche. Toute structure complexe et massive peut être réalisée, y compris avec des pièces mobiles internes, à condition que le design de l’objet permette d’évacuer la poudre non frittée emprisonnée à l’intérieur du modèle.
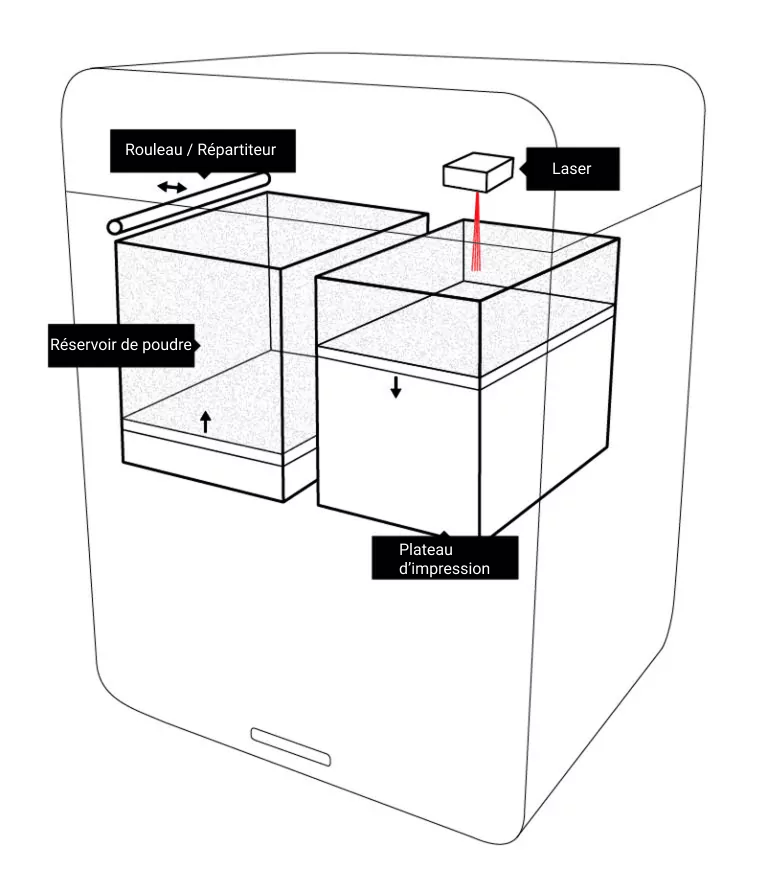
Après l’impression, l’excédent de poudre peut être simplement éliminé par aspiration ou brossage. Pour obtenir un résultat optimal, la pièce imprimée peut également être sablée. Le frittage sélectif par laser utilise une large gamme de matériaux tels que les thermoplastiques, les élastomères et les cires. Certaines machines industrielles fonctionnent également avec des poudres métalliques (SLM, DMLS, LPBF) ou des céramiques.
Si l’on compare le nombre d’applications entre le SLS, le SLA et le FDM, le frittage sélectif par laser occupe incontestablement la première place avec le plus grand éventail d’applications potentielles. Il permet de réaliser des prototypes fonctionnels et articulés pouvant être testés en soufflerie ou soumis à d’autres essais expérimentaux, mais aussi des pièces finales produites en petites ou moyennes séries. Les domaines d’utilisation incluent les éléments d’assemblage ajustés, les clips et charnières, l’outillage rapide, les modèles maîtres, les noyaux et moules pour les procédés de moulage, les maquettes de concepts produits, ainsi que les implants médicaux et dentaires. Cette technologie est également utilisée à des fins pédagogiques, tant par les chercheurs que par les enseignants pour la formation des étudiants.
Conception de pièces pour le SLS
Les concepteurs choisissent la technologie SLS car elle offre une grande liberté de forme. Il est possible de créer des pièces mobiles avec une géométrie complexe. Comme aucune structure de support n’est requise, il est également plus facile de concevoir des projets détaillés, avec des arêtes vives et des parois fines. Une épaisseur de couche comprise entre 0,06 et 0,15 mm permet d’obtenir une grande précision. Comme pour le FDM et le SLA, l’anisotropie des propriétés mécaniques rend les pièces plus fragiles dans la direction verticale de fabrication.
Avantages de la technologie SLS
- Aucune structure de support nécessaire
- Pièces mobiles avec géométrie interne complexe
- Surfaces lisses – les couches sont à peine visibles
- Pièces durables
- La poudre est réutilisable après impression
- Coût des matériaux faible à modéré, tout en utilisant toute la surface de travail
- Les imprimantes SLS de bureau sont peu coûteuses comparées aux machines industrielles
- Aucun personnel hautement qualifié n’est requis (dans le cas des modèles de bureau)
Inconvénients du frittage sélectif par laser
- Les machines industrielles sont coûteuses
- Délais de production longs
- Le nettoyage de la machine doit être très rigoureux lors d’un changement de matériau pour éviter toute contamination
- Temps d’impression long (notamment pour les grandes pièces)
- Pour la gestion de la poudre lors du post-traitement, un aspirateur et de l’air comprimé sont recommandés, car le procédé est poussiéreux
Impression SLA vs SLS : Comparaison approfondie
Lorsqu’on compare les technologies de fabrication additive, la SLA (stéréolithographie) et le SLS (frittage sélectif par laser) représentent deux approches avancées mais fondamentalement différentes de l’impression 3D — chacune optimisée pour des applications spécifiques et des comportements matière distincts.
La SLA utilise un laser UV pour polymériser une résine photopolymère liquide, couche par couche, dans une cuve. Ce procédé permet d’obtenir des impressions d’une résolution exceptionnellement élevée, avec une finition de surface très lisse, ce qui en fait une solution idéale pour les prototypes visuels, les modèles dentaires, les maîtres-modèles en joaillerie et les composants de précision. Cependant, la SLA nécessite des structures de support, ce qui peut limiter la complexité géométrique des pièces et impose souvent un post-traitement manuel pour les retirer.
Le SLS, en revanche, emploie un laser haute puissance pour fritter des poudres thermoplastiques, telles que le PA12, le PA11 ou le TPU, afin de créer des objets solides couche par couche. La poudre non frittée qui entoure les pièces pendant l’impression agit comme un support naturel, ce qui élimine le besoin de structures de soutien et permet de fabriquer des géométries complexes, imbriquées ou articulées. Les pièces obtenues sont généralement plus robustes et fonctionnelles, ce qui rend la technologie SLS parfaitement adaptée à la production en petites séries, aux prototypes fonctionnels et aux composants finis dans des secteurs comme l’automobile, l’aéronautique ou les dispositifs médicaux.
D’un point de vue performance, la comparaison SLA vs SLS repose sur un compromis entre esthétique de surface et résistance mécanique. Les pièces SLA offrent une clarté optique élevée et un niveau de détail très fin, mais elles sont en général plus cassantes et moins performantes en termes de résistance thermique. Les pièces SLS, bien que leur finition soit plus granuleuse, présentent une meilleure résistance aux chocs, une capacité de charge supérieure et une excellente stabilité thermique — notamment lorsqu’elles sont imprimées avec des polymères techniques.
En définitive, le choix entre SLA et SLS dépend des priorités de l’application. Pour la visualisation de designs complexes ou le rendu de détails ultra-fins, la SLA reste inégalée. Pour la durabilité, la liberté de conception et l’évolutivité en production, le SLS est la solution industrielle de référence.
FDM vs SLA vs SLS : Tableau de comparaison rapide
Paramètre | Fused Deposition Modeling | Stereolitography | Selective Laser Sintering |
---|---|---|---|
Abréviation | FDM | SLA | SLS |
Principe de fonctionnement | Extrusion de filament fondu | Photopolymérisation par UV | Frittage laser de poudre |
Matériau utilisé | Polymère thermoplastique sous forme de filament (PLA, ABS, etc.) | Résines liquides photopolymérisables | Poudres polymères frittables (polyamides, TPU, TPE) |
Avantages | Faible coût Temps d’impression rapide | Haute résolution d’impression Automatisation du processus | Pas besoin de structures de support Qualité Prototypage Pièces articulées |
Inconvénients | Structures de support nécessaires Retrait thermique du filament | Gamme de matériaux limitée Coûts d’entretien élevés | Temps d’impression long |
Applications | Prototypage rapide Éducation Production en petite série | Éducation Production en petite série Prototypes à géométrie interne complexe Modèles dentaires | Éducation Prototypes fonctionnels Modèles médicaux Prototypage Pièces articulées |
Épaisseur de couche | 0,1 – 0,3 mm | 0,05 – 0,15 mm | 0,060 – 0,15 mm |
Impression sans structures de support | Non | Pas toujours nécessaire | Oui |
Impression de pièces articulées | Pas toujours réalisable (précision moindre) | Non | Oui |
FAQ impression 3D : FDM, SLA ou SLS ?
FDM (Fused Deposition Modeling) et SLA (Stéréolithographie) sont deux des technologies d’impression 3D les plus courantes, mais leur fonctionnement est très différent. Le FDM dépose du filament thermoplastique fondu couche par couche, tandis que le SLA utilise un laser ou projecteur UV pour durcir de la résine liquide. Le SLA offre généralement une meilleure précision et une qualité de surface supérieure, alors que le FDM est plus économique et plus simple à utiliser.
Oui, le SLA est en général plus précis. Les imprimantes SLA peuvent atteindre des résolutions de couche aussi fines que 0,05 mm, idéales pour les détails complexes. Le FDM fonctionne plutôt entre 0,1 et 0,3 mm, avec des couches plus visibles. Pour les projets nécessitant une surface lisse et une grande précision, le SLA est clairement favorisé.
Le SLA offre une finition de surface plus lisse, une précision accrue et un meilleur rendu des détails — particulièrement important pour les modèles dentaires, les bijoux et les prototypes de haute qualité. Il est donc souvent préféré pour les pièces de présentation ou à tolérances serrées. Cependant, les matériaux SLA sont plus coûteux et le post-traitement est plus exigeant.
Le SLS est généralement préférable pour les prototypes fonctionnels. Bien que le SLA offre une excellente qualité visuelle, ses pièces sont plus cassantes et moins adaptées aux contraintes mécaniques. Le SLS fournit des pièces robustes, résistantes à la chaleur, idéales pour des tests réels ou de petites séries fonctionnelles.
En règle générale, non. Les imprimantes FDM ne peuvent pas égaler la résolution ni la finition de surface des machines SLA. Le SLA reste supérieur pour les modèles nécessitant finesse et esthétisme, même si les FDM modernes peuvent produire des résultats acceptables pour des prototypes de base.
Le SLA est utilisé pour les modèles dentaires, les prototypes visuels et les pièces moulables. Le SLS est préféré pour des pièces fonctionnelles, résistantes, des assemblages clipsables ou des composants finaux en petites séries. Le SLS domine en robustesse et en polyvalence.
Non. Le SLS n’a pas besoin de structures de support. La poudre non frittée environnante sert de soutien naturel, ce qui permet une plus grande liberté de conception et l’impression de géométries complexes, imbriquées ou internes.
Le SLS est la meilleure option pour les pièces mobiles ou articulées. Grâce à l’absence de supports et à la précision du frittage de poudres haute performance, il permet d’imprimer des mécanismes emboîtés en une seule opération. Le FDM et le SLA sont moins adaptés à ce type d’application.
Oui. Le FDM est généralement la technologie la plus abordable, tant pour l’équipement que pour les matériaux. Il convient parfaitement à l’enseignement, aux loisirs et au prototypage simple, même s’il est moins performant en précision et en finition.
Le SLA fournit une meilleure finition de surface et des détails plus nets. Le SLS, en revanche, produit des pièces plus solides et plus adaptées à un usage fonctionnel. Le choix dépend de vos priorités : esthétique (SLA) ou performance mécanique (SLS).
Le SLA utilise un laser pour durcir de la résine liquide et produire des pièces très détaillées avec une surface lisse. Le SLS utilise un laser pour fritter de la poudre polymère (nylon, TPU, etc.) sans nécessiter de supports, pour des pièces solides et complexes.
Oui, le SLS est souvent préféré pour les pièces fonctionnelles grâce à sa robustesse, sa résistance thermique et sa capacité à produire des géométries complexes sans supports. Le SLA excelle en précision mais reste fragile.
Optez pour le SLA lorsque l’apparence visuelle, la résolution fine et les finitions lisses sont primordiales (modèles dentaires, prototypes visuels, bijoux). Choisissez le SLS lorsque la durabilité, la performance mécanique et l’évolutivité sont essentielles.